Not Just A Pretty Facade: Porcelain’s Durability Made It Material Of Choice For 2 New D.C. Developments
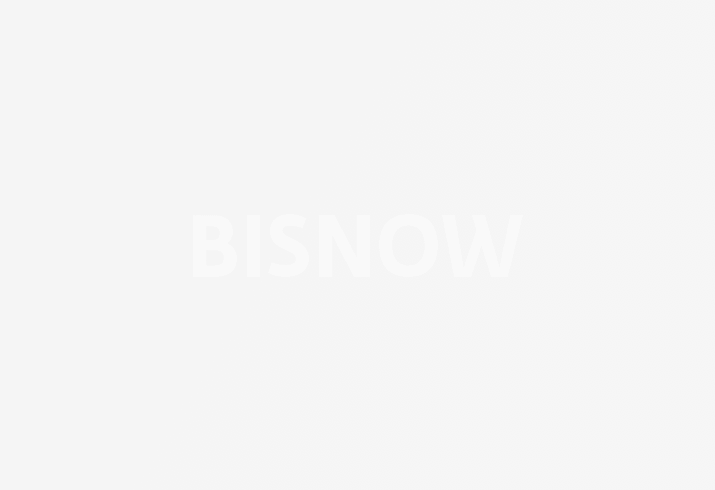
When the architects of two new building complexes in the Washington, D.C., area wanted cladding or interior materials that were durable, easy to work with and attractive, they turned to one often associated with vases and other delicate furnishings.
But far from being fragile, the material they selected — porcelain — is known for its resistance to wear and tear, as well as its ability to meet the design requirements of contemporary architecture.
“To realize The Silva’s complex exterior features, the design team needed a thin material that could stand up to exterior requirements but also handle changes in angle abruptly and elegantly,” said Dean Hutchison, senior architect of CORE architecture + design, which, together with the UK's Grimshaw, designed The Silva, a 10-story, 175K SF multifamily development in Washington, D.C. “Porcelain tile ended up being the ideal material for this.”
Clearly, this is not the porcelain of your grandmother’s Hummel figurines.
“Technical porcelain” is manufactured to stand up to the elements with its thermal expansion and contraction properties, and to resist freeze-thaw cycles and the buildup of efflorescence. Exterior porcelain cladding panels absorb no more than 0.1% of water, meaning they are virtually impervious to moisture.
“Porcelain not only offers the widest aesthetic options, but as a man-made stone product it also provides technical features such as increased durability and impact resistance,” said Santiago Manent Alonso, Mid-Atlantic and Southeast general manager for Porcelanosa USA.
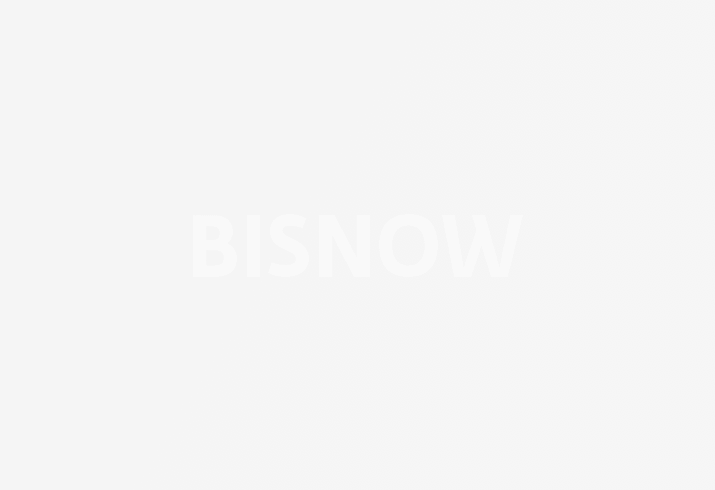
Spain-based Porcelanosa provides a range of porcelain-based tiles and mosaics, custom kitchen cabinetry, flooring, bathroom and sanitaryware, natural stone slabs, installation materials, exterior façades and other surface materials. It operates 30 showrooms in the United States and Canada, where architects, builders and owners can become acquainted with the properties and benefits of porcelain.
Manent Alonso said lightweight porcelain requires no maintenance thanks to its anti-graffiti and frost-proof properties, and it is noncombustible and highly resistant to wind loads. Along with the material’s aesthetic appeal, it was those qualities that convinced architecture and design firm CORE to specify porcelain materials for both the exterior and interior of The Silva.
The exterior porcelain panels needed to accommodate The Silva’s unique design, which gives each of its 172 units a corner view with oriel bay projections. The façade also needed to complement The Silva’s neighbor, a limestone-clad historic building.
“The lighter weight of the porcelain tile, compared to precast or terra cotta, lent itself well to a stunning aesthetic that required less support structure — and therefore a lower cost — than other materials with a similar aesthetic,” Hutchison said.
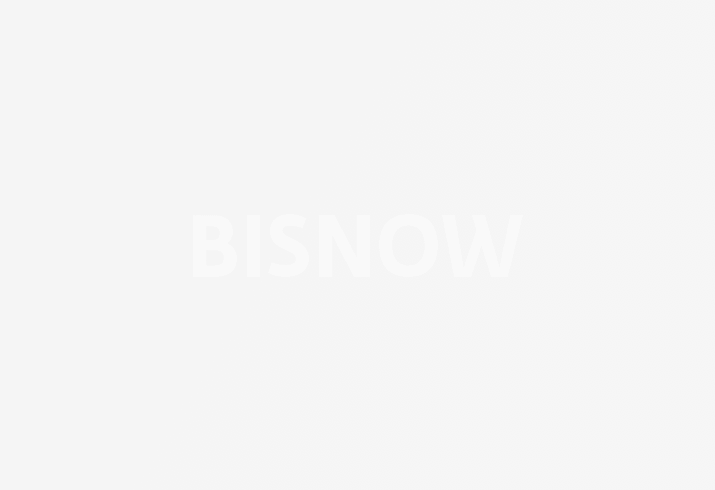
A few miles away, in Bethesda, Maryland, porcelain materials were selected for the flooring, bathroom and kitchen tiles and other interior elements of The Wilson and The Elm. Manent Alonso said the award-winning three-tower, 940K SF multi-use development includes the tallest building in Montgomery County.
Porcelanosa provided many aesthetic options while clarifying any issues that could have impacted schedule and delivery times, noted the design team at Shalom Baranes Associates, architect of The Wilson and The Elm. This helped the design team feel confident it was selecting the right materials that would not need to be substituted late in the game.
Manent Alonso said Porcelanosa established a direct line of communication between itself and the specifier, which allowed it to meet budget, style and lead-time priorities. The company's multi-unit program offers a one-stop solution for clients, he added.
The key to successfully incorporating porcelain into their buildings’ designs, both architecture teams agreed, was working with the manufacturer and its in-house team of architects and consultants from the beginning of the projects.
“As early as the concept stage, CORE worked extensively with the general contractor and Porcelanosa to ensure the joints of this material came together with the intended visual alignments as well as appropriate spacing to allow for expansion,” Hutchison said. “We also worked with Porcelanosa to ensure the grain of the pattern would remain vertically oriented throughout the building, even with individual panels that were wider than they were tall.”
Porcelain tiles, backsplashes and other interior elements serve another purpose, too. Their antibacterial and stain-resistant properties make them a natural choice for kitchens and bathrooms in the Covid era, Manent Alonso said.
“Trends in the healthcare industry are being replicated in the multi-unit niche, where everyone is aware of the need for clean surfaces in kitchens, bathrooms and home offices,” he said.
This article was produced in collaboration between Studio B and Porcelanosa USA. Bisnow news staff was not involved in the production of this content.
Studio B is Bisnow’s in-house content and design studio. To learn more about how Studio B can help your team, reach out to studio@bisnow.com.