Construction’s Woes Start To Hit This Surging Real Estate Sector
The U.S. construction industry is sputtering as rising prices for materials and a deeply disrupted global supply chain continue to wreak havoc on building costs and construction timelines.
These problems are straining developers and contractors to the point that in the white-hot industrial sector, some players are reconsidering the practicability of breaking ground on a new project.
Others are just pushing projects further down the road until pricing and access stabilize.
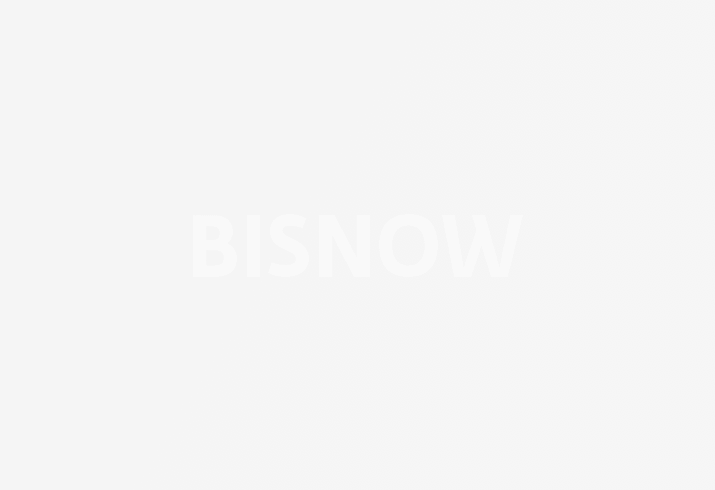
During the first few months of the coronavirus pandemic, U.S. manufacturers of steel, lumber and other materials were forced to idle some of their domestic production, as construction projects around the country slowed or came to a halt. Lockdowns forced some factories and plants to close for weeks, while others furloughed their workers.
At the same time, the global supply chain suffered a massive disruption.
Chinese manufacturing lagged first, cutting off access to certain goods and materials for several months. But now that manufacturing has resumed, most U.S. ports face a bottleneck of backed-up container ships, which continues to limit the availability of materials.
In nearly 20 years of working for the Associated General Contractors of America, chief economist Ken Simonson said he has never heard of so many materials rising in price so quickly and steeply — or seen such extreme lead times for delivery and the rationing of materials.
“Materials costs have been shooting up at unprecedented rates ... Specifically, lumber and steel prices have reached record highs,” Simonson said.
Between April 2020 and February 2021, prices for steel mill products jumped by 20%, according to producer price index data from the U.S. Bureau of Labor Statistics. Copper and brass mill shapes rose by 37%, lumber and plywood prices rose by 62%, and diesel fuel rose by 114%.
Simonson noted that diesel fuel prices have fallen in the last few weeks, while copper prices have also backed down over the last two months. However, both remain much higher than a year ago, and the situation remains very difficult for accessing plastics and other petrochemical-based materials that are commonly used in construction.
In mid-February, a snow and ice storm pummeled Texas and delivered multiple days of below-freezing temperatures across the state. The storm had a major impact on the Gulf Coast, where most of the country’s plastics are produced. Widespread loss of power, production shutdowns and damage caused by the freeze have been challenging for producers, who are still trying to get production back up to speed.
“Many, many producers of construction plastics or the materials that go into them have declared force majeure, and they're not able to deliver product on time, they're raising prices or prices are being bid up for what is available,” Simonson said.
Arch-Con Corp. President Jason Cooper said that the rising cost of materials like steel, lumber and cold form steel are causing anxiety among contractors and developers. He told Bisnow that now, lumber has more than doubled in cost since last April, causing developers to re-evaluate wood-constructed developments.
Similarly, Cooper said that steel prices have increased by 40% since mid-October, which is placing pressure on construction starts.
“This steel price increase is not canceling jobs, but it may delay the kickoff of a speculative development,” Cooper said.
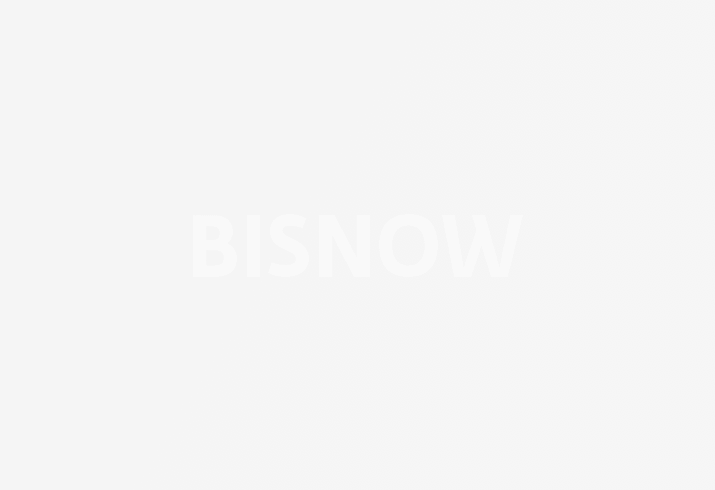
Powers Brown Architecture principal Nazir Khalfe said there has been a lot of discussion around industrial projects being delayed because of the inflated costs, but general contractors working with his firm have expressed optimism that soaring prices could soon plateau.
However, Simonson said the sector could still be facing elevated prices for several more months before prices start to come down.
“I won't predict that any of these will keep going up at the rate that they have been, but it could be late this year before we start to see general relief on the prices,” Simonson said.
In an AGC survey conducted between Feb. 19 and March 4, the organization found that 77% of the 1,489 respondents have had projects that were indefinitely postponed or canceled. About 40% said their projects were postponed or canceled in 2020, while 17% had a project halted that was supposed to move forward between January and June this year.
Aside from skyrocketing construction material prices, lengthening delivery times across the U.S. are wreaking havoc on projects. Khalfe said that in particular, the lead time for delivery of steel bar joists and steel decking is causing significant problems.
“If delivery times are being quoted towards the latter part of the year, it is making developers think twice as far as construction scheduling goes,” Khalfe said.
Cooper agreed that steel joists and decking are posing some of the biggest challenges, and noted that delivery times from the two major U.S. manufacturers of those items have extended out to 24 weeks. Normally, delivery times range between eight and 12 weeks.
“On smaller warehouses, retail and office building projects, this time frame is a no-go as the steel is bought in a normal sequence and would not fit the swift project schedule,” Cooper said.
Despite having conversations with clients to release the structural steel early, in some cases the materials are still not arriving in typical sequence, ultimately disrupting the entire timeline of the project.
Cooper said the situation has become so difficult that in some cases, Arch-Con has recommended delaying the start of projects to allow for the normal sequence of steel. Larger projects have more room for flexibility, and the firm has been able to resequence the construction of those projects to accommodate the delays.
Duke Realty Corp. Senior Vice President Stephanie Rodriguez said that when the pandemic first began, most of the sector hit pause on speculative industrial developments, to ensure that balance sheets remained in check. When demand remained strong, especially for logistics facilities, construction of spec development started up again.
Delayed deliveries have negatively impacted construction schedules across the U.S., but Rodriguez said that despite the challenges, Duke Realty Corp. hasn’t been forced to hold off on any projects. The industrial REIT tends to specialize in larger facilities that cater to e-commerce and supply chain users, two sectors that have been in extremely high demand since the onset of the pandemic.
“I haven’t seen 12-to-24-month delays. However, we are seeing longer lead times for steel,” Rodriguez said.
Rodriguez noted that on build-to-suit projects, Duke Realty Corp. tries to get ahead of steel orders, sometimes even prior to lease execution. That has allowed the firm to accommodate schedule changes due to material availability.
Unlike Cooper, Rodriguez said that she hasn’t heard of anybody in the industry deciding to delay an industrial construction project because of material delivery problems.
“We know that projects may have to slide a bit and it’s something that everyone in the industry is dealing with. So, there really isn’t anxiety — just something we all know that we have prepare for,” Rodriguez said.
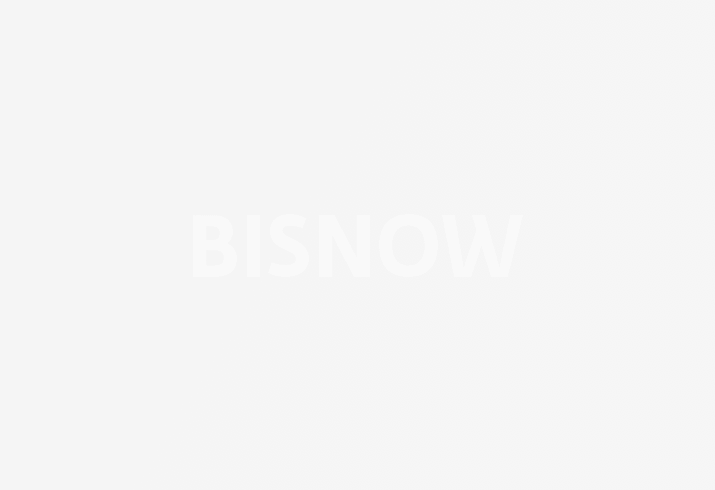
Aside from high materials prices and delivery delays, there’s another challenge facing the construction sector: staffing.
The U.S. construction industry will need at least 430,000 more workers this year than it did in 2020, according to an Associated Builders and Contractors analysis of U.S. Census Bureau data and a forecast by economic consulting firm Markstein Advisors. If construction spending accelerates at a higher growth rate, that figure could be closer to 1 million.
All these issues point to ongoing pressure that could result in more projects postponed or canceled, though demand for certain product types, like e-commerce and logistics facilities, is likely to keep bigger projects moving ahead.
As for the challenge of accessing construction materials, Simonson said that there is enough global capacity to produce most items. The challenge is repairing and improving the supply chain to ensure that everybody can access them.
“It’s much more a question of logistics, of having the personnel and also being able to get things delivered, whether it's from a domestic source or brought ashore and moved through ports and to the destination,” Simonson said.
CORRECTION, APRIL 9, 1:15 P.M. CT: A previous version of this story contained an incorrect figure regarding the wait time for steel joists and decking. The story has been updated.