The Prefab Paradox: Slow Down Now To Save Time Later
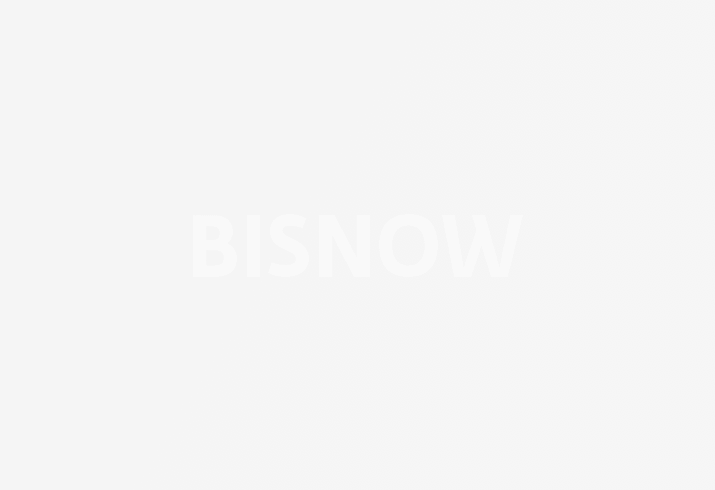
In the resurgence of prefabricated buildings, architects, developers and other project stakeholders have been inundated with the idea that prefab’s main purpose is to save them time and money. Despite these perceived benefits, the commercial real estate industry has yet to fully embrace this construction methodology.
Ryan Ware, president of construction firm VANTIS, has a theory as to why.
“Everyone has bought into the idea that prefab’s singular benefit is the reduction of construction costs and should only be considered if it saves them money at the outset — but that’s a short-sighted view of things,” Ware said. “Prefab’s greatest strength actually lies in its ability to help solve some of the overarching problems we’ve had in the construction industry for quite some time now.”
At VANTIS, Ware and his colleagues believe that to achieve the time and cost-saving advantages of prefabrication, the construction industry must heed the adage of measuring twice and cutting once. Developers, architects and contractors need to work to fully understand the prefabrication process and engage in extensive pre-project planning, early engineering design completion and close project management to ensure each stage of a project is completed in a coordinated fashion.
Bisnow recently spoke with Ware to learn more about what the industry might be missing about prefab, as well as the true benefits of this burgeoning methodology and how they can make the most out of them with their chosen prefab solution.
Bisnow: What are some common misconceptions people have about prefab?
Ware: One of the biggest misconceptions is that prefab only brings value to a project if it’s saving money. Too often, people want to plug-and-play prefabricated solutions into their project without changing their proposed process at all and are then left wondering why they aren’t saving money. The real questions they should be asking themselves are why the rest of the construction process costs so much, and why continuing to use that same flawed process makes sense.
Prefab isn’t just about saving costs. It’s about addressing the issues that have led construction costs to rise in the first place. For example, the labor shortage. With prefab, certain components or assemblies can be built using fabricators, allowing for the optimization of on-site work, and solving for the shortage of workers.
Key stakeholders should shift their focus a bit. Instead of centering solely on hard cost comparisons, they should also consider the other ways prefab can benefit their project and the industry. On a direct one-to-one cost basis, prefab construction is not cheaper than traditional construction. However, time is money, and prefab can considerably shorten construction schedules when properly integrated. This means that the revenue and occupancy stage can begin much sooner, which accelerates investment returns.
Another misconception centers on timing. Too often, teams look to prefab to save a project once it’s already behind schedule. Prefab should be integrated into the process from the very beginning. Project teams and stakeholders should take their time to truly understand prefab as a methodology — slow down their design process to focus on the prefabricated elements that will end up benefiting them greatly in the end. That’s what prefab is truly about: Slowing down the design process to speed up the build. If you take your time in the beginning, you will discover increased savings in the latter project phases where the costs tend to be much higher.
Bisnow: VANTIS combines prefabrication with the design-build methodology. What does that look like?
Ware: The Achilles' heel of prefabrication has been the pre-construction phase. When developers, architects and contractors come together to design a project, things tend to fall into two categories: construction methods and products. Prefab is an actual method of construction but is too often viewed as just a product. This doesn’t bode well for prefab as it can often get ignored or placed in the wrong stage of development due to this lack of understanding. It should be noted that if prefab is being used in any portion of a project, then it impacts every part of the project — from the design to the budget to the schedule.
With new innovations and improvements in manufacturing, customization, quality, performance and sustainability, prefab construction is no longer relegated to cookie-cutter options. In fact, many solutions now feature customized designs that incorporate green and smart tech.
Prefab construction is more than just a solution, it’s an approach that involves front-loaded design and requires familiarity with the process. By integrating prefab with the design-build methodology — which involves all project stakeholders from architects to fabricators to contractors working together from the very beginning and throughout each stage of design and construction — everyone involved has the opportunity to learn more about prefab, explore its benefits, work it properly into the design, and make key structural, mechanical and electrical decisions. It's about repetitiveness and learning from the challenges faced early on in your prefab integration experiences in the same way we’ve done with conventional construction.
Bisnow: What are some of the challenges of traditional construction that VANTIS’ prefab methodology helps solve?
Ware: Construction projects are labor-intensive, and the industry has had an ongoing challenge attracting enough skilled workers. This chronic issue has been exacerbated by the current pandemic, adding significant time and cost to many projects.
VANTIS’ prefab methodology shifts away from traditional labor-heavy, weather-dependent, site-based construction by utilizing a technology-enabled design-build approach to streamline the entire construction process and reduce labor requirements. For example, the software we use during design and off-site fabrication stages to perform build inspections and proactively fix issues that would normally need to be fixed by people on-site. As a result, that same on-site crew can instead focus on prepping the site for construction. This translates to optimization of worker productivity, and shorter project timelines by allowing various parts of a project to be undertaken simultaneously.
Another challenge made clear to us during this pandemic is that we can no longer thrive in a static world. As tenant needs have changed, a lot of building owners have been unsure of what to do to or with their spaces. Many discovered that if they stuck with the same static approach their building was constructed in, their options would be limited and costly.
By utilizing the many advancements in construction technology and prefab solutions, it’s now possible to design flexible spaces that can be easily adjusted to accommodate changing needs and landscapes, allowing for the creation of more intelligent spaces.
Ultimately, it’s not about predicting the future, but designing spaces that make new challenges easier to overcome when that future arrives. The industry has incredible inertia, and to successfully address the challenges that will surely come, we must rethink how we design and build buildings. We must slow down and take the time to move the industry in a different direction — to commit ourselves to the continuous development of smarter and more efficient construction methods that solve the real underlying problems and drive better outcomes.
This article was produced in collaboration between VANTIS and Studio B. Bisnow news staff was not involved in the production of this content.
Studio B is Bisnow’s in-house content and design studio. To learn more about how Studio B can help your team, reach out to studio@bisnow.com.