Modular Construction Can Save Time And Money, But It's Not 'A Magical Fix'
Modular construction isn't a new concept, but it still hasn't gained a foothold.
For many developers and contractors working in the industry, that's a major missed opportunity. They attribute the lag on modular adoption to modular construction being misunderstood.
"Everyone’s looking for a way to cut costs on construction without sacrificing quality, design, long-term sustainability of the property," UrbanCore Development President Michael Johnson said at Bisnow’s National Off-Site Construction digital summit. "But the only way you can save money with prefab is in the execution."
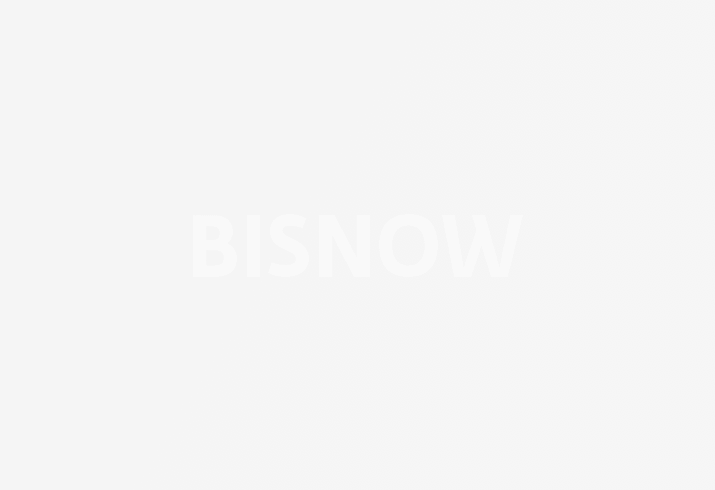
Johnson, along with DMG Investments Chief Operating Officer Jeffrey Amengual, Clark Pacific Managing Director Greg Otto and Vantis co-founder Ryan Ware, said there's potentially a lot of money that can be saved. A June 2019 report from McKinsey & Co. found that modular construction had the ability to speed up construction as much as 50% and that "in the right environment" it could shave 20% off construction costs.
Johnson's UrbanCore has used modular construction to complete two projects, one in Oakland and another in Sacramento. Johnson previously told Bisnow that using prefabrication had delivered roughly 10% hard-cost savings on an Oakland mixed-income development. Savings can be especially important on projects where below-market-rate units are included.
A 100% affordable housing project in Sacramento was able to bring per unit costs down to $385K per unit through modular construction instead of the $525K per unit it would cost to be traditionally constructed, the San Francisco Chronicle reported in November. The 143-unit project was also delivered 40% faster than the typical affordable development.
While modular construction's potential advantages draw developers and builders in, many developers looking to dip a toe into using prefab in their project fail to recognize that a modular project needs to be visualized from its inception as such.
"We have to take a page out of the automotive industry's book," Amengual said. "We wouldn’t be designing vehicles halfway through production.”
Site selection and design are different for prefab projects. And there are new challenges, like shipping the prefabricated components and balancing the work that gets done off-site with the work that gets done on-site.
Often, prefab is considered “a magical fix” for the problems in the traditional construction industry, but without an acknowledgement of the new considerations that have to be made for a prefab project to succeed, Clark Pacific's Otto said.
"It really takes a mindset shift in thinking about how you’re going to integrate it," Vantis' Ware said.