After 3 Major Failures, Does UK Modular Housebuilding Have A Future?
Modular housebuilding was supposed to be the clean, green, fast and friendly solution to the UK's housing supply problem. Yet one by one, the UK's pioneer modular housebuilders are falling by the wayside.
Ilke has become the latest to hit trouble, suspending production at its Yorkshire factory as it searches for a buyer willing to rescue it from a possible administration. Earlier this summer, Legal & General paused its ambitious modular housing operation, whilst Urban Splash House collapsed into administration in May 2022, owing about £20M.
For at least a decade, modular housebuilding has been heavily advocated by the housing sector and the UK government as a way of getting more houses built more quickly, but three such high-profile failures suggest a bleak future for modular housebuilding.
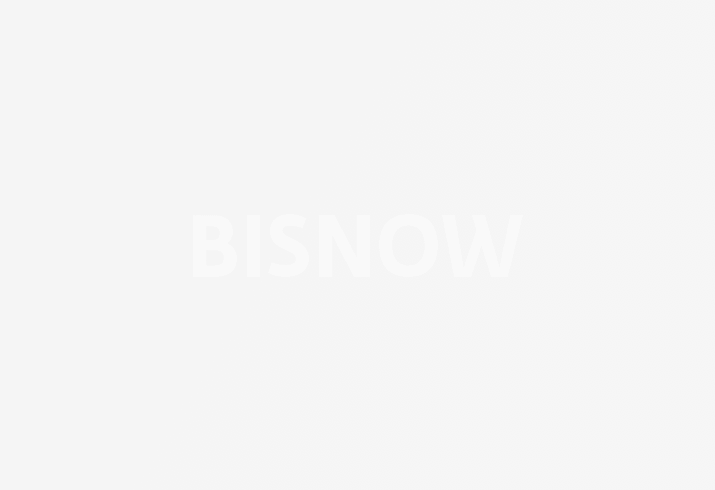
While the sector is not dead, it needs to find a way of overcoming a Catch-22 that has beset many startup sectors: It's not profitable if it can't scale, but it can't scale if it's not profitable.
Ilke suspended production, blaming fundraising and housing delivery issues and macroeconomic conditions. The firm — owned by Sun Capital, Fortress Investments and TDR Capital — said it had a 4,200-home pipeline and a £1B order book, mostly for affordable housing.
However, the most recent accounts showed a pre-tax loss of £34M against a turnover of £12.7M, and there has been a long-term record of losses, The Construction Index reported.
The common factor in all three business traumas is the simple problem that modular housing factories are only efficient and viable if they have steady demand and, therefore, a constant output of housing units.
“Without the necessary scale of pipeline, it is not sustainable to continue producing more modules,” Bill Hughes, chair of Legal & General Modular Homes, said in May 2023 of his decision to close a factory.
The manufacturing plant had been intended to produce 3,000 units or more each year, but output only reached 450 annually. The entire modular sector produced 3,300 units in 2022, according to industry body Make UK Modular.
Without reliable, long-term customers to keep the factories working, modular faces a challenge. There are also questions over the quality control of output from modular factories, plus the knottier problem that modular housing is difficult to convert, extend or personalise, and nobody knows how well these buildings will age.
The inherently standardised and inflexible nature of modular construction is also a problem in a world that demands flexibility and variety.
“The unreliability of the planning system means their factories, which produce a small range of standard product, haven’t had the flexibility to be used to full capacity,” said Edward Architecture Managing Director Graham Edward, a specialist in modular projects.
The spate of failures shouldn't be surprising, according to Nick Whitten, JLL head of EMEA and UK living and residential research. Business startups are always fragile, and most don't make it, especially in the construction sector.
"The modular building industry in the UK is still so nascent and effectively consists of a set of startup businesses," Whitten said. "Innovation is really hard in business, and about 60% of UK startups fail within the first three years. This is in line with global averages."
On top of this, the small and medium-sized enterprise housebuilding sector typically bears the brunt of the pain during periods of economic turbulence, Whitten said, and the same is clearly happening again.
"Construction starts are down by around 20% and housing transactions are down 30% as a result of all the inflationary-driven headwinds facing the industry," he said. "Modular builders need certainty of workflow. It is very difficult to dial up and down a conveyor belt approach to housing delivery."
This approach is shared by a remaining modular housebuilder with serious ambition: TopHat, the Goldman Sachs-backed modular operation, is aiming for 3,500 units a year by 2025.
"Modular homebuilding is still a growing and fast-changing industry which creates both challenges and opportunities," TopHat founder and chief executive Jordan Rosenhaus said. "As with other evolving sectors, different companies have adopted distinct business models. Inevitably, some will fail, but others will benefit from the immense possibilities that exist. The world needs more homes and new ways of delivering them. TopHat will be one of the companies that capitalizes on this opportunity.”
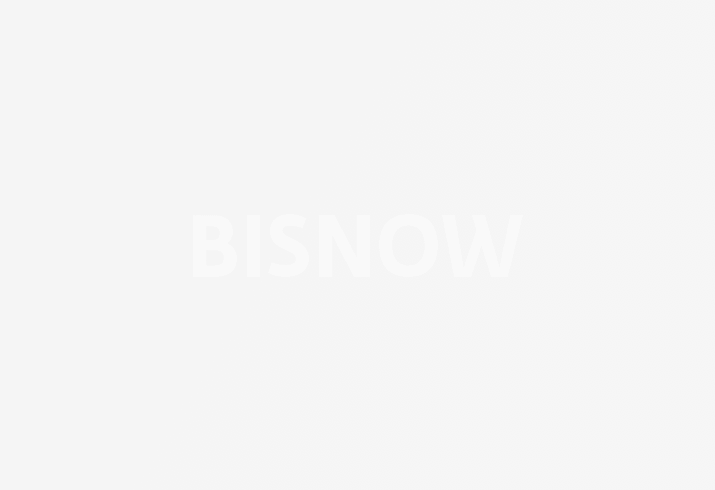
In spite of the high-profile failures, modular construction still has advocates who argue that the sector can fly if it can overcome an initial hump.
“Modular building has gained immense popularity, not just for its cost savings but also for its ability to reduce construction time and elevate quality control measures,” Symmetrys Associate Director Ashwin Halaria said.
The structural and civil engineering practice has a strong record in demountable structures.
“Despite the challenges it faces, it is still a practical approach," he said. "To overcome the obstacle of limited volume, developers, architects and engineers must be aware of the advantages and optimise building design accordingly. Boosting feasibility requires expanding manufacturing capacity, providing regulatory support and educating stakeholders.”
Mike De’Ath is partner at architect HTA Design, the firm behind the world’s tallest modular residential scheme, Greystar's 44-storey Ten Degrees in Croydon.
“The first modular housebuilders have been pioneers, and so they got some arrows shot into them,” De'Ath said. “Innovation is difficult because the housing market is broken, so enthusiasm has been frustrated. The government needs to listen to modular housebuilders to learn what they need, especially on end-to-end delivery, because modular means 40% less carbon and twice the productivity of traditional building methods.”
The hope in the UK property industry is that government thinks modular's speed of delivery and potential environmental, social and corporate governance wins are sufficiently impressive to reconfigure the housing market in a way that gifts it a commercial future.
“Volume is certainly key when it comes to the rollout of modular housing with bulk sales — single and multifamily housing and affordable housing at present driving the only volume delivery in the off-site construction market,” BNP Paribas Real Estate Head of Development and Planning Tom Stanley said.
“A major driver for increased volume will be the ESG benefits that come with sustainable methods of construction and build quality," he said. "Both planning policy and regulatory systems need to catch up with this design aspiration whilst the volume demand in the market isn’t quite there to sustain its delivery.”