Developers, Contractors Investing In Off-Site Construction Storage To Get Ahead Of Supply Chain Issues
Supply chain delays rooted in the ongoing pandemic have forced developers to rethink construction timelines, strategies and budgets.
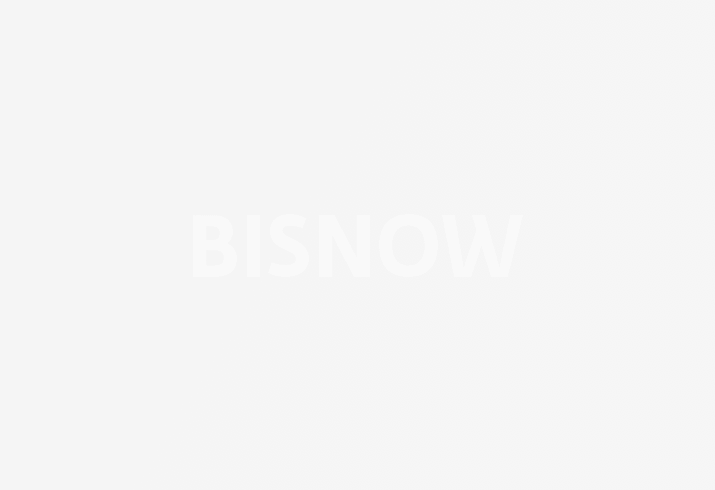
Supply chain was always a consideration when it came to the planning on a major construction timeline even before the coronavirus pandemic kicked off a two-years-and-counting crisis, a panel of construction experts said at Bisnow’s New York Construction and Development event last week. But with uncertainty around the delivery of materials, developers are switching more to proactive approaches like ordering materials ahead of time and utilizing off-site storage.
“Leading into 2018, it was just-in-time delivery. It was, ‘How can we be as efficient as possible so nobody’s wasting time moving material, nobody’s spending money when they don’t need to?’ That conversation has flipped,” said Charles Esteves, director for pre-construction at Schimenti Construction Co. “The off-site storage thing has become huge.”
Esteves said utilizing off-site storage allows developers to account for supply chain volatility, as well as the impact that unpredictable delays can have on a project’s price tag.
“It’s all about schedule. Recent trends are creating delays in the supply chain,” said Thomas Campbell, founder and principal of developer Thorobird Cos. “The most important thing I could say on how to deal with supply side shocks is it’s very difficult to change things once the train gets started.”
Thorobird is partway through building 1921 Atlantic, a project in Bedford-Stuyvesant that combines affordable, middle-income and senior housing. Supply chain delays meant a good relationship with contractors was fundamental to Thorobird’s construction timeline, Campbell said.
Longer delays while builders wait for material to come through make projects more expensive. Unexpected delays to construction and increasing costs can result in shocks that are as uncomfortable for lenders to absorb as they are for developers figuring out how to pivot.
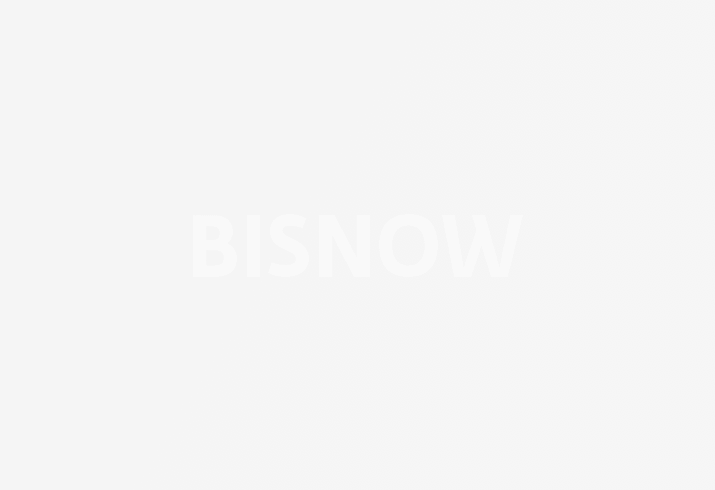
Scott Solish, executive vice president at Greenland USA, said the coronavirus pandemic had impacted 800K SF of construction on Pacific Park in Brooklyn that the developer started working on in 2018 and was ready to start building just before the pandemic hit. But shutdowns and the immediate impact on the supply chain had immediate consequences.
“You have to regroup, look and see where all your components are coming from, where are your windows coming from, your HVAC, every piece of material,” Solish said. “Then you have to try and find out: is it coming; how fast can it get here; will the bank let you pay for it upfront; can it get through the port; where are you going to put it.”
The comprehensive approach has been critical as the availability of every type of material has waxed and waned over the course of the past four years, creating a need to keep even finishes on hand well before the project is close to completion.
“There’s no consistency. Something comes up on each project, and it’s something different on each project,” Esteves said. “The off-site storage thing has become huge — that’s where we’re trying to take risks.”
Greenland — which hadn’t factored a supply chain crisis into its construction planning — was left competing for storage space once its materials arrived. But developers like Thorobird started adding off-site storage into their construction process and budget even before the pandemic. The key to being able to take a proactive approach, Campbell said, is having contractors you trust.
“We really went out and we allowed our contractor to invest in storage, to go out and purchase the things that we knew were gonna be long lead time items,” Campbell said.
For one project, Thorobird purchased exterior brick six months before the job would require it, and put it in storage until then.
The forward-thinking approach hasn’t shielded the developer from all delays: It’s currently waiting on paint to come through, but Campbell said a six-week lead time is a manageable obstacle. The flip side is that lenders are open to financing storage if developers can make a good argument for it, said Kenneth Wille, the president and CEO of KOW Building Consultants.
“Banks don’t like surprises. They don’t like volatility. They don't mind risk, as long as they assess that risk properly,” Wille said. “Banks are willing to take the risk on things like a deposit or an off-site store of material if it means you get to lock in pricing.”