Modular Construction Has An Image Problem. Housing Proponents Are Trying To Fix It
Modular construction is increasingly popping up in the Bay Area and elsewhere as a sustainable, lower-cost, quicker way to deliver affordable housing, but unfamiliarity and misconceptions are curtailing its use.
Although some aren't ready to think outside the stick-built box, certain commercial real estate companies, tech companies and those fighting for affordable housing creation are pushing for a modular approach to at least be considered across the board.
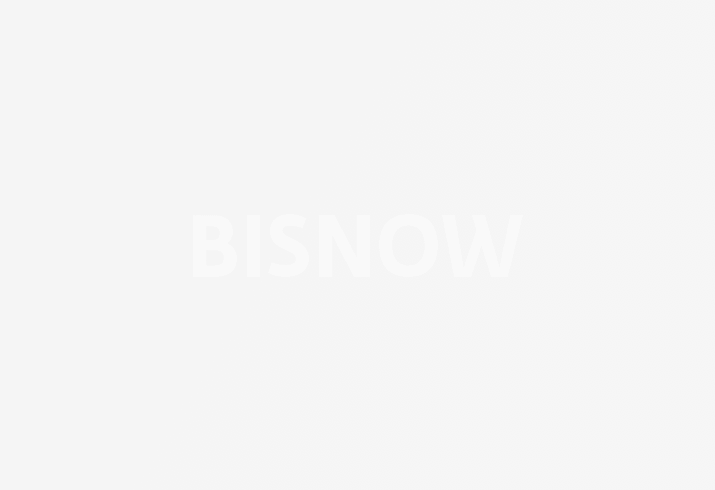
The image issues stem in part from confusion around the definition of modular construction. Prefabrication is an umbrella term covering a range of building types from modular to panel construction to manufactured structures. The lumping together of these different types can leave the impression that it is all akin to mobile homes.
While mobile or manufactured home construction has advanced in quality and sophistication from prior decades, the moveable nature does not lend itself to standing the test of time compared to conventional construction. Conversely, other prefab construction types such as modular are slowly earning a reputation as high-quality, durable, aesthetically pleasing and greener.
Modular, which utilizes factory-assembled prefab units or modules that can be stacked together in flexible ways, is particularly growing in popularity as a means to deliver multifamily product to the housing-starved Northern California region where groups seeking to block new development in general often prevail in at least stalling projects.
“The downside of being in the Bay Area is we've got all these problems, but on the upside, this is sort of the Paris of the 1920s as far as being at the center of the world of innovation,” Lowney Architecture President Ken Lowney said. “Most people think of that in technical terms of software and computers and interconnectivity. There are people moving to the Bay Area specifically for entrepreneurial culture and sophistication that's here to help solve this problem.”
Lowney, who said his firm leads the western U.S. in modular design, has been working on prefab construction for the past decade, resulting in over 60 projects at various development stages, and he has worked with factories in multiple countries. He said that although several factors like high construction costs and the housing and homelessness crises have driven modular construction to the forefront, what he called psychological barriers persist against making it more ubiquitous in the world of construction.
The first barrier Lowney cited is the not-in-my-backyard, or NIMBY, attitude typical in many Bay Area communities. People say more housing should be built, just not near them. The second, he said, is the risk profile associated with modular, as considerable sums have to be paid to a factory upfront for the work to begin, while the factory itself could end up going out of business, a situation that happened to Lowney on a couple of occasions.
“Another psychological barrier is the lack of similarities and complexity of the process,” Lowney said. “It's not like building and thinking as you would with a site build. So all the decisions have to be made upfront, and there's a steep penalty if you change your mind later in the process. There are multiple permits that have to happen. There are a lot of moving parts to that. There's a lot of grayness. Even if you're familiar with it — it's one thing to talk about it over a beer, and it's another thing to invest millions of dollars in it.”
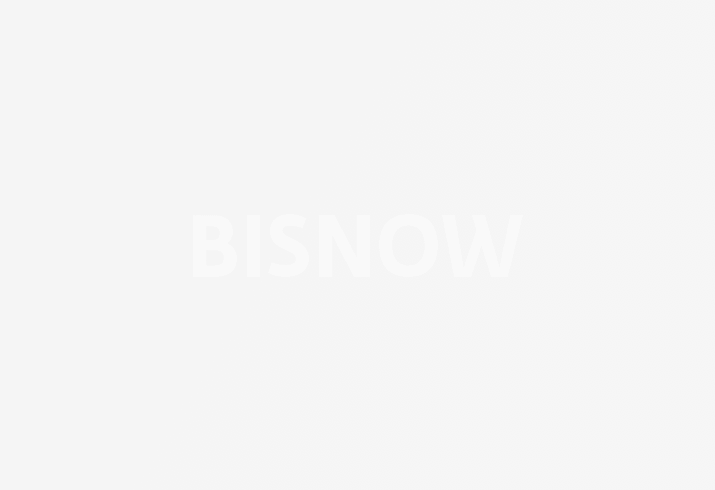
Still, the burgeoning building type is steadily being championed by groups that work with those on the economic margins. Alicia Garcia, associate director of WeHOPE, first delved into modular construction when she joined the board of directors of a startup called United Hope Builders based in East Palo Alto, which works to build steel modular dwellings for disadvantaged communities. In her work with WeHOPE, Garcia is part of a team of service providers for those experiencing homelessness and realized that only through the building of affordable housing for those with extremely low incomes can the homelessness crisis be solved.
After touring the country, speaking with experts and searching for solutions, modular construction emerged for Garcia as an effective and lower-cost way to build housing.
“Our model is to partner with cities, counties, churches and other landowners to place these units on their land and to buy some of our own land in the future so that we can provide energy-efficient, stable, nice homes so that homeless people can become formerly homeless people and live with dignity,” Garcia said.
Working with Idaho-based modular home factory indieDwell, Garcia said that her group has just placed two modular housing units on a city-owned property in East Palo Alto that will soon become home to two homeless families. Habitat for Humanity also just finished a 32-unit modular building in San Jose on city-owned land. Garcia said she sees modular as having far-reaching potential, such as being used to supply more student housing.
For Lowney, modular construction shows promise far beyond enabling projects to be built faster and with lower price tags. Growth in conventional construction productivity lags behind other industries and costs the global economy $1.6 trillion per year, according to a report by McKinsey & Co. Lowney said he thinks change is afoot with technologies like automation and 3D printing entering the field.
Another Idaho factory, Autovol, is harnessing robotics and automation to help build Virginia Steel Studios, an apartment complex that is nearing completion in San Jose, according to a press release. CEO Rick Murdock said in the release that automated modular construction would "take the back-breaking work off of people, and use new techniques that weren't humanly possible."
Meanwhile, Mighty Buildings, based in Oakland, just received $40M in Series B funding to build affordable housing using a combination of 3D printing, robotics and automation, TechCrunch reports. The company claims it can 3D print a 350 SF apartment unit in a single day.
Such industry changes have sparked opposition from S.F.’s building trades unions concerned about slipping work quality standards and lower wages on modular projects not made by union hands. Factory_OS, based on Mare Island in Vallejo, stands out as a union shop that has partnered with the Northern California Carpenters Regional Council employing hundreds of union workers. Factory_OS, which just received $55M in Series B financing from Autodesk, Citi, Facebook, Google, Morgan Stanley and Lafayette Square, said in a press release that it can drive down production costs by 20% to 40% and can build 40% faster than conventional construction.
Factory_OS fabricated the modular components for a supportive housing project in Mission Bay developed by BRIDGE Housing and Community Housing Partnership. The project will deliver 140 housing units with a groundbreaking late last year and is part of Mayor London Breed’s Homelessness Recovery Plan.
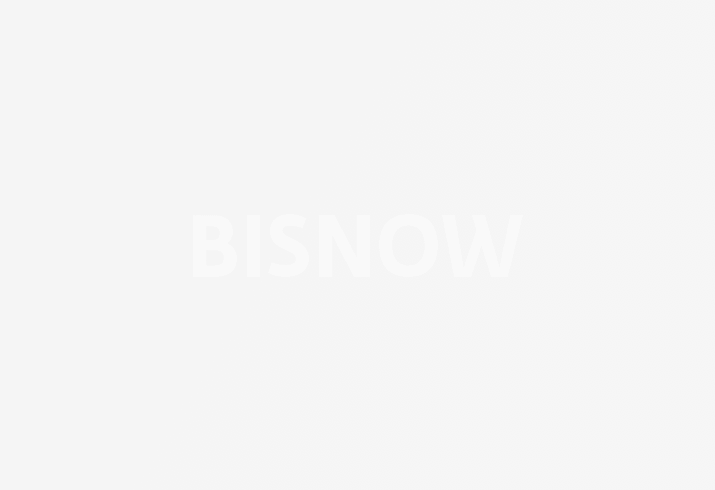
Lowney said a number of factors determine whether a modular approach is viable for a given project. One is that prefab factories are scarce and may or may not have work schedules that mesh with development teams' timelines. He also said current limitations result in modular projects, in reality, being hybrids. For instance, custom site-built foundations and roofs are common. Utility connections still have to be made on-site.
An intentional hybrid approach can serve a purpose, as is the case with an intergenerational affordable housing project at 4300 San Pablo Ave. in Emeryville. Developed by EAH Housing and designed by KTGY Architecture + Planning, the project will supply 68 housing units for seniors and youths transitioning out of foster care under a flexible construction approach. One option under consideration is to use a mass timber ground level for a reduced carbon footprint and then either proceed with stick-built or modular for the units above.
“Using mass timber on the base just opens up a whole other toolkit for us,” KTGY principal Jessica Musick said. “Just the natural warmth that is associated with mass timber — our hope is that it gets expressed on the exterior of the building, so as a pedestrian walking down the street, you see the inherent warmth of the material. That's a big difference than with concrete. Concrete can be beautiful, but this has inherent design qualities to it where you don't have to try so hard as with other building materials or other potentially costly design moves.”
Musick said she expects that with continued high construction costs, modular flex options will increasingly be considered for projects where designs will be laid out in a “modular-ready” fashion. Some firms are also researching whether a mass timber/modular hybrid approach may have advantages from an engineering standpoint beyond just the aesthetic upsides.
“Our goal was to provide EAH the flexibility and a little bit more time to make that decision,” Musick said.
From Lowney’s view, the prospect of going 100% modular would be ideal if it results in cost savings. He said he likes the quality assurance and control in a factory environment coupled with saving 15% in construction costs and delivering product 35% to 40% faster.
In the Bay Area, where developers struggle with getting project proposals to pencil, some consider modular as a way to build more cheaply. Lowney cited the Mayfair project in El Cerrito his firm is nearing completion on as an example of modular construction with no compromises on quality or appearance. The project is a transit-oriented development near BART that offers 223 housing units, 67 of which are designated affordable. With a landscaped courtyard and a mix of colors and design elements on the facade, no passerby would think it was modular, Lowney said.
“I think that modular should always be considered and then eliminated if it doesn't make sense for the particular project,” Lowney said. “But in many instances, it is a very beneficial solution that will save money and time."