Speed To Market: The Essential Role Of Preconstruction
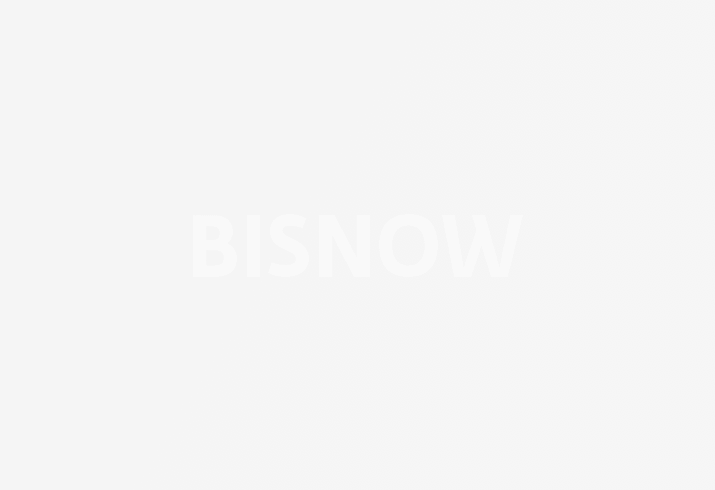
Construction costs continue to rise as the NYC Metro market building boom continues.
The Turner Building Cost Index, an industry standard that measures nonresidential U.S. construction costs, has risen 5.63% since last year. A competitive construction market, coupled with a growing skilled labor shortage and escalating tariffs, has helped fuel this increase.
A primary driver of increased construction costs is delays to market. According to a 2015 KPMG report, only 25% of construction projects come within 10% of their original deadlines. But for many of these projects, cost and schedule overruns are preventable.
Preconstruction — the period during which construction partners, architectural and engineering teams and stakeholders collaborate on a project at the earliest opportunity to develop baseline schematics, affirm constructability, source materials, create budgets and determine schedules — can prevent delays and unexpected costs.
“We emphasize preconstruction,” Talisen Business Unit Director Christopher Norris said. “Ideally, you want as much time as possible to plan, but in our challenging industry, time is not always a luxury that can be afforded.
"Any timeline reserved for a collaborative 'precon' exercise is time and money well spent. Our challenge as a construction partner in the overall building process is ensuring a delighted client and the preconstruction phase helps bring all the key parties together prior to breaking ground for a collaborative process. Digging in to pinpoint what the client’s needs are, what the potential obstacles are in the design and construction phases and how budgets and schedules can be aligned to final scope achieving the final product is an incredibly valuable process for everyone involved.”
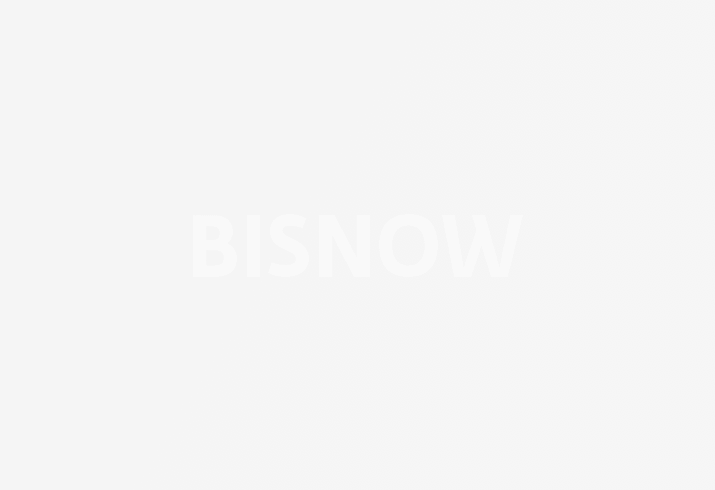
Preconstruction collaboration between the end user, designers and construction partner is effective in building a cohesive team working together from the beginning and creates a unified front in the best interests of the project. This enhances each team member’s contribution as a unit instead of separate parties and diminishes adversarial positions of each stakeholder protecting their own interests. Preconstruction helps the team focus on a shared interest: a successful project.
The essentials of preconstruction span contract type. Whether the contract structure is a stipulated sum or guaranteed maximum price, the benefit of a rigorous precon exercise is universal. Precon service fees are money well spent, and in many cases, even with a lump sum construct, these fees can be absorbed into the overall budget with high return on investment. Building a project on paper first, with stakeholder, architecture and engineering teams and the construction partner in full collaboration, is more economical and efficient than doing so at the construction phase alone, Norris said.
On its most recent healthcare project, Talisen, in partnership with the owner, Northwell Health and TPG Architecture with engineering from Bladykas Engineering, transformed a former 27K SF water-treatment facility located in Lynbrook, New York, into a premier medical office building offering full cardiology, family medicine, gastroenterology, internal medicine and pulmonology services.
The completed project, which included a three-story building extension, mechanical, electrical and plumbing infrastructure, elevators, and new exam and office spaces, benefited from an extensive preconstruction period. Northwell’s Lynbrook MOB stands as a template to the advantages of preconstruction partnerships.
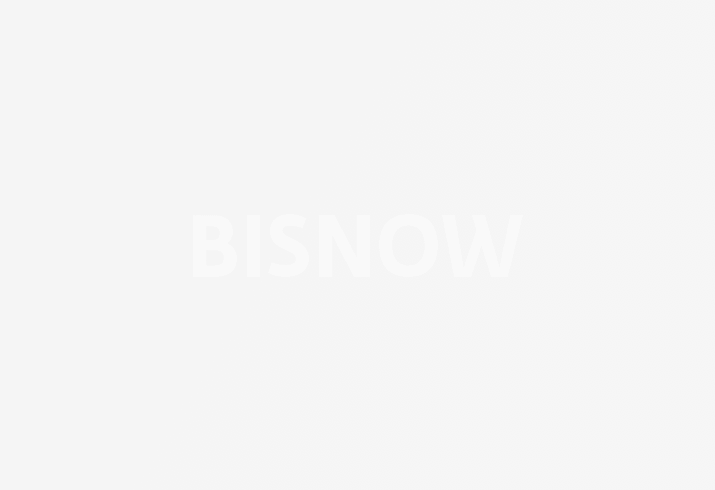
Built in the 1940s, the building had suffered from the impacts of time and weather prior to Northwell’s acquisition. A typical design approach would have addressed the full gut of the facility and the subsequent build-out. What the typical process would not have necessarily addressed is the overall constructability, schedule constraints and, in the case of Northwell’s Lynbrook MOB, the ability to quickly respond to “found conditions.”
In this case, the building needed extensive asbestos-containing material remediation and a facade that required an 85% replacement due to structural deficiencies that wouldn’t have been discovered in the typical design process.
Without the diligent preconstruction period and the partnership developed between Northwell, TPG and Talisen, the flexibility and speed required to overcome these challenges would have resulted in a schedule overrun with subsequent brand and cost impact.
“By doing this preplanning early, you start removing the roadblocks to a successful, cost-efficient and timely project,” Norris said. “If you were to project out encountering the same issues, without identifying them early through the preconstruction phase, the impact to time and cost can be significant.
“Having the construction team at the table during schematic program design is instrumental in allowing fluid budgets, real-time value engineering, scheduling and overall constructability in concert with efforts by the architect and engineer,” he added. “Hammering out these issues weeks or months in advance allows us to plan for these potential issues, thus avoiding potentially significant schedule and or cost delays. This approach also offers the opportunity to initiate the construction in earlier, 'preliminary' phases, allowing predecessor tasks such as foundation and steel to progress in field, while the final designs on 'successor' aspects, such as finishes, can still be in process.”
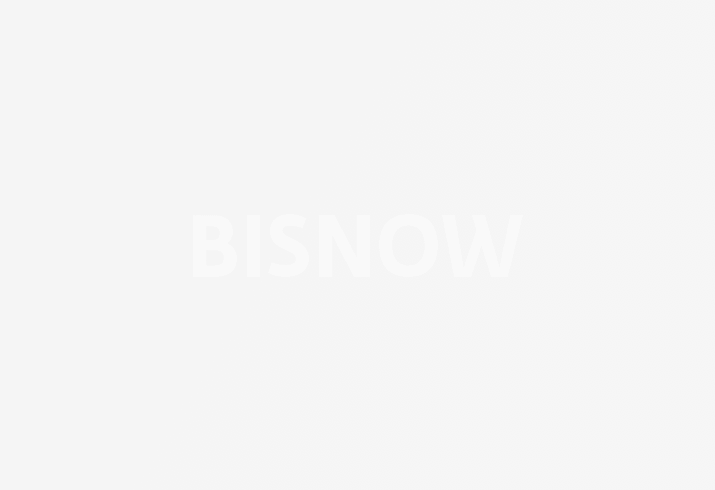
For example, with Northwell’s approval, contingency funding was used to bring in Becker Engineering to do a detailed engineered assessment of the facade work. This assessment was executed in concert with South Ferry Construction, the project’s masonry contractor, to develop a detailed drawing based on the new findings for final review and approval by TPG. Stakeholders then decided to expedite the work to stay on schedule for Northwell's end of April 2018 opening.
By conducting assessments ahead of time, Talisen salvaged, and even expedited, the overall schedule, despite a scope increase of nearly 350% of the overall masonry work required for completion.
The Northwell Lynbrook MOB had been initially slated for a full, 13-month construction period at the point of schematic design. Using these techniques and with a collaborative team approach, the timeline was shortened to eight months, without compromise to initially designated budget constraints.
The cost of construction is not softening any time soon, but there are strategies clients, architects and construction partners can use to save time and money. Preconstruction should be a primary tool in this effort to bring successful projects, such as Northwell’s Lynbrook MOB, to market in record time.
This feature was produced in collaboration between Bisnow Branded Content and Talisen Construction. Bisnow news staff was not involved in the production of this content.