To Coat Or Not To Coat — That Is The Question Facing Owners Of Aging Masonry Buildings
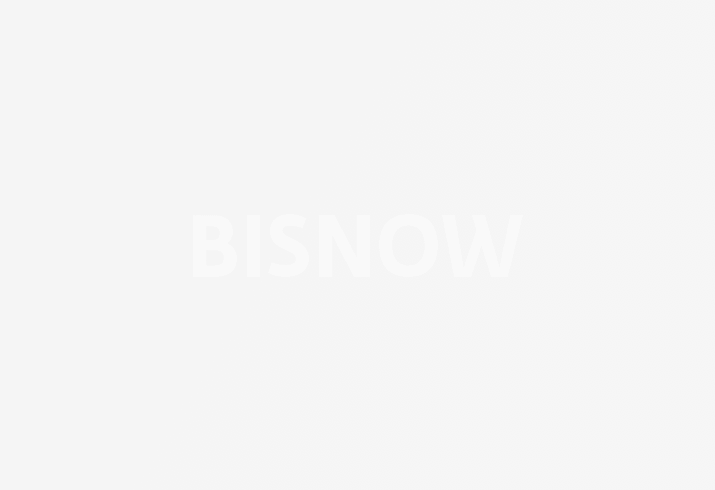
There are certain things in life that you can’t take back. One of them is the application of a solid pigmented acrylic coating to address water intrusion through a masonry wall.
If properly detailed, the coating can adequately address water infiltration to a commercial or residential building and avoid the need for expensive brick replacement. But if it is not properly detailed or applied by a competent contractor, a poorly chosen coating might create expensive, long-term consequences for the owner.
Licensed architect and Klein & Hoffman Senior Associate Mike Naponelli advises clients to consider all other options with an engineer or architect before they hire a crew to apply a masonry coating.
“Our first effort is always to try to avoid putting a coating on,” Naponelli said. “We always try to repair what's there with other methods that will last longer and not impact the aesthetics or performance of the masonry wall.”
Masonry walls face many long-term threats, including weather and aging. But nowadays, they also might be imperiled by well-meaning home improvement shows, which have normalized the idea of putting a layer of paint on an old brick exterior to hide signs of aging.
“I always cringe when I see that because they don't realize what they've created,” Naponelli said. “We do not recommend applying paint coatings for aesthetic purposes because it becomes a continual maintenance item and could potentially cause damage to the masonry if not installed properly.”
Naponelli said building owners need to understand that coatings are “essentially permanent.” Worst case, they can be removed but that is a very expensive step that is likely to damage the underlying brick, he warned.
An old brick wall will naturally be suspected as the source if the building is experiencing water intrusion, which Naponelli said is often the reason an owner reaches out to the architectural and structural engineers at Klein & Hoffman for help. Naponelli said his firm will take a holistic look at the issue that considers all potential problem sources, such as poorly sealed windows or internal wall condensation.
A careful inspection of exterior walls is made, followed by maintenance and surface preparation to address brick and mortar problems that come to light.
“Things like open and deteriorated mortar joints should be repaired prior to installing coatings,” Naponelli said. “Installing a coating without taking these precautions could further damage the walls and cause premature failure of the coating. If this happens, the wall will need more repair and the coating would need to be removed, if it’s even possible.”
If it is determined that a coating is a viable option, the next step is to identify the most suitable product to apply to address the problem. As Naponelli noted, “not all coatings are equal,” and a poor choice can compound the building’s problems.
“Some buildings rely on moisture vapor drive from the interior to exterior, and a coating can inhibit the breathability of the wall,” he said. “Blocking or inhibiting the moisture vapor drive can cause spalling of the brick face, deterioration of the mortar joints and peeling of the coating.”
To avoid this, Klein & Hoffman will perform mock-ups to test whether a coating achieves what it is expected to do. That can take time, but it will help avoid further costs down the road.
“You should expose mock-ups to the weather for up to a full year if possible,” Naponelli said. “In situ testing should be performed as well to confirm adequate bonding of the new coating to the substrate or any underlying coatings.”
This is the approach Klein & Hoffman recently took to help the owner of a more than 50-year-old multifamily high-rise. About 35% of units in the building were experiencing water intrusion due to deterioration of the masonry walls.
“They had applied a coating in the early 2000s to address water infiltration; however, cracks were forming in the coating where open mortar joints were telegraphing through,” Naponelli said.
The owner was considering rebuilding its brick exterior, which would have cost about $4M, Naponelli estimated.
To avoid that expense, Klein & Hoffman tested coating candidates for about a year on mock-ups while the coating manufacturer performed bond testing. As a result, the owner felt confident in the coating selection, and after preparation work and application of the selected coating, the water infiltration has stopped — for a fraction of the cost that would have been required to replace the bricks, Naponelli said.
However, Klein & Hoffman also reminded the owner that coating solutions like this require regular maintenance and eventual reapplication to remain effective.
Naponelli urged building owners to work with contractors who understand the subtleties of masonry coating application and maintenance. An architect or engineer can assist with the necessary mock-ups and testing protocols, and can provide the recommended work plan and detailing.
“If you hire someone that doesn't know what they're doing, they may not understand how important surface preparation is,” he said. “You can use the best coating that money can buy, but if the surface isn't prepared properly then it's going to fail. That’s why it is important to have both the right architect and contractor selected for the team.”
This article was produced in collaboration between Klein & Hoffman and Studio B. Bisnow news staff was not involved in the production of this content.
Studio B is Bisnow’s in-house content and design studio. To learn more about how Studio B can help your team, reach out to studio@bisnow.com.