'Everybody Wants A Piece Of The Pie' As Industrial Demand Soars, But Will Rising Costs Cut The Boom Short?
The 2020 shutdowns sparked a logistics and warehouse boom throughout the U.S., but a big question now hangs over the sector: Now that Covid is receding, will the boom last? Experts say they feel optimistic that the pandemic permanently altered consumer behavior and that new methods of shopping, adopted out of necessity last year, will sustain long-term demand for modern warehouses.
“A slightly older generation that would have gone to the store previously has now learned to use Amazon,” Realterm Vice President Derek Fish said last week during Bisnow’s Chicagoland Industrial Boom Digital Summit.
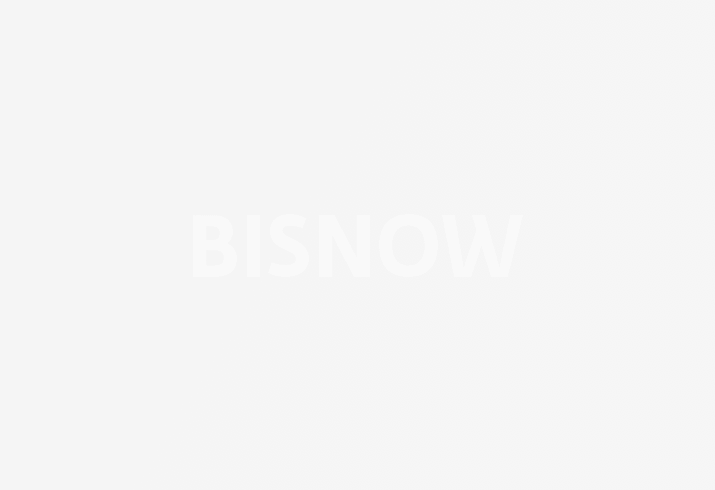
Those new habits have fueled a demand surge, he added. And the recent Suez crisis taught users another valuable lesson that has further boosted demand for Class-A logistics space.
“If you don’t have redundancy, speed and efficiency in your supply chain, you could quickly become destabilized,” he said.
The Annapolis, Maryland-based Realterm will invest between $1.5B and $2B into the logistics sector this year, according to Fish. And clients’ demand for greater speed and certainty has changed how they approach development.
“Their questions are no longer about rent or [tenant improvements],” he said. “It’s about when can you deliver the space, and will it be functional enough to handle all the traffic we now have?”
Alexis Graziosetta-Tobias, director of project development for Premier Design + Build Group, is seeing the same thing.
“Our clients are saying, ‘How fast can you start construction?’” she said.
As a result, Chicagoland development keeps accelerating. Demand for new spec development is exceeding supply, according to Colliers International, which said in its Q1 report that the 86.1M SF of spec product delivered in the metro since 2013 is 81% leased.
The rise in online shopping and at-home deliveries also led users to demand more big-box buildings, a sector that had seen a decline in leasing activity before the coronavirus hit. Nearly 8M SF of new big-box product was finished in Q1 throughout Chicago and its suburbs, Colliers found, including four buildings of more than 1M SF: three build-to-suits and a 1.1M SF speculative facility from CenterPoint Properties at the Intermodal Center Joliet, which Walmart agreed to occupy.
“It seems like everyone is building warehouses on every piece of land they can find,” Graziosetta-Tobias said. “The demand is there and everyone wants a piece of the pie.”
That escalating demand is happening all over the region, according to Kyle Grant, vice president of Venture One Real Estate. It touches every submarket, as well as all building classes.
“Even Class-B and Class-C product is starting to be competitively priced,” Fish said.
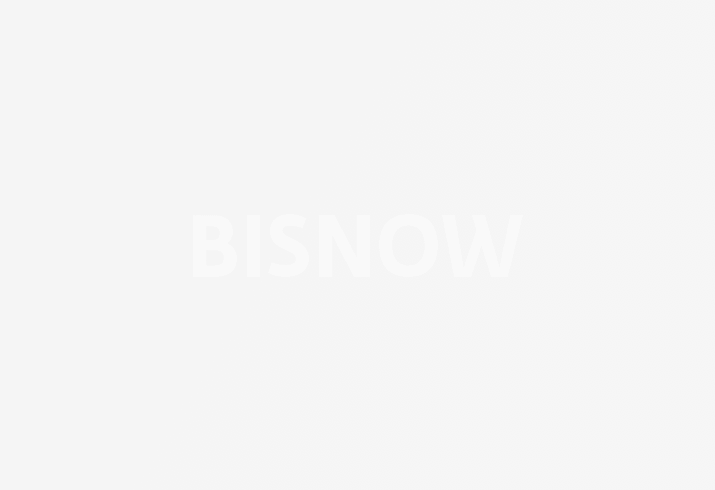
The intense competition in today’s market should bring some subtle changes to how developers service clients, Grant said. As users now need ready-to-go spaces faster than ever, completing simple tasks, such as making sure warehouse and logistics spaces have adequate office spaces, are more important than they have ever been.
“Being in a position to cater to a client who needs a quick occupancy gives you a unique advantage against your competition,” he said.
But all these busy users and developers have a problem, Graziosetta-Tobias said. The massive demand, coupled with disruptions in supply chains, has led to huge increases in the costs of construction materials and delays in construction material deliveries.
Securing an adequate supply of steel joist can now take up to 45 weeks, she added.
“It’s June 2021, and I’m bidding on a project, and I can’t get bar joist until April 2022,” she said. “That’s awful for everyone. And it’s across the board, it’s not just steel.”
Moderator Hugh Williams, principal at MK Assets, asked the group whether builders are seeking new construction methods that will speed up development in the face of supply chain disruptions. Graziosetta-Tobias said there are signs of that happening.
“Just the other day I had a steel supplier give me a different way that engineers are designing bar joist. They are using prefabricated trusses rather than bar joist.”
Whether the boom has staying power may depend on how users react to these price increases and delays, according to Grant. The price of steel has more than tripled in the past year, and at some point, rental rates will have to reflect that, possibly curtailing users’ eagerness for more expansion.
“I would imagine that would limit new supply coming out of the ground,” he said. “Are they willing to pay these premiums for what it costs now for a developer to justify building a new building? Or will they look for a second-generation space or a building that’s already up?”
Graziosetta-Tobias said relief may be on the way. She recently spoke with several steel suppliers who told her price increases will start to let up late in Q4 2021 or just after the first of the year.
But until then, users will have to balance their need to rebuild supply chains with the exorbitant costs of doing so.
“I’m curious to see how the next 12 months plays out,” Grant said.
CORRECTION, July 1, 7:45 A.M. CST: A previous version of the story misstated the time period when steel prices are expected to decline. The story has been updated.