‘Medication For The Pain’: How Prefabrication Can Help Businesses Achieve Sustainability Goals
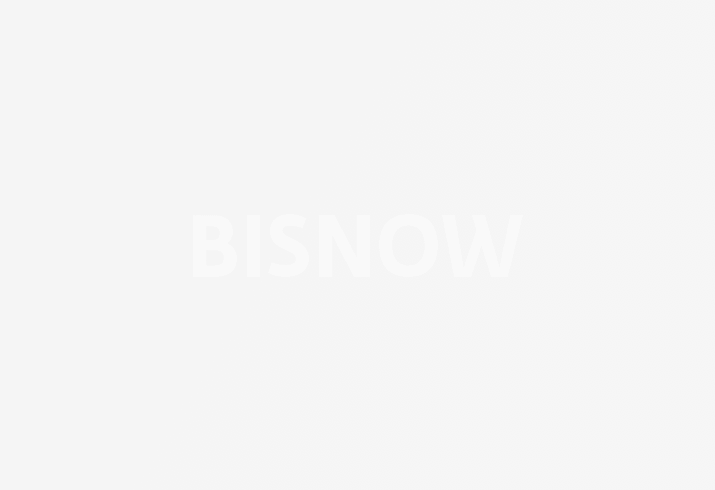
The commercial real estate and architectural/engineering/construction industries want to embrace sustainability, but they often find that this is easier said than done.
CRE is under growing pressure from regulators and investors to reduce its emissions, but there is little guidance on how to do that. Additionally, owners and developers who want to build sustainably are likely finding it difficult to procure many of the materials they need for new projects, let alone low-carbon-emitting sustainable materials.
This is no small matter: Buildings generate an estimated nearly 40% of carbon emissions globally. Their operations alone are responsible for 28% of total global carbon releases while building materials and construction activities contribute to another 11% of emissions.
Reducing a building’s carbon footprint in today’s regulatory and business environment is enough to give anyone a headache, but Geene Alhady, president of Clark Pacific, believes a remedy is available if the industry is willing to rethink the building process.
“Prefabrication is definitely becoming what I call a medication for the pain,” he said. “It can help address the current limited access to materials and labor and the concerns about sustainability.”
Clark Pacific’s off-site construction approach allows entire building units to be manufactured at one of its California facilities and then installed on-site by a small, trained crew. This process, which avoids the traditional design-bid-build model, is less vulnerable to supply chain disruptions because Clark Pacific orders its materials far in advance to keep its manufacturing operations humming right along.
Once the prefabricated panels and components are delivered to the job site, the process generates less carbon than conventional methods that require a large fleet of diesel-consuming heavy equipment. But that is not the only sustainable aspect of the process.
Clark Pacific prioritizes sustainability in its products, including in its recently developed NetZERO Building Platform, Alhady said.
A thermally active concrete floor system combined with a thermally isolated building facade system results in its NetZERO office structures having a 40% smaller carbon footprint than other buildings, according to Clark Pacific. In addition, the platform uses 100% outside air to enhance tenant health and comfort while reducing a building’s energy consumption by 30%.
Those are appealing statistics to Clark Pacific’s customers, Alhady noted, particularly for developers of large corporate or biomedical campuses in California looking to add buildings.
“When it comes to the actual product itself, we're able to use low-carbon concrete to deliver a design that meets industry standards,” Alhady said. “In addition, more than half of the energy consumed during our prefabrication process at the factory is provided through solar energy.”
The company is taking its commitment to renewable energy even further. In April, Clark Pacific announced it would work with NewGen Energy to install solar arrays at all of its facilities, transitioning its energy consumption to nearly 100% renewable by the end of this year.
Alhady said the effort reflects Clark Pacific’s commitment to the “quadruple bottom line.” This framework takes the elements of the well-known “triple bottom line” — people, planet and profits — and adds a fourth: purpose.
“The quadruple bottom line takes a holistic view of doing business,” he said. “It allows us to do the right thing and to be a successful organization at the same time.”
Alhady said other organizations thinking of adopting a similar philosophy might consider making prefabrication part of their building strategy.
“Companies developing megacampuses in Silicon Valley are looking to adopt a standardized approach to building, but also want to retain a uniqueness to each site,” he said. “Those are very likely users of prefabrication.”
Rather than selling them a one-size-fits-all product, Clark Pacific prefers to partner with its clients to help them develop and then achieve their sustainability goals, Alhady said.
“They look to us to help them understand how our methodology will help them get closer to their goals,” he said.
Prefabrication technology has advanced quite a bit in recent years, he said, meaning clients don’t have to make nearly as many design trade-offs compared to traditional design and construction methods. In the process, the sustainability of prefab buildings has advanced, too.
“Prefabrication and sustainability are very interdependent,” Alhady said. “And you are most likely to achieve a sustainable building when the sustainability goals are designed into the product.”
This article was produced in collaboration between Studio B and Clark Pacific. Bisnow news staff was not involved in the production of this content.
Studio B is Bisnow’s in-house content and design studio. To learn more about how Studio B can help your team, reach out to studio@bisnow.com.