Frenzied Pace Of Lab Construction Has No End In Sight
Much like developers rushing to find new space for labs, the firms specializing in the construction of life sciences lab and manufacturing space are a small, specialized group that has seen its workload and revenues skyrocket over the past year.
“Is this pace sustainable? I don’t know the answer to that,” Suffolk Construction Vice President of Life Sciences William Sayles said. “I’ve been at this for 25 years, and never seen it as heavy as it is now.”
Sayles says his firm’s life sciences workload has doubled since 2019, and he expects to be extremely busy for at least three to five more years. Sayles and executives from four other major firms with life sciences construction specialization said in interviews with Bisnow that today’s extremely fast pace is new, not set to slow down anytime soon, and won’t even solve the lab space supply crunch.
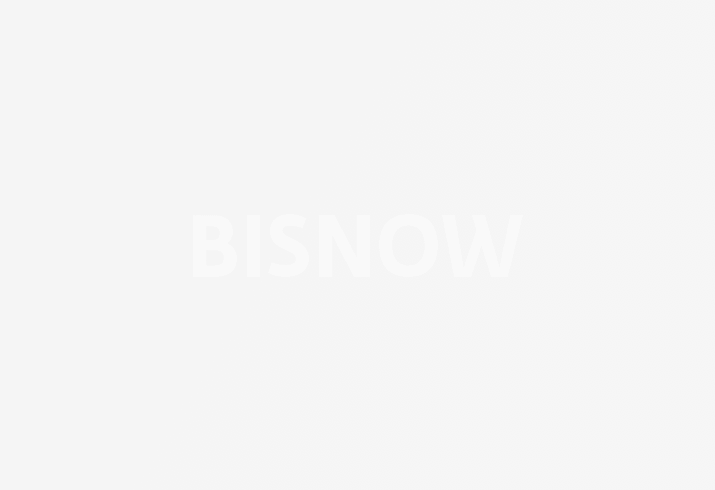
Leaders of these firms are seeing record or near-record demand for lab, and especially manufacturing space, which has benefited from the Covid-19 vaccine push, a national reshoring effort, and new demand driven by advances in cell and gene therapy.
Seattle-based BNBuilders has seen its manufacturing workload double in the past year. DPR Construction Life Sciences Core Market Leader Scott Strom said four years ago, the firm, which has contracts nationwide, was doing just under $900M in annual biotech business. This year, it should top $2.3B.
Universities have also pushed to build more applied science and research space, said Kitchell Regional Executive Brian Brown, a response to how the pandemic led to decreased enrollment, retention and revenue in academia.
“To sustain themselves and adapt to a changing education landscape, there’s more investment in research,” he said, adding that investment eventually will lead to innovations, spinoffs and more demand for lab/pharma-type space at a commercial level.
There doesn’t seem to be a rush of new construction firms entering the space. The complexities of these projects, as well as long-standing relationships these contractors have with big developers, have made it extremely difficult for new firms to enter the industry, experts said, so buildings tend to be built by the same players, especially in markets like the Bay Area, competing against each other for jobs.
“Owners and clients with knowledge in the industry are doing background checks on the skill sets new firms claim to have, since it’s better to pay now than pay later,” Sayles said. “There’s definitely a barrier to entry here.”
Like the rest of the construction industry, life sciences work has been stymied by supply chain issues and raw materials shortages, such as cold-rolled steel. But the specialized nature of life sciences work has added additional complexities to getting the right material to the job site.
High-purity piping requires special workers to install. Automation gear, such as valves and actuators, and process equipment are in short supply or stuck in shipping limbo. HEPA filters, which are made of the same material as disposable face masks, can be hard to get. A type of epoxy resin used for workstations in labs became hard to get earlier this year when power outages in Texas shut down a plant that specialized in the chemical.
“The supply chain is resistant to wanting to tie into numbers too early because everything in their supply chain is fluid,” XL Senior Vice President of Integrated Solutions Chris Bailey said. “Then it gets into how do we forecast not just design contingency or construction contingency, but escalation? We went through 14% escalation in Northern California in the first eight months of the year. Nobody saw that coming, and it’s a difficult conversation with clients.”
In addition, the labor needed to handle specialized parts, materials and procedures is in short supply. DPR’s Strom said the shortage is amplified in the markets like San Francisco, San Diego and Boston by what he called megaprojects, which cost over $350M, tend to pay over scale and create more competition for trade specialists.
For many firms, however, overall labor shortages haven't been among their tougher challenges — although Bailey said vaccine mandates for workers tended to be much stricter for firms working on lab and pharma projects. Sayles said since Suffolk has seen its work in other sectors, particularly office, slow down, the multidisciplinary firm has been able to shift some workers into lab projects.
“Everything and everyone is feeling flexed,” XL Construction Project Executive Tate Chandler said. “If you’re gutting an office and turning it into a lab space, that’s something that takes more horsepower every step of the way, and it's tough for city building departments to adjust to that.”
These shortfalls and temporary stoppages add time and cost to lab projects. Strom said products are running about a month late, nothing “catastrophic.”
But the challenge juggling contractors and supply chain hiccups means ordering materials well ahead of time and procuring specialized staff early is key. Some techniques have become more widespread, such as design-build construction, or using prefabricated cleanrooms to speed up the construction process. But there’s no silver bullet for radically accelerating a complex construction project.
“We are in a different market right now,” Strom said. “It’s going to evolve and add considerations for how we build.”
CORRECTION, OCT. 8, 7:00 P.M. ET: A previous version of this story misidentified clients of DPR Construction and misconstrued a statement by a DPR representative about delays in sourcing products. The story has been updated.