Red-Hot Lab Market Getting Cooled Down By Supply Chain Delays, Chip Shortages
The incredible surge in demand for life sciences real estate has recently been exacerbated by the supply chain challenges roiling so many industries, creating logistics anxieties and delaying long-anticipated completions of new lab space.
Developers, analysts and construction executives said these issues, complicated by the myriad items and materials that have been delayed in recent months, won’t go away anytime soon.
“It used to be, you’d gauge when you could start a project by when the drawings were done,” Dacon Director of Architectural Operations Jennifer Luoni said. “Now, it’s how fast you can order the equipment so it arrives in the next six months.”
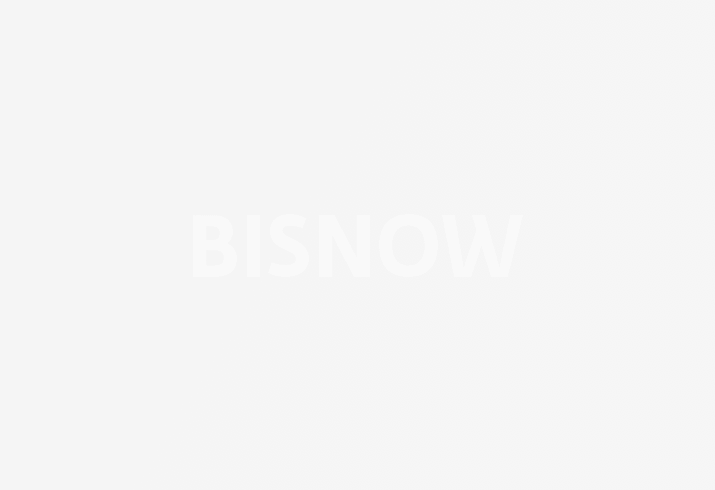
Boston Properties Vice President Jon Lange said the lead time for major pieces of equipment has increased anywhere from 25% to up to 100% or more compared to pre-pandemic, significantly impacting the REIT's redevelopment projects.
“If you typically assume one year for an office-to-lab conversion, with current lead times, this year is getting extended, which will push out base building and tenant occupancies,” Lange said. “This exacerbates the shortage of high-quality, finished lab space in Boston, the Bay Area and other major life science hubs throughout the country.”
Surging demand nationwide has created a shortage of available lab space. Demand grew 34% year-over-year across all markets, a July CBRE report noted, construction firms in the space face record demand, and venture capital investment in life sciences, another measure of demand, is set to shatter records this year.
In response to these backlogs, developers have been more careful and fluid when building, as constantly fluctuating supplies of furniture and machines mean the dimensions of the labs and electrical wiring setups may rapidly change with new replacement parts.
One of the big struggles during pandemic-era construction has been how the items in demand or on backorder keep shifting. Luoni discovered in August that the lab furniture needed for a new project was on a 38-week delay, when she had previously been told eight to 10 weeks; her team ended up custom-building benches at a 30% premium.
Other firms told Bisnow they found orders for steel studs for walls were delayed 14 weeks. Lab Launch CEO Llewellyn Cox, who has helped develop a pair of incubator spaces in LA, said his biggest day-to-day challenge is lab plastic, specifically the single-use tubes, pipette tips and culture plates needed for daily experiments.
A large-scale retrofit of a Quest Diagnostics manufacturing facility in the Boston area was delayed four months due to trouble sourcing electrical switching gear, said Timberline Construction CEO Steven Kelly, who also noted that a single missing motherboard for a rooftop HVAC unit was holding up another lab project.
Developers of larger projects are leaning on preferred supplier relationships, which provide them with preferential treatment and access to in-demand items, putting more pressure on smaller lab developments.
The reality of these delays is putting some jobs on the backburner until supplies are confirmed — there is no use finishing a lab space so a tenant can sit for months without equipment and rack up rent payments without being able to do any work, Luoni said.
Much of this challenge comes from container ship delays at major ports and the larger supply chain crunch. Chinese companies manufacture much of the furniture, materials and machines needed in labs, and lines of container ships off West Coast ports have pushed back delivery dates for many items. Kelly said the time it takes for a ship to traverse the Pacific has gone from 30 days to nearly 80.
But the ports aren't the only source of friction. Canadian manufactures, which produce a good number of U.S. lab benches, insulation, rubber flooring, firestopping and lab casework, often have trouble trucking in goods due to labor and logistics issues arising from Canada’s longer lockdown, Perkins&Will Science and Technology principal Matt Malone said.
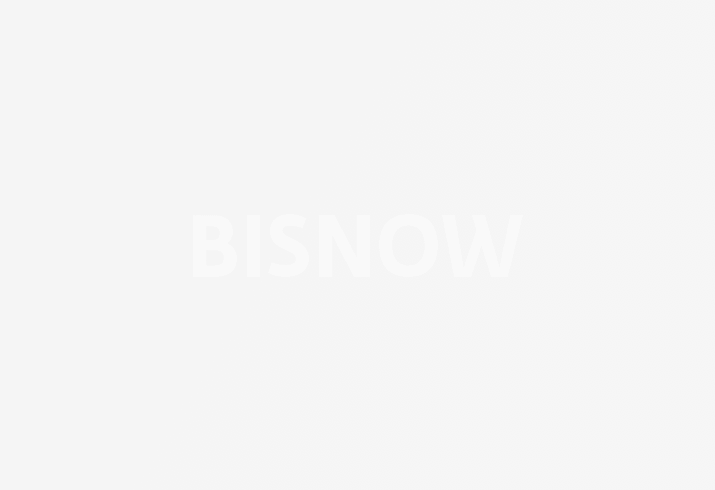
But for many, the real challenge comes down to microchips. Labs, especially for newer startups focused on cutting-edge cell and gene therapy, require significant numbers of high-tech machines to operate, in addition to the sophisticated HVAC systems and temperature controls required for all lab space.
Like automobiles, the nation’s lab spaces have become significantly more digital in the past few decades, making the microchip shortage especially painful. Malone said he is seeing shortages of variable frequency drives and fire and smoke damper actuators, as well as aluminum parts.
Luoni has seen firms attempt to buy used equipment online, she said, so they can start researching instead of waiting for new gear to arrive.
Even lab renovations experience significant delays. Outside Philadelphia, the $1.1B, 680K SF Centers for Breakthrough Medicine, a lab space and biomanufacturing site, was built on the site of a previous research center. Even with many of the necessary generators and air handling equipment in place, co-founder Audrey Greenberg said it has still been challenging to find casework and advanced machinery, such as bioreactors.
In response to these challenges, construction and development firms are ordering materials and machines well in advance, planning extremely far ahead to avoid delays. The rush to order and lock in pricing and materials is real — suppliers are guaranteeing pricing for days, instead of weeks, and developers and construction firms are more apt to cite contractual clauses about potential price increases due to supply issues.
It’s creating a lot more tension, Luoni said, since project teams, now accustomed to sudden delays, are “waiting for the other shoe to drop at all times.”
Like so many industries caught in the grip of a supply crisis, the answer isn’t simple. Without the right parts and materials, companies can’t simply add additional manufacturing facilities to increase supplies.
Kelly said he expects steel production to be back to normal shortly, and many of the supply chain issues, at least for Boston, could rectify themselves by the middle of next year.
But there may be something of a silver lining in the uncertainty. Luoni said the challenges faced today have made design-build — a method of project delivery where all architects, contractors and subcontractors work as a unified group, ideally eliminating delays and inefficiencies — more popular among firms working in the industry. That could mean faster projects once supply chain issues are resolved.
CORRECTION, NOV. 10, 11:15 A.M. ET: A previous version of this story misidentified the company Quest Diagnostics as Qwest Diagnostics.