Next Stop, Apartments: 2-Story 3D-Printed House Lays Foundation For Bigger Projects Ahead
Making construction cheaper, safer and more efficient sounds like a bold promise, but advocates of 3D printing say the technology is up to the challenge.
Now, one ongoing project in Houston could help apply that construction method to bigger projects, including multifamily buildings, sooner rather than later.
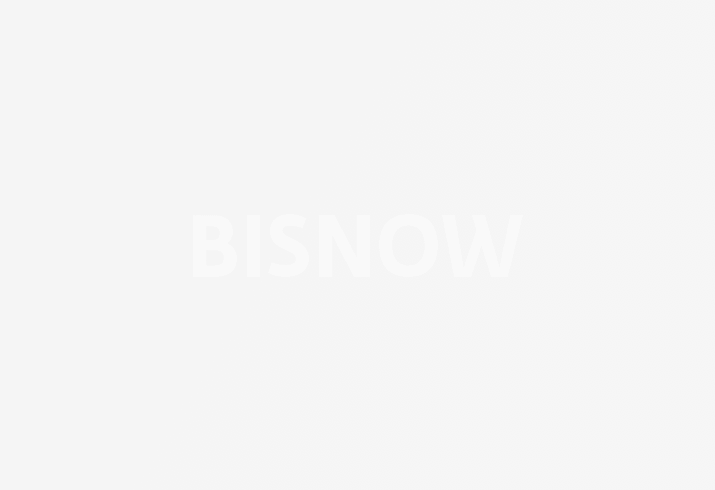
CIVE, a Houston-based design-build firm, is constructing America’s first fully 3D-printed two-story house along with Hannah, a New York-based architecture firm, and Germany’s Peri 3D Construction.
Those involved say the project is a significant stepping stone to constructing bigger projects like apartment developments more quickly and with fewer supply chain-related snags — a major plus for an industry beset with labor and materials shortages.
Construction of the reinforced concrete house began in July and should take 330 hours of printing. The printer can run for 20 hours before going down for four hours of maintenance. That means that, in theory, the project could have been completed in less than three weeks. But CIVE and its partners are taking their time.
“This is like the case study,” CIVE Head of Structural Engineering Hikmat Zerbe said. “A real-life, experimental project. So from this project, we’re learning a lot. That’s why we’re not pushing for speed.”
Instead, project leaders are trying to explore the capabilities of the printers, determine what architectural features can be printed and see how the concrete material reacts in different weather conditions, all while learning as much as possible to use the technology in other applications.
“As a company, this is not where we want to stop,” CIVE President and CEO Hachem Domloj said.
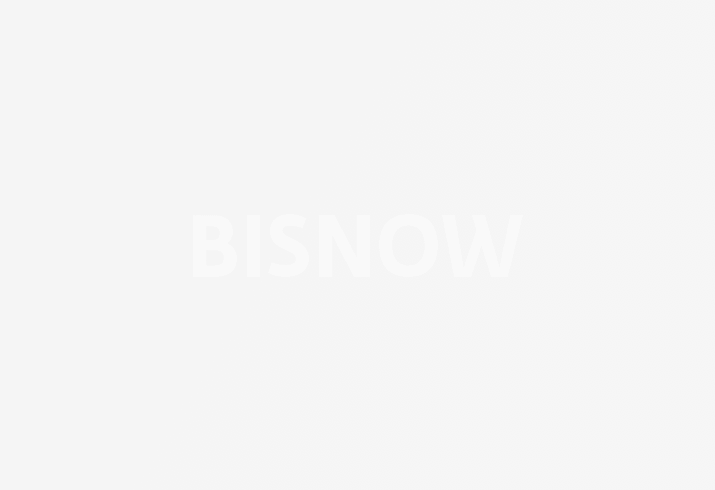
CIVE, which provides engineering, architectural and contracting services, has long been interested in ingenuity in construction, Domloj said, and has researched 3D-printing technology for years. A little more than two years ago, Hannah and Peri approached CIVE to join the two-story house project.
The house will be 100% 3D-printed, save for components like anchors and plumbing. A large on-site printer is capable of pouring entire concrete walls, eliminating the need for some typical framing materials.
It is a young and expensive technology, and the project was only made possible by sponsors donating equipment and material. But Domloj said hybrid construction, which involves 3D-printing some pieces on-site while also using aspects of traditional construction, can be affordably implemented now.
To that end, CIVE is meeting next week with developers looking to assess whether the technology could be used in multifamily home construction, he said.
“Anything that is modular, we are looking to perform with 3D printing,” Domloj said. “[It] minimizes the risk, it’s more efficient, a lot faster and the same cost.”
Domloj said there will be many developments in the 3D-printing industry in the next five years that could make printing larger, taller buildings more achievable. The main limitations are the size of the printers and the capability of reaching higher elevations.
“There are a lot of new startup companies investing a lot of money into 3D-printing technology,” he said. “There are other people developing new kinds of printers that can reach higher elevations more accurately and faster. This is an evolving technology right now.”
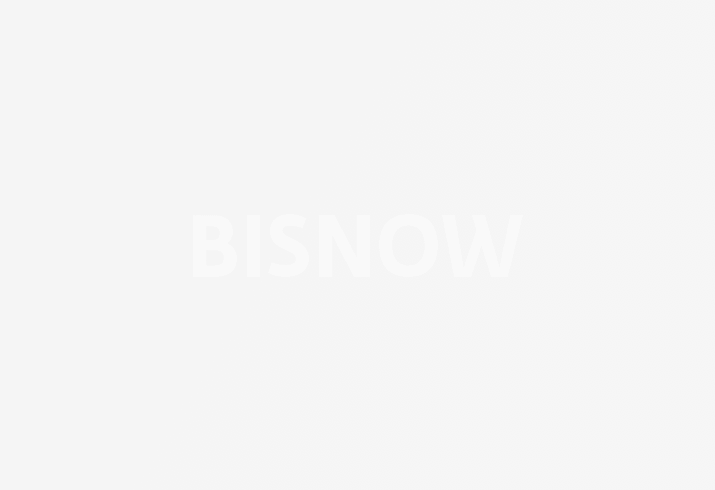
That technology could offer a solution to the affordable housing crisis. Virginia Housing, a nonprofit housing finance agency, used a grant to purchase a 3D printer last year and used it to print a home in Richmond.
"The hope is that 3D-printed houses will be able to be constructed at a lower cost because they require fewer on-site resources and less time to build,” Virginia Housing Director of Strategic Housing Chris Thompson told Bisnow.
3D printing also requires significantly less labor. The Houston project involves a printer operator, a mix operator and a person or two looking at the printer’s nozzle at the two-story house project, Zerbe said, far fewer workers than on a typical construction site.
The project also employs workers to place reinforcements, which are typically metal frames within concrete and can't be printed, he said.
“By applying reinforcement within the structure, we’re able to confidently go two stories,” he said. “If you want to go bigger, higher, you need the reinforcement.”
Domloj said he is excited about the technology but is most enthused about its commercial potential. Interest is high, and applications for housing and other construction are broad and mostly untapped.
Anyone interested in buying the nation's first fully 3D-printed two-story house is already too late. It was sold before construction began, though CIVE is confident there will be more available soon.
“To me, this is not just one project,” Domloj said. “We are looking into how to implement this 3D printing … not to be the only way of construction but utilize it more in hybrid construction. I look at it from a business perspective: the new technology, the new way of doing construction.”