New Precast Standards Bring Goals Of Project Owners And Architects Into Alignment
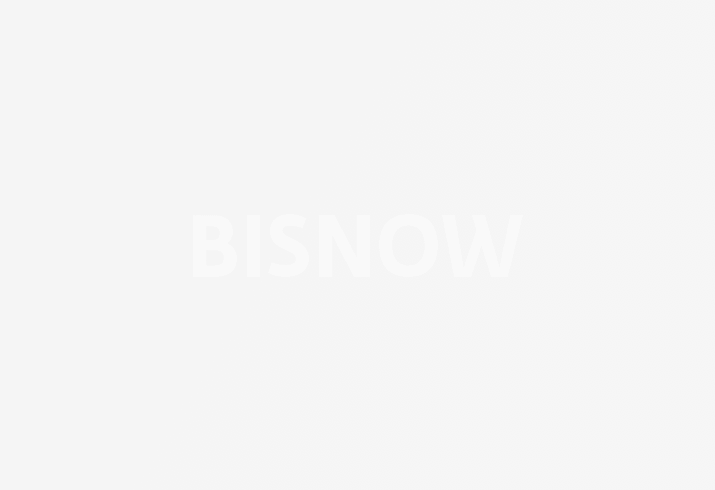
A new certification program helps project owners, architects and designers select the right architectural precast concrete producers for their jobs, allowing projects to be completed faster and more cost-effectively without sacrificing design quality.
But to get the most out of the new program, architects and owners need to understand some of the nuances that separate the four tiers of architectural precast certification.
When it introduced the standards in Q4 2021, the Precast/Prestressed Concrete Institute said the previous one-size-fits-all certification program it had used for more than 50 years no longer met the needs of the architectural, engineering and construction community.
“Designers asked PCI to consider developing a new program that would highlight the quality skills available from the industry,” PCI President and CEO Bob Risser said when the new standards were unveiled. “The PCI board accepted the challenge and after several years of hard work by PCI members and staff, the program is underway.”
What does this mean for the architects, builders and owners of new commercial buildings? Representatives of High Concrete Group, one of the country’s largest precasters, said PCI’s new four-tiered system better aligns the expectations of project stakeholders.
“While it is easy to see why architects and end users gravitate toward the very ornate and intricate aesthetics that precast concrete certainly offers, these designs may conflict with some of the client’s priorities," High Concrete President John J. Seroky said. "That is why it is important to work with a precaster that has an in-house design and engineering team to help ensure the right balance of aesthetics and function.”
But in the context of PCI’s new standards, this does not mean that architects and end users need to sacrifice quality, said Jamie Sweigart, director of sales for High Concrete.
“Today’s precast product options are not the precast concrete of years ago,” Sweigart said. “They are not limited to institutional-looking walls. There are so many features that can be added to any precast product and the new standards allow the manufacturer to produce very economical and yet very aesthetically pleasing products.”
PCI’s new system separates architectural precast products into four categories. The most stringent, known as “AA,” has the tightest product and installation requirements, and covers cladding or non-load-bearing products that feature three-dimensional or curved surfaces.
Two other categories, AB and AC, also cover cladding or non-load-bearing precast products but with less-demanding tolerances, which establish permissible variations in product dimension and location. The least architecturally exacting category, AD, concerns structural precast products.
Architects might be tempted to specify AA-level precast products for architectural applications, but most times their customers’ needs can be met with the slightly less stringent — and more budget-friendly — AB or AC standards, Sweigart said.
“The high tolerances of AA are achievable, but what architects need to know is that there are costs associated with AA,” Sweigart said. “In all the jobs we look at throughout a year’s time, you might get one project that's truly right for AA, but there's a lot of additional setup time, forming time and pouring time involved. Because the tolerances are so tight, we have to really make sure that our forms are absolutely perfect. And then once the piece is pulled out of the forms, then it's making sure the color and the finish are absolutely premium.”
Fewer than 20% of precasters are certified capable of doing AA-level work, a designation that is not easily achieved. To join that exclusive club, Sweigart said High Concrete participated in extensive and ongoing auditing and monitoring by PCI at its two plants in Ohio and Pennsylvania.
But even with that level of commitment, Sweigart said the company doesn’t hesitate to tell a customer when they might be just as well-served by specifying products that meet the slightly less stringent AB category.
“An AB product itself is really a very high-end architectural precast product but with less of the costs of an AA product, which is significant at a time when many contractors and owners are concerned about high material and labor costs,” he said. “For most projects, everything that you need or want in a precast wall is covered through AB.”
Whichever level of precast a project owner ultimately chooses, Sweigart said all precast products bring the same benefits to buildings.
“It often gets overlooked by architects and owners, but precast offers a huge reduction in a completed building’s operational costs,” he said. “Precast panels provide edge-to-edge insulation, which is required today by many building codes. The concrete is absorbing heat or cold and releasing throughout the day, which ultimately reduces the demands on the building’s HVAC equipment. Precast also has a very long lifespan, which reduces maintenance or repair needs for owners.”
Any industry-wide change can lead to disruption. But in this case, the shift to using the new certification program should give project owners, architects and designers better clarity and inspiration when selecting and specifying precast concrete for their projects, Sweigart said.
This article was produced in collaboration between Studio B and High Concrete. Bisnow news staff was not involved in the production of this content.
Studio B is Bisnow’s in-house content and design studio. To learn more about how Studio B can help your team, reach out to studio@bisnow.com.