Want Masonry Or Stained Concrete On That Facade? How Prefabrication Offers A Range Of Exterior Options
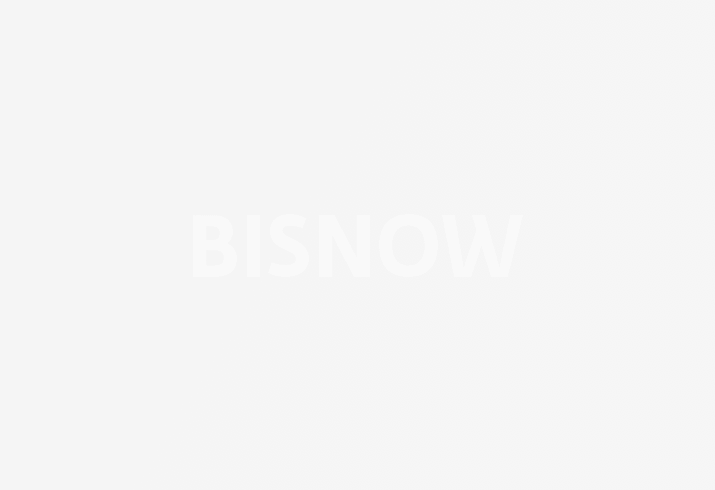
Passersby might assume the 2100 Kettner building in San Diego’s Little Italy has been a neighborhood fixture for decades. The masonry facade that covers much of the six-story mixed-use building recalls an era when most commercial buildings were truly brick-and-mortar and hand-built by skilled craftsmen.
But in fact, the building was completed in 2021 with the majority of its exterior components designed and prefabricated off-site by Clark Pacific. Once the pieces were delivered to the job site, the California-based manufacturer and contractor assembled them in a fraction of the time a conventionally built facade would have required.
To achieve the building exterior’s ageless look, Clark Pacific used several techniques including embedding thin brick into its Infinite Facade prefabricated envelope solution. To provide a lighter-hued contrast to the masonry portions, an unadorned facade with an unfinished concrete skin was used for certain areas of the building exterior.
“I absolutely loved this job because we used a lot of different materials but we still prefabricated the majority of the project,” said Doug Bevier, associate director of preconstruction for Clark Pacific. “This is an example of how to pre-manufacture wall assemblies with a look and feel of traditional masonry, like something that's been around for a hundred years.”
Of course, not every owner wants their building to look like a historic landmark. In San Francisco, where Clark Pacific is providing precast facade for three of the four buildings in the $2.5B Mission Rock mixed-use development, it worked with noted architects to design panels that will achieve a modern facade look for several of the high-rise buildings. But it kept the panels’ manufacturability in mind, too.
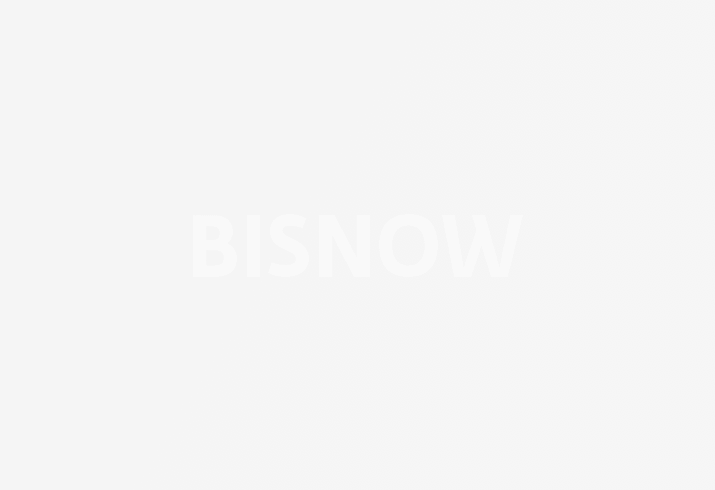
Mission Rock Building G has a facade with a high window-to-wall ratio of about 70% glass to 30% precast. Bevier said the “mega-panels” the company fabricated were approximately 16 feet tall by 30 feet wide while allowing it to meet the buildings’ design requirements.
Although very different in appearance, 2100 Kettner and Mission Rock demonstrate the versatility of prefabrication that is made possible when Clark Pacific works closely with design and construction teams, Bevier said.
“For Mission Rock, that close coordination allowed us to take a high-profile project and deliver on the aesthetics, while wrapping up the job quickly in an area of San Francisco where you don’t have a lot of space and logistics can be a nightmare,” he said.
Bevier said his company’s work at Mission Rock demonstrated a couple of other benefits of prefabrication, too.
For one, those “mega-panels” were manufactured off-site and delivered to the job site ready to be installed. That significantly reduced the amount of set-up and storage space that would have been required at Mission Rock if another construction method had been used.
It also reduced the number of people needed on the busy site, reducing both cost and risk for the owner.
“Once the fabricated panels are in the field, it takes a crew of six people to erect them,” Bevier said. “This is extremely different from a curtain wall, metal fab or stick-built construction, where you’re going to need a lot more people. There’s not a ton of space in a lot of the urban areas where we work and prefabrication doesn’t require you to stack people on top of one another to get the job done.”
Bevier said another benefit of prefabrication is the quality control that factory manufacturing allows compared to working on an exposed job site. While customizable, the panels are built to meet preset performance standards accounting for factors such as providing a barrier against water intrusion and fire resistance. The result is that the owners will know exactly what they are getting when the components arrive on-site.
“It allows for much faster on-site installation,” he said. “We can hang 5K to 6K SF of facade a day with only a small team on the job site.”
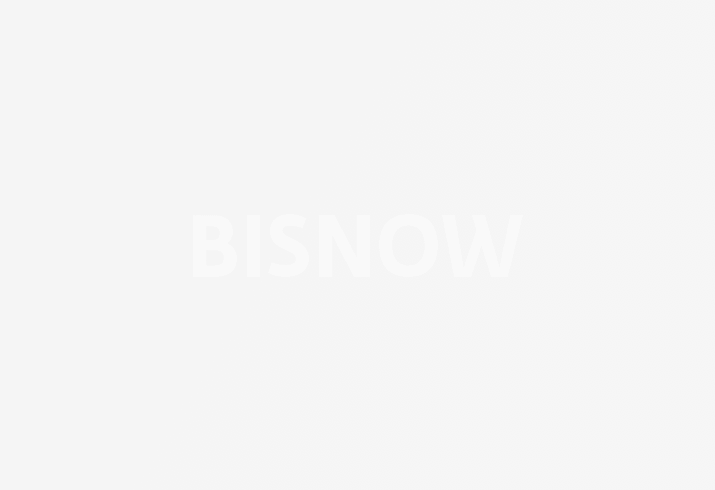
When the Clark Pacific team is closely tied into the project from the beginning, it can adjust quickly to design changes and other surprises, Bevier said. In addition, the project owner knows who to go to should any problems arise during or after installation.
“We are a single source of responsibility for the facade and owners like that,” he said.
Bevier said a recent project that took advantage of many of the benefits of prefabrication was San Francisco’s new citizenM Hotel. The 195-room, 13-story structure’s exterior panels combine concrete stained to look like metal with stone for a modern look.
As with 2100 Kettner and the Mission Rock buildings, people might be surprised to learn that its facade was entirely prefabricated.
“The citizenM project was a perfect example of what you can do with prefabrication,” Bevier said. “CitizenM used a metal panel stain and replicated stone finish. To me, it’s one of the most gorgeous buildings we’ve put up.”
This article was produced in collaboration between Clark Pacific and Studio B. Bisnow news staff was not involved in the production of this content.
Studio B is Bisnow’s in-house content and design studio. To learn more about how Studio B can help your team, reach out to studio@bisnow.com.