Are 3D-Printed Buildings A Viable Cost-Saving Solution For Developers?
In the past decade, the ability to 3D-print buildings has become one of the latest, though still controversial, technological advancements in the construction industry.
What was once used to manufacture small objects, figurines and vehicle prototypes is now being used to construct affordable and emergency housing in developing countries.
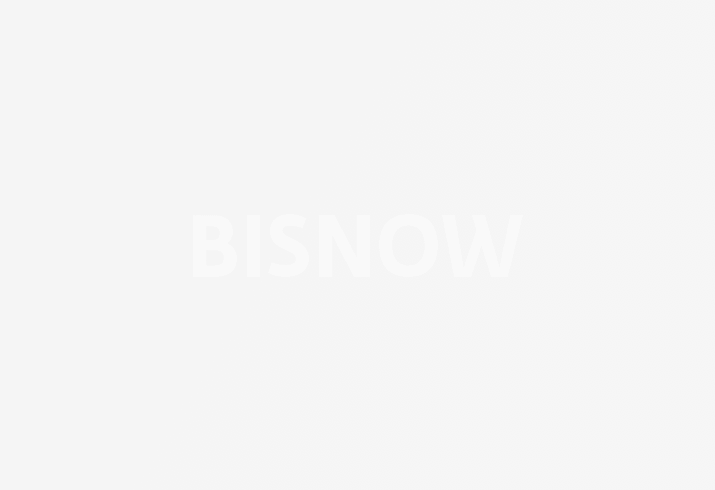
Developers across the globe are experimenting with the cutting-edge technology, using massive 3D printers to build entire housing communities and even commercial buildings — though sources told Bisnow the technology still has a long way to go before being widely adopted in the U.S.
“3D printing buildings is an interesting emerging technology but is, unfortunately, years if not decades away from being viable in the United States,” Carrier Johnson + CULTURE Digital Practice Manager Casey Mahon said. “There are a lot of building codes, life safety and constructability issues that still need to be resolved before people actually can inhabit a 3D-printed structure.”
Though international companies have used the technology to build more cost-efficient housing (some between $4K and $10K a unit), there remains a harrowing number of questions surrounding the safety and habitability of 3D-printed houses.
Most of the innovative 3D-printed structures across the globe are one-off projects that have yet to create a regulatory pathway to getting these buildings approved so they can be mass-produced, said Jerry Neuman, a commercial real estate attorney and land-use expert with DLA Piper. There is not a system in place that would allow inspectors in the field to examine the 3D-printed buildings for structural integrity, plumbing, electrical and other public safety concerns before providing occupancy permits.
“There are certainly discussions about 3D printing creating a low-cost alternative to housing construction, which can assist in the affordability crisis we’re seeing. That said, I think it is not a short-term solution,” Neuman said. “We haven’t really been able to create the body of regulations that would be necessary to ensure its safety or have those processes evaluated.”
How It Works
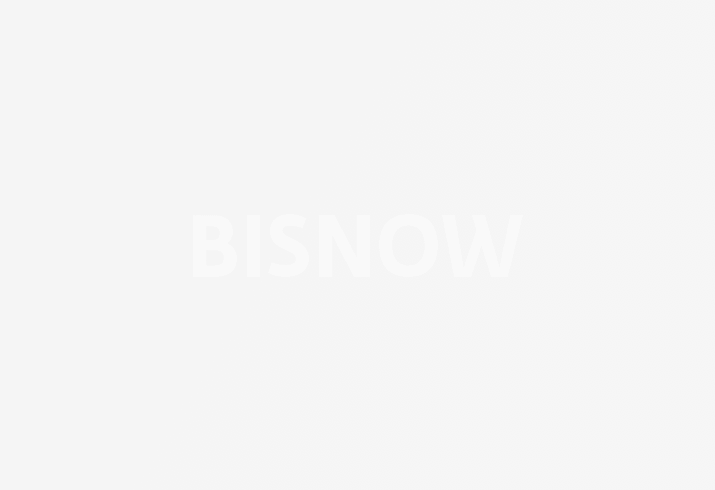
Whether they are portable printers used on-site or are housed in a warehouse, 3D printers have the potential to completely revolutionize the built environment.
The printers work around the clock to complete a structure using various materials depending on the project, from concrete, steel and plastic to more natural materials like wood or bamboo.
In a construction technique known as additive building or additive manufacturing, 3D printers essentially scan a project’s blueprints, then use softened concrete to build the structure layer after layer, somewhat like a multi-layered cake.
With construction costs skyrocketing, high housing prices and homelessness a growing issue across the country, 3D printers could greatly cut down on the labor and costs associated with homebuilding, which according to the Observer, accounts for 61.8% of a house’s price. Questions remain regarding whether this process can be regulated in the U.S. and emulated on a large scale in the near term.
“The examples of 3D-printed houses that exist in places like China, Russia, EU and on academic campuses around the country are really more proof of concepts than products [and] techniques ready to be deployed to address the growing housing shortages affecting many states like California,” Mahon said.
The Dream
One driving factor behind the 3D printing fanfare is the idea that these printers can be used to build homes and establish communities in developing countries, bringing shelter, electricity and plumbing to families in need.
An organization called New Story is raising funds to build 100 3D-printed homes in El Salvador. The nonprofit is partnering with Texas-based ICON, a construction tech and robotics company with a focus on affordable housing, to raise $1M and build these homes within the next two years.
The two have had success with the technology. In early March, New Story and ICON built a 3D-printed house featuring three bedrooms, a living room and an office for $4K in under 24 hours. They unveiled the home at Austin’s SXSW festival.
"We want to bring this to the families who need it the most," New Story CEO and co-founder Brett Hagler told CNN.
New Story has funded the construction of more than 850 homes in Haiti, Mexico, El Salvador and Bolivia. Most of these homes were built using blocks of concrete, took 15 days to erect and cost around $6K to complete.
Across the Atlantic in Dubai, San Francisco-based engineering firm Syska Hennessy Group partnered with the UAE Prime Minister’s Office to help design and build a fully functional 3D-printed commercial building at the Dubai Future Foundation.
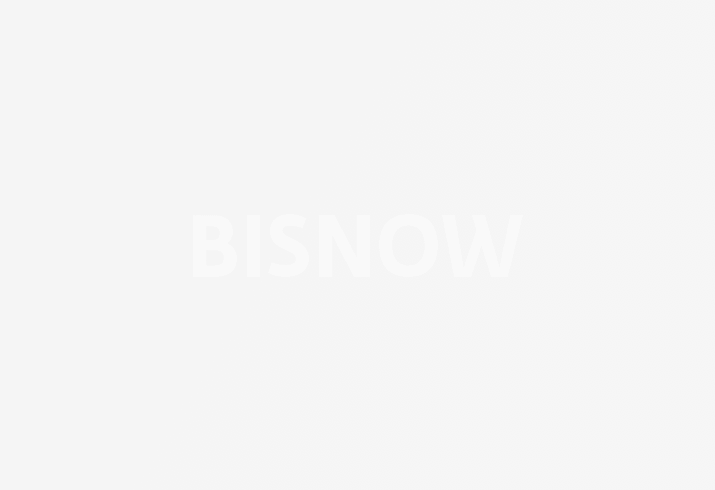
Known as the Office of the Future, the building is housed on Dubai’s Museum of the Future campus. The nearly 2,700 SF flexible office was built using a 20-foot-tall, 120-foot-long and 40-foot-wide 3D printer, one of the world’s largest, according to Syska.
“It's not a specific area of focus for us, but we do like to embrace innovative approaches,” Syska Senior Principal Robert Bolin said. “So when something like this comes along we’re usually very interested in seeing how we can participate.”
Syska helped design the infrastructure for electrical wiring and HVAC systems to make the building inhabitable, such as integrating pathways for electrical conduits. Most of the building was printed in China, shipped in containers to Dubai and assembled on-site in 17 days, Bolin said. From start to finish, about 18 team members worked on the project, and companies involved included PMKConsult, Gensler/Killa Design and China State Construction Engineering Corp.
“It was quite a fast and fascinating exercise,” Bolin said. “The level of integration we had with the building system was perhaps not as integrated as we would have hoped, at least for this commercial approach. Lots of lessons learned though.”
Academics and nonprofits are not the only ones experimenting with this technology. In New York City, architecture and engineering firm Edg plans to use 3D printers to restore the facade of historic buildings and to help design new building facades.
“It’s just hastening the process of construction,” Edg partner and Design Director Richard Unterthiner said. “You’re going to have with all these systems greater efficiency and speed, you can do more complex things and achieve them quicker with more economy in mind.”
Edg co-founding partner John Meyer said the goal is to use 3D-printed materials to replicate a building’s existing facade or to create a new ornamental element for a building.
“We want other people to run with this concept too. I think the challenge [is] anything new within construction is not really welcome for a lot of reasons,” Meyer said. “If you’re doing something different, it’s pretty scary.”
Structurally Sound
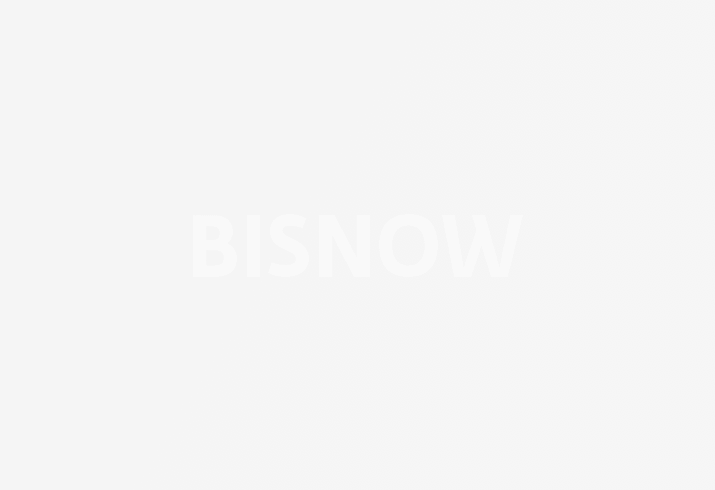
Though the tech offers a quicker way to deliver homes, 3D printing carries risk.
For one, the concrete lacks the structural reinforcement of traditional concrete because the layers are built one atop the other.
“3D-printed buildings are certainly in there fad stage, but the potential is there,” InVision Advisors President and architect Jonathan Moore said. “The basic problem is the technology does not exist to respond to a structure's need to act in both tension and compression. As new materials and new printing technology [are] developed, this will certainly change, but right now it is basically a pile of ooze that is either burned or melted into the shape of the building.”
Eindhoven University of Technology Professor of Applied Mechanics Akke Suiker created a formula to guarantee the structural soundness of 3D-printed straight wall structures. Suiker told 3DPrint.com in February that his formula helps determine the rate at which concrete layers can be piled on top of each other and remain structurally sound without collapsing or falling under their own weight.
“The insights provided by the model create essential basic knowledge for everyone who prints 3D structures,” Suiker told 3DPrint.com. “For structural designers, engineering firms but also, for example, for companies that print thin-walled plastic prostheses of small dimensions, because that is where my equations also apply.”
Some experts believe the wide adoption of 3D-printed materials to build entire homes and commercial buildings is far off, and the cost cuts associated with the tech may not be worth the initial investment.
"I haven’t seen any actual reporting from contractors and/or housing developers that indicate building a structure this way would be more cost-effective,” Mahon said. “There is a brick-laying robot that is currently deployed alongside masons to execute brickwork on long linear walls that can lay [six times] the average amount of bricks in a day than a typical mason. That sounds like cost savings until you factor in the cost of the machine, maintenance and the four highly trained engineers it takes to operate the equipment. You’re probably breaking even.”