‘Adding Fuel To The Logs’: Construction Materials Prices Continue To Soar
The coronavirus pandemic has had a protracted impact on the construction industry, exacerbated by pre-existing trade tariffs on construction materials. Beyond the complications of workers falling ill and job sites shuttered last year due to shelter-in-place orders, high prices and slow delivery schedules for construction materials such as lumber and steel have maintained a stubborn strain on the industry.
The supply chain issues and rising costs began about a year ago when public officials across the nation issued orders halting work on many construction sites. As soon as those restrictions started to lift, there was a rush of demand for residential homebuying from people wanting to upgrade their square footage or achieve homeownership for the first time, which created a surge in demand for construction materials, according to Ken Simonson, chief economist of the Associated General Contractors of America.
This followed sweeping logistical challenges resulting from the pandemic and shutdown hampering production and distribution facilities' ability to fulfill the need for materials. It coincided with a rise in remodeling work and ventilation system upgrades for schools and other facilities to accommodate social distancing protocols, also driving demand.
“All of this caused huge disruptions to the supply chain for many materials just as the demand came roaring back,” Simonson said. “And sawmills in particular, once they shut down, it wasn't necessarily easy to resume production to get the logs coming in and so forth. So, they've been playing catch-up for almost a year now.”
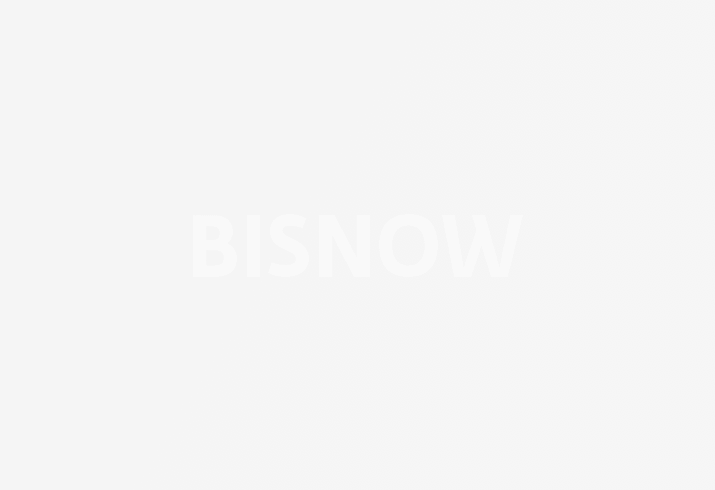
Simonson said that he isn’t surprised by the increases in the price of construction materials given the steep rise in home construction and because many lumber mills were shut down beginning in 2006. Given the need for specialized skills to operate and work in sawmills, it isn’t something that can be revived overnight.
“The pandemic caused this huge V shape in terms of near shutdown of demand and a very strong bounce back almost immediately,” Simonson said.
Even though a year has elapsed since the pandemic’s onset, the trends continue. The selling price for materials and services for new nonresidential construction increased by 2.5% between December 2020 and January 2021, and 10.7% since April, according to a Bureau of Labor Statistics statement.
However, what contractors said they would charge to build new nonresidential construction increased by a mere 0.2% during the same time frames.
Softwood lumber prices have increased by 73% year-over-year, and iron and steel prices are up by 15.6%, according to data from the Associated Builders and Contractors.
Arntz Builders President Brian Proteau said he has seen prices for softwood lumber for framing increase by as much as 110%.
“We've seen a collective increase in contractors bidding on projects than normal,” Proteau said. “For whatever reason, they're coming in. On the average job, before, there would be four to five different bidders maybe, now they're up around a dozen.”
Even with the rise in materials pricing, more contractors are bidding on projects, a phenomenon Simonson said he witnessed in the previous recession where a lack of projects sparked increased competition among contractors while they absorb the cost increases, at least initially.
“Clearly contractors normally operate on pretty thin margins — they’re not in a position to keep absorbing these materials costs increases and the costs associated with delays, and also the additional costs on-site for personal protective equipment, sanitizing and so forth,” Simonson said. “So I think that owners should be prepared to see higher prices in the next round of bids.”
The cost increases are in part a reflection of the delivery delays for materials experienced over the past year. Contractors that want materials delivered on schedule have to pay more for expedited fulfillment.
The delays are global. Reports of congestion at the Port of Oakland, Long Beach, Los Angeles, and ports on the East Coast have added to the challenges as many materials come from China and other countries.
Swinerton Division Manager Lori Dunn-Guion said she had seen the congestion firsthand when driving across the San Francisco-Oakland Bay Bridge, seeing ships idling in the bay due to the bottleneck. She said a shortage of shipping containers and port closures in China have compounded the issues.
“This shipping container shortage, this is something that's been as recent as a few weeks ago, and we're still trying to turn a corner on it,” Dunn-Guion said. “So the idea that we're still dealing with some of the port delays a year after the pandemic started is pretty surprising. But we're trying to be flexible, and we're trying to think outside the box and come up with solutions to resequence activities when we can, to try to help mitigate the effects of what we're seeing.”
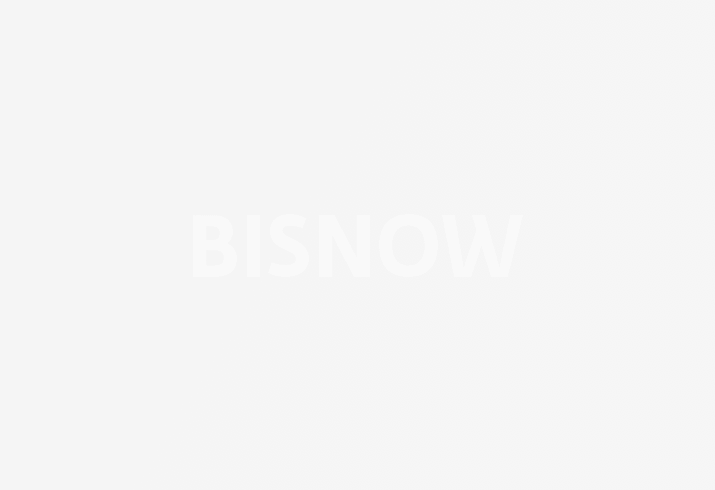
Practicing resequencing of construction activities to work around the material delivery delays has been effective in keeping Swinerton’s projects on schedule, Dunn-Guion said.
Arntz Builders, which primarily does public works projects and sources materials from the East Coast, has increased lead time on orders, which Proteau said has helped prevent impacts on project timelines. He said that the company has been absorbing some of the increased costs but has also adjusted bid pricing.
“We're certainly asking our vendors to hold their pricing longer than we typically would just because we are seeing spikes in materials such as lumber and steel,” Dunn-Guion said. “Secondly, I would say that we're ordering our materials much earlier than we would have probably a year ago. So, it's really incumbent upon us to try to get our orders in so that we can lock in that pricing.”
Whereas in the past, a pricing hold would typically be for 30 days, now 90-day holds are being requested, Dunn-Guion said.
Although some contractors may be successful in averting the impacts of project deliveries, not all have been as fortunate. In December, an AGC survey revealed that of the over 1,300 contractors who responded, over 75% reported experiencing a project cancellation or postponement. Only 25% said that they had won a new project or an add-on to an existing project due to the pandemic.
“Contractors must be mindful of potential rapid input price inflation as they enter into new contractual obligations,” Associated Builders and Contractors Chief Economist Anirban Basu said in a statement. “Given the softness in demand in a number of key nonresidential construction segments, the temptation may be to bear the risk of future price increases in exchange for increasing the likelihood of securing new work. That strategy may work out, but estimators, attorneys, executives, and others should be aware that the accompanying risks of such approaches are elevated.”
Policy changes could help to alleviate some of the hardships. In 2017, the Trump administration intensified existing trade rifts with Canada by imposing tariffs on Canadian lumber, the L.A. Times reported. Although the tariff was dropped from 20% to about 9.5% last fall, according to Simonson, the AGC has requested that the Biden administration rescind the tariffs that add to the high prices.
Despite the high lumber prices, timber growers in the South are struggling financially. Meanwhile, Canadian lumber companies are making profits by buying U.S. sawmills to avoid the tariff penalty, The Wall Street Journal reported.
“We think in the current situation that's just adding fuel to the logs as it were in terms of pushing up prices unnecessarily at a time when they're already at record levels,” Simonson said. “So we certainly think it's appropriate to remove the tariff.”
Furthermore, Simonson cited the need for a review of U.S. processes for clearing international commerce, such as holding trucks at borders for lengthy inspections, preventing a truck transporting lumber mill products from British Columbia to move expeditiously, thus becoming yet another factor driving up prices.
“Left unchecked, these rising materials prices threaten to undermine the economic recovery by inflating the cost of infrastructure and economic development projects,” AGC CEO Stephen E. Sandherr said in a press release. “Widespread harm is caused by maintaining tariffs on products that so many Americans need to improve their houses, modernize their infrastructure and revitalize their economy.”