Mortenson Takes Its First Steps Into Modular Hotel Construction
Hotels, with their small, identical units, are an ideal match for pre-constructed modular units. Each hotel room can be made in a climate-controlled off-site location and then installed like a Lego block into its permanent home. As construction costs for labor and materials continue to soar, modular units are one way contractors are controlling costs and speeding up delivery time.
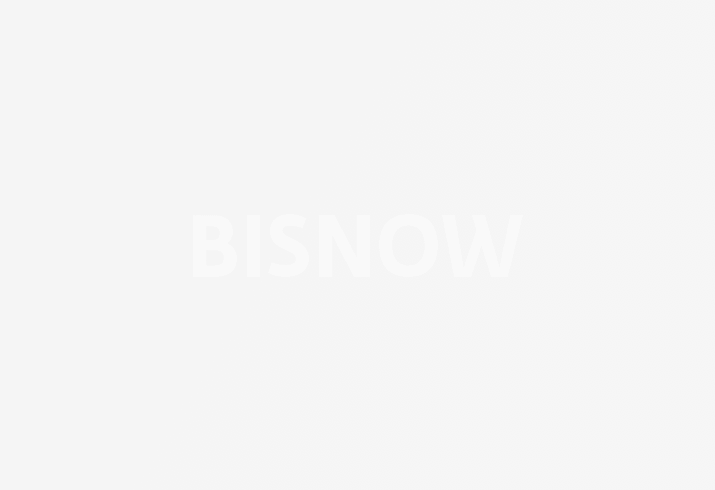
Mortenson Construction recently took that step when it installed modular hotel rooms at the seven-story citizenM hotel, which is currently under construction in South Lake Union. Each modular unit is an individual hotel room that was shipped on one vessel from Europe to the Port of Everett.
There are a total of 264 rooms that are being installed atop a traditionally constructed concrete podium for the hotel. Each unit is fully finished with floor, fixtures, wall coverings, lighting and furniture. The units include everything except the mattress, pillow and towels.
Modular construction is widely used in Europe, Asia, Australia and in some parts of the United States. Even Marriott International is embracing this trend. But building modular hotels is new to Seattle.
“Modular construction allows for large schedule savings on project delivery which equals speed to revenue for our customer, citizenM,” Mortenson General Manager Seattle Operating Group Phillip Greany said in an email. “It’s a 13-month construction schedule versus 17 months for a traditional build — a savings of four months.”
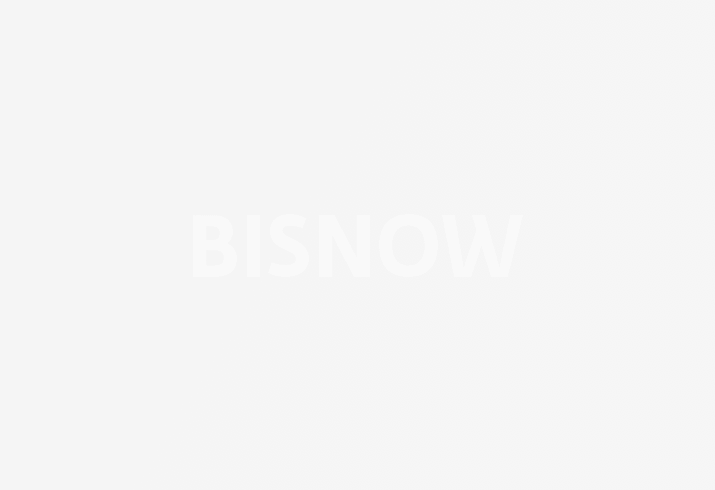
The use of modular units in commercial construction helps mitigate the lack of skilled labor in the Seattle market, which is driving up construction costs during the current building boom, he said.
The technique also allows for a higher level of quality control and safety, due to the fact it is built in a factory. It eliminates the effect of bad weather and the work is performed in an assembly-line fashion where quality standards are easier to duplicate. It reduces construction waste by 60%.
It is also safer, Greany said.
“We are eliminating adverse weather conditions that can contribute to slips, trips and falls,” he said.
The process moves 80% of the hotel construction work off-site, which reduces the impact on the neighborhood. It requires fewer construction workers needing parking, fewer street closures for materials deliveries and fewer noise disturbances.
Mortensen is in early discussions with two other Seattle-area hotel clients that are interested in using modular technology. It will begin another citizenM modular-built hotel in downtown Los Angeles by Q2 2019. The company is also exploring modular construction in the development of student housing.
The citizenM hotel is at 201 Westlake Ave. N. In addition to Mortenson, which is the general contractor, the project team includes architect Gensler, engineering firm Arup and modular builder Polcom Moduling.
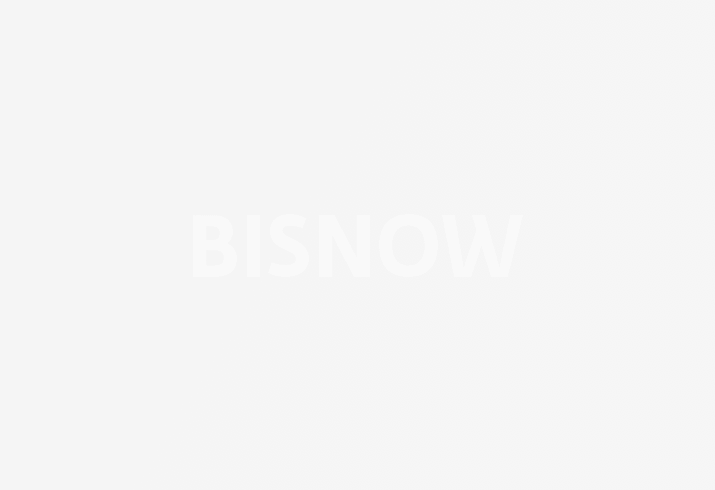
Though this construction trend is new to the Seattle commercial real estate market, the trend has already taken hold elsewhere. The 32-story, 363-unit 461 Dean St. building in New York City is a well-known building constructed with modular units. Built in 2014, this project highlights the potential difficulties that can arise when using modular construction, according to New York Yimby.
Despite potential problems, many in the industry expect to see the modular trend grow in 2019, according to a report by eSub construction software. The trend will likely last because it promises to save time and money, allows for better recycling of unused materials and reduces the effect of weather.
Some companies are even betting investment money on the trend. Japanese conglomerate SoftBank Group Corp.’s Vision Fund is investing $865M in Katerra. Katerra is a Silicon Valley startup that is creating an assembly system to control design and production of modular units.