Game-Changer Or Game-Ender? Construction Grasps For A Handle On New Tech
Those in the business are united that artificial intelligence and other new tech will revolutionize the development and construction industries. But whether the coming wave will push out half of all employees or usher in a new generation of professionals capable of harnessing its power depends on who you ask.
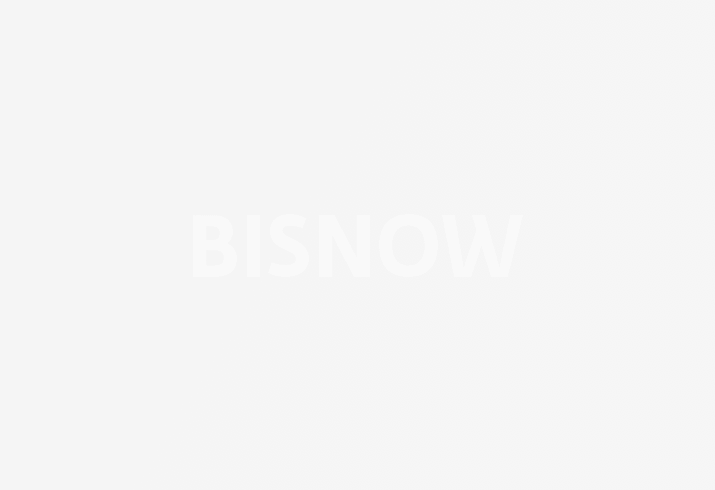
“The most dangerous words in the development and construction technology department are ‘That’s how we’ve always done it,’” Pontikes Development Vice President of Construction and Design Nick Pontikes said at Bisnow’s Houston Construction Trends and Innovation event at POST Houston on Wednesday.
With the market challenged by difficulty securing financing, high costs and supply chain issues, panelists said it is important to examine new ways of making things work. That includes a number of new technologies and methods shaking up construction, from 3D printing and prefabricated and modular construction to mass timber.
But AI is poised to be the biggest game-changer of them all in the industry known to require many repetitive tasks, Pontikes said. And it is one capable of eliminating numerous jobs — and a lot of human error.
“I can imagine construction projects that have half the teams on them that are able to run more efficiently,” Pontikes said, adding that AI will take gut feelings and guesswork out of processes.
An AI system can take years of historical pricing data and use it to compute efficient apartment layouts, he said.
“You’re looking at one person doing a job that it used to take a whole company to do,” Pontikes said. “For it to generate that, I don’t think we need to talk about impacts that’s going to have on pricing and a lot of people’s jobs in this room.”
AI doesn't necessarily mean mass job loss, at least not across the board, and it offers a boon to speed and efficiency
HOK is looking at AI from a value-add perspective, HOK Technical Principal Thomas Bayer said. That means applying it to low-value or repetitive tasks at the early prototyping stage of a project, allowing the company to quickly review 30 different options.
Processes that would usually take months to accomplish now take just a fraction, and getting them done quickly frees up design professionals to focus on higher-value issues, Bayer said.
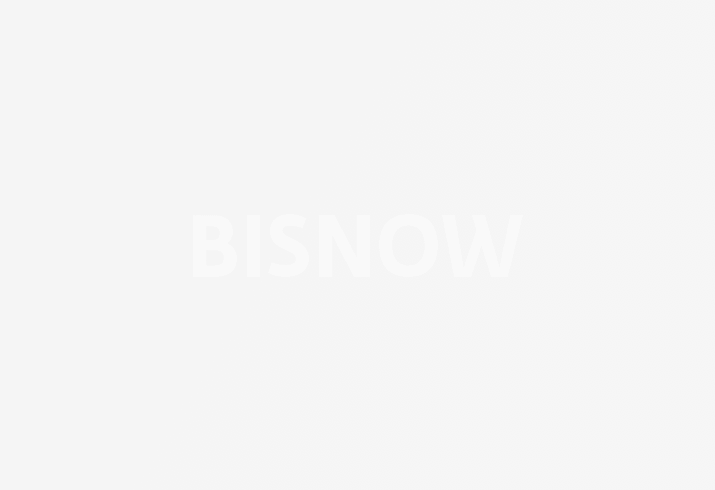
Tellepsen is using AI to help with its construction scheduling by filling in gaps and validating assumptions, CEO Tadd Tellepsen said.
The potential is huge. After playing with AI image generators, Tellepsen said he couldn’t help but wonder when he would be able to tell an AI system to generate a building design with all requested specifications and have the results almost instantly.
Yet one of the most practical ways Tellepsen is seeing AI used right now is to answer questions for employees who are new to the industry.
“It’s so much more efficient than just asking Google,” Tellepsen said. “It gives you very readable explanations of terms and methods. I’m watching that happen in the office now.”
Other technology is also making a mark. CIVE, a Houston-based design-build firm, is constructing America’s first fully 3D-printed two-story house in Houston.
CIVE President Hachem Domloj likened the project to a research effort that has sparked a number of ideas for improving the technology. One needed improvement CIVE has uncovered is greater mobility: Once a printer is set in place, it must stay fixed in position until an entire section is complete.
But opportunities are abundant, he said.
“With 3D printing, you can print anything that you can basically think of that is constructible,” Domloj said. “There are some limits, but you can print some very complicated designs in less time.”
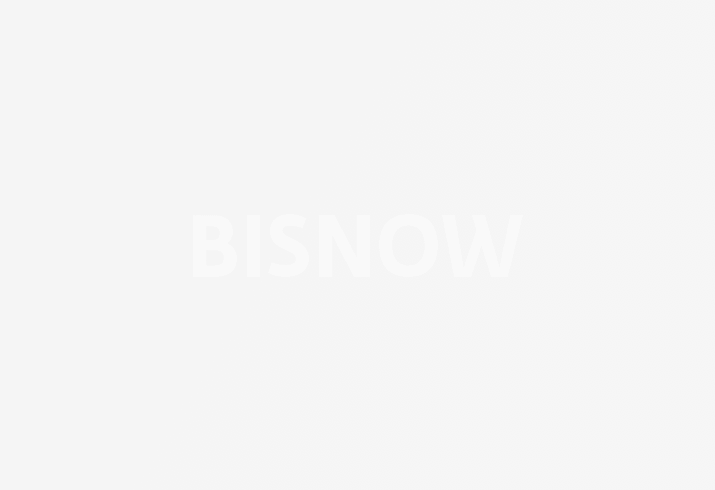
While it might be ahead in some technologies, in others, Houston is lagging. Prefabricated and modular construction is seen more often in places like New York City, where unions drive up the cost of labor, Pontikes said.
CIVE tried prefabrication on a multifamily project and found it to be a success, saving a lot of time, Domloj said. Still, legislation will likely be needed to make innovative construction methods more affordable and attainable, WC Construction President Will Carter said.
“[When] we present these ideas to our clients, everybody seems to be interested,” Carter said. “But then the majority of them, once it gets down to budget, that’s one of the first areas they look to cut, unfortunately.”
Tellepsen saw how important it was to start educating the market, the city and code enforcement officials early on in its San Jacinto College mass timber project, Tellepsen said. Tellepsen and the firm's client started those conversations a year early.
“As modular comes, we’re going to have to get way ahead of it,” he said. “Education, namely, for city permitting, code enforcement and subcontractors. Because they don't know how to handle this. It’s something new.”
In Houston, the cost of labor is still low enough that the time savings don't make up for the cost of modular construction, Pontikes said. But the cost of labor is rising.
“It's getting close. And every year, we're waiting for it to flip,” Pontikes said. “When it does, it's going to be truly groundbreaking.”