What's Shaking? Hopefully, It's Not Your Life Sciences Lab Space
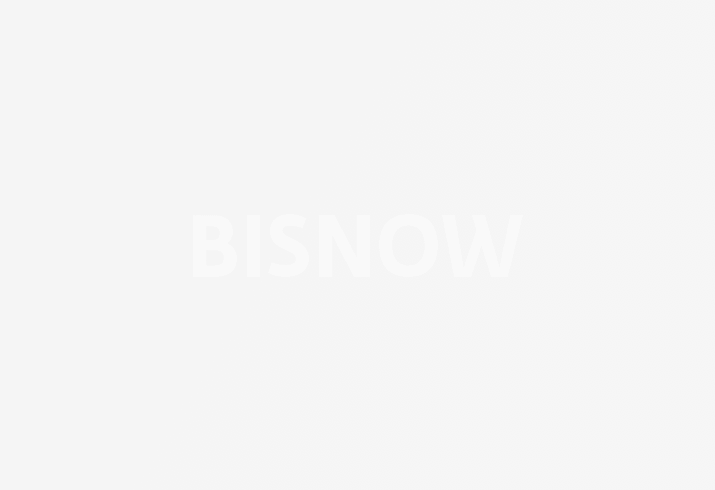
A laboratory space must meet certain criteria before a biotechnology company will even consider signing a lease. These include proximity to a STEM-educated workforce and reliable access to utilities such as water and electricity.
But increasingly, any discussion of potential lab space also needs to take into account its flexibility and resistance to vibration.
Flexibility in this sense refers to how easily a lab’s design and floor plate can be customized or expanded to accommodate a lab user’s fast-changing needs. It ranks among the top five real estate priorities of life sciences lab operators, according to one study. Separately, JLL called flexible lab space a much-needed “catalyst of success” in the ongoing development of new medicines and treatments.
“The biotech market is very fast-moving, very dynamic,” said Blake Roskelley, a senior engineer who has led the development of the new Lab Solutions product for prefabricated building systems manufacturer Clark Pacific.
He said this is a sector where a new research and development breakthrough can lead to a rapid increase in funding and expand a company’s lab space needs almost overnight.
“There's a lot of new occupancies, changes and acquisitions in this market,” Roskelley said. “The flexibility of the product has to be able to accommodate frequent changes.”
Prefabricated laboratories are a solution to this challenge, Roskelley said. Manufactured off-site using low-carbon concrete, they are built to accommodate a wide range of lab users’ needs.
They are also easily modified after installation, allowing the tenant to add new equipment or expand the overall workspace as its business grows.
“We offer a floor system that can be penetrated with openings of up to 24 inches wide, anywhere in the floor, to allow for tenant improvements and future changes in the building,” he said. “It can even accommodate the installation of interconnecting stairs between floors without the need for reinforcement or additional framing around the opening.”
The end user isn’t the only beneficiary of flexible floor plans. Roskelley said many developers in the life sciences space build their properties on a spec basis. This means their buildings must be able to accommodate a variety of use scenarios for current or future tenants.
“Builders of spec labs can go through the design process without knowing who exactly is going to be using the space and how,” he said. “The flexibility of the structural system is paramount. These types of developments are meant to accommodate multiple tenants, and you could have a multitenant floor, too, all of them with varying needs.”
Roskelley noted that Clark Pacific’s Lab Solutions product addresses another issue of vital importance for biotech companies.
Lab operations use extremely sensitive equipment such as electron microscopes whose efficacy can be impacted by the slightest vibration, even one created by people’s footfalls as they move around the building.
“Even if humans can’t perceive the vibration, at the super-high, zoomed-in resolution of an electron microscope, even slight vibrations can negatively impact outcomes,” he said. “This means labs have to have really stiff floors.”
Roskelley said Clark Pacific’s prefabricated spaces can protect lab activity from subtle vibrations of between 2,000 and 4,000 micro-inches per second. This is not achievable with a steel-supported floor unless the builder installs “significantly” more steel to increase the structure’s stiffness, which may add to its cost, he said.
Using Clark Pacific’s reinforced concrete product instead of steel beam construction also allows for the creation of larger rooms that are uninterrupted by vertical support columns.
“A long steel beam is going to want to deflect or bend,” Roskelley said. “To limit vibration to an acceptable level, steel spans must be reduced and steel beam sizes increased, resulting in heavier, more costly framing and column-encumbered spaces that can increase costs and get in the way of lab operations. Clark Pacific's prefabricated solution, on the other hand, give additional flexibility to the architect to design spaces that will meet their users’ needs without compromising.”
With Clark Pacific’s prefabricated floor framing system, floor spans can reach 44 feet with as much as 33 feet between columns, allowing floor plates of up to 40K SF. Ceiling height can reach 16 feet on upper floors, and as much as 20 feet on the first floor.
A laboratory’s unique needs mean that Lab Solutions does not incorporate the thermally active concrete floors of Clark Pacific’s NetZERO building platform. However, radiant floors can be integrated into floor plates for known areas of office occupancy or installed throughout so that lab space can be converted later to NetZERO office space depending on a tenant’s future needs.
“Prefabricated structural system products have a lot of inherent flexibility to accommodate future uses by tenants,” Roskelley said. “This allows developers and life sciences companies to adapt much more quickly to changing business demands.”
This article was produced in collaboration between Studio B and Clark Pacific. Bisnow news staff was not involved in the production of this content.
Studio B is Bisnow’s in-house content and design studio. To learn more about how Studio B can help your team, reach out to studio@bisnow.com.