How Can Construction Teams Work With Suppliers To Get Back On Track?
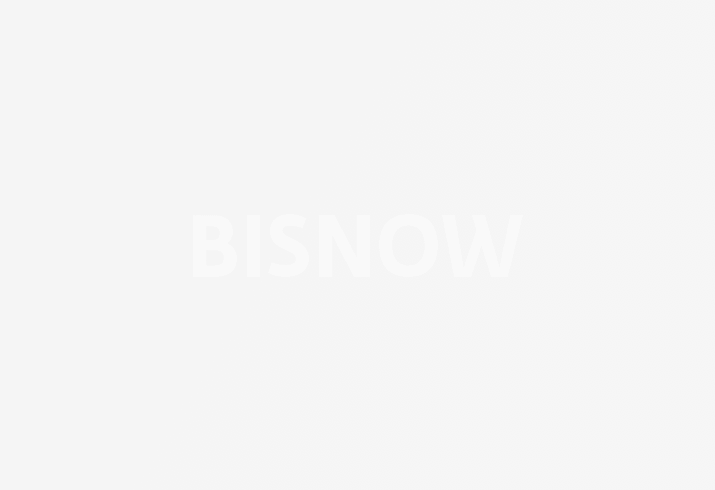
While the construction industry has been steadily recovering from the pandemic, major project delays remain. In a January 2022 survey by the Associated General Contractors of America, 72% of contractors said that their projects have incurred delays throughout the pandemic.
For general contractors and subcontractors, one solution to stay on track is to work with suppliers that have internal processes to ensure materials will be available on-site when needed and without missteps.
Bisnow sat down with Tim Yeiser, president of Dricrete, a company that provides technology for concrete waterproofing, to discuss how construction crews can work with suppliers to ensure maximum efficiency and prevent project delays.
Bisnow: How has the industry, and suppliers in particular, been impacted by pandemic-related construction delays?
Yeiser: This industry has always had issues with delays and the pandemic has created an entirely new set of problems; spiraling fuel costs, freight, material and labor are out of our control. We have heard horror stories about companies waiting for containers sitting offshore, so we need to be even more vigilant in taking control where we can.
Unlike other suppliers, Dricrete is not dependent on overseas deliveries. Our raw materials are sourced locally and manufactured domestically. Fortunately, because of this, our inventory has remained solid throughout the pandemic.
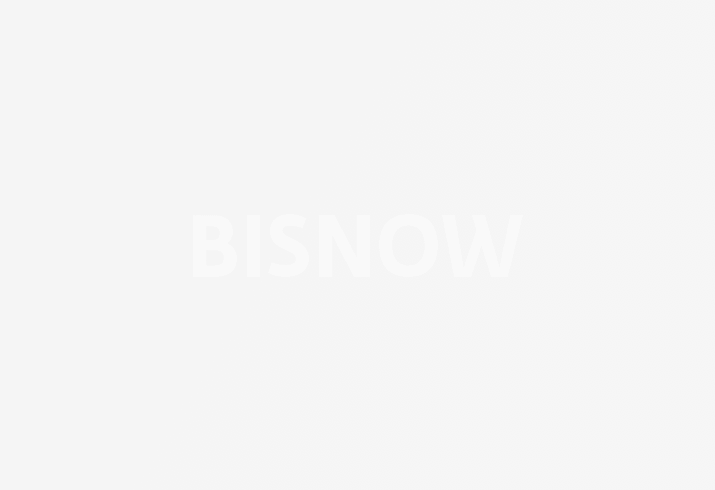
Bisnow: If failures occur and a key project material is not implemented in a timely manner, how can that impact projects?
Yeiser: With any delay there is an "accordion effect" that ripples through the trades, much like planes stacked on a runway losing more and more time as the day wears on. With so many moving parts, it can take as long as a month to get everyone back in sync.
This crisis has forced builders to think outside of the box, which has been a driving force in the success and acceptance of modular housing, for instance.
Bisnow: How has Dricrete provided solutions for project delays?
Yeiser: The Dricrete business model took the below-grade waterproofing trade off-site 20 years ago to help maximize time and project efficiency. We bundled technology and chemistry in the concrete and assumed the responsibility for the cold joint design, delivering a fully enveloped basement to the developer.
We are self-contained and don’t require logistics, labor, machinery, scaffolds, man-lifts or crane time. Our waterproofing is integral with the concrete and piggybacks with the arrival of the ready-mix truck, thus eliminating the time traditional below-grade waterproofing methods consume.
Typically, using this process we shave at least two-three weeks off the construction schedule.
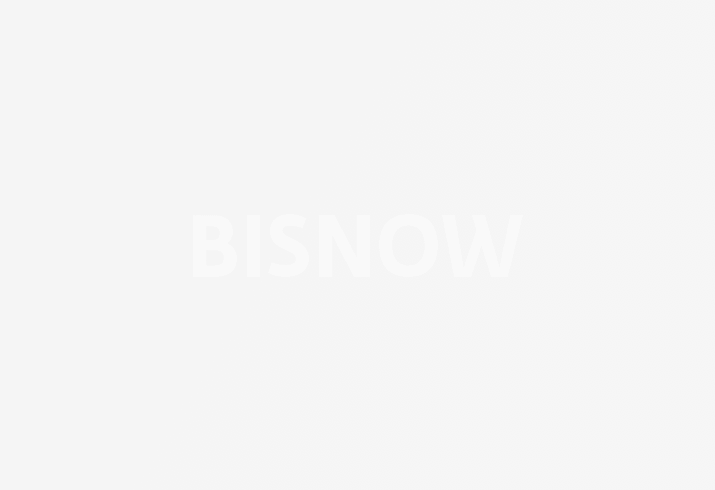
Bisnow: Can you give me an example of how Dricrete’s business model has benefited your clients?
Yeiser: We have worked with owner-developer IMT Residential for the past 12 years and we are currently underway in Sherman Oaks, California, at the Citrus Commons. Right from the start, IMT recognized our value engineering solution and drove the bus during the first pre-construction meetings. They directed the concrete subs to work with us, knowing that the waterproofing phase would move smoothly and quickly creating a great start from the outset.
Our goal is to save time and money for our clients. If we can help them deliver a project a month early on a 500-key apartment with average rent of $4K per unit, the result is $2M in the bank earlier than expected. This is particularly helpful for the opportunity zone builders who are required to finish at 18 months.
We have never delayed a project, not even by a single minute. Staying on time and on budget has become even more elusive and we are extremely happy to be part of the solution.
This article was produced in collaboration between Dricrete and Studio B. Bisnow news staff was not involved in the production of this content.
Studio B is Bisnow’s in-house content and design studio. To learn more about how Studio B can help your team, reach out to studio@bisnow.com.