2 Companies Building Modular Housing Factories In Colorado
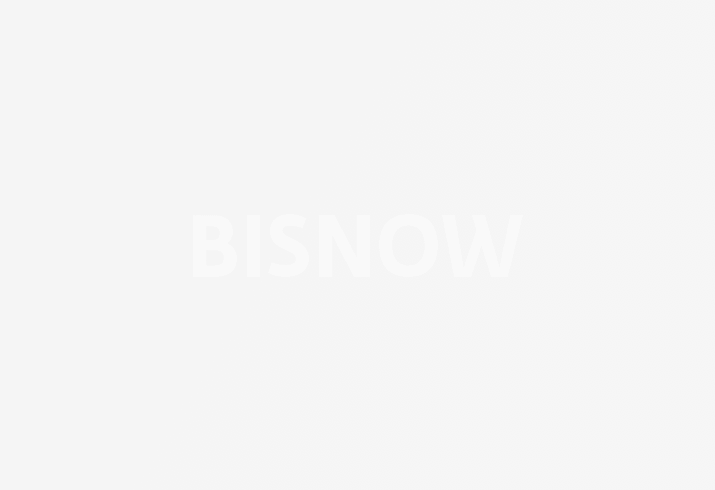
Two leading manufacturers of modular housing, Idaho-based Guerdon Modular Builders and Vederra Modular, headquartered in Aurora, Colorado, are preparing to open new facilities in Colorado.
Both companies received loans from the state as part of a push to create more affordable homes. Guerdon was awarded $8.5M and Vederra received $6M from various state agencies, the Denver Business Journal reported earlier this year.
In an announcement in March, Guerdon CEO Tommy Rakes said his company, which has yet to select its site for a 200K SF factory, expects to hire more than 200 people once it opens.
“The new facility will serve as a satellite factory, leveraging local talent while benefiting from centralized administration in Boise, which will remain the company’s headquarters for core operations,” Rakes said in the announcement.
Nathan Peterson, Vederra’s founder and CEO, said his company is working on finalizing a lease for its planned 140K SF factory in Adams County. Once up and running, which is expected by the end of the year, he anticipates hiring about 150 workers for the factory’s assembly line, as well as 20 office employees.
Peterson said Colorado is playing catch-up with the rest of the country in modular housing. The state used to have five modular housing factories, but they closed during the Global Financial Crisis, he told Bisnow.
Peterson said the Centennial State’s modular housing market share is about 1.8%, while that figure is around 3% to 4% nationwide.
“The governor has said he’d like modular housing in Colorado to get to a 5% market share,” Peterson said. “He’s really behind reestablishing the industry. “
Vederra’s modular housing is made up of “boxes” measuring 72 feet by 18 feet at the largest. The boxes come with kitchens and baths, but otherwise they allow “complete design flexibility” by the user. While one box can be used for a studio residence, Peterson said they can also “be put together like a bunch of Legos,” to make larger residences and buildings, which can improve construction efficiency.
“Modular housing, if done the right way, can be between 10% and 20% lower costs than traditional construction,” he said.
A typical modular project usually takes six to nine months to complete, according to Peterson.
Vederra’s Colorado facility is projected to construct more than 200 modular housing units in 2025 and expected to make upward of 500 “boxes” annually at full production levels.