Three Ways to Keep Construction Costs Down
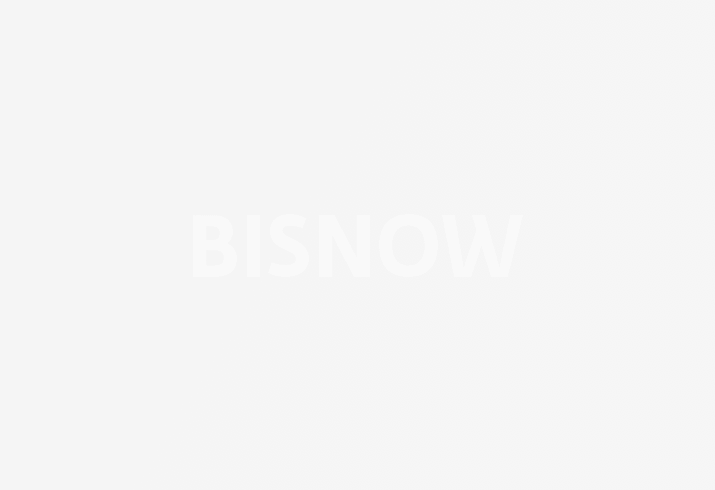
Gone (for the most part) are the days of designing a project, then finding a contractor and negotiating how to keep a project under budget. Today, the buzz phrase is integrated team approach. Callaway Architecture CEO Tony Callaway says it’s been the biggest change in the way construction is done. He’s a fan of design-build and getting contractors involved early in the design process. It minimizes change orders and helps keep those tight schedules (and budgets) on target. He says the best way to keep costs down is a three-fold approach by doing your homework early on the budget, scope and quality of a project.
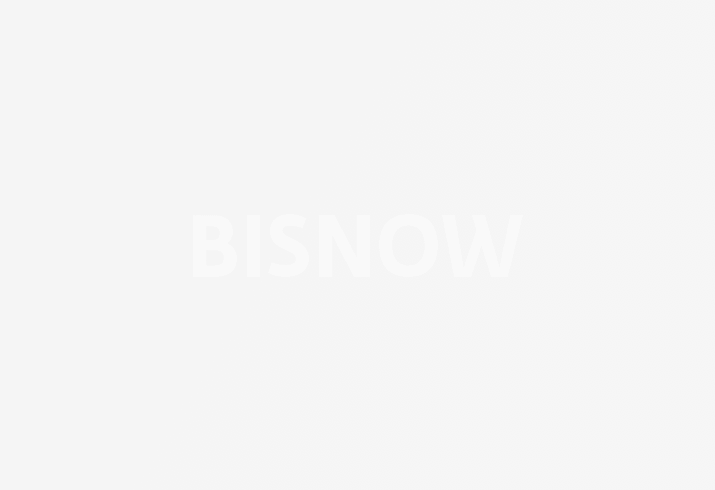
Determine two of those three and the third is established. Identifying the scope of the project from size and goals and then identifying the budget determines the quality of the finishes. By establishing those three things up front, the architect can make better decisions on costs in line with the client's vision. Tony was among a panel of construction experts speaking at Bisnow’s Construction and Development event Tuesday. The panel: Tony, WoodWorks regional director Robbie Kelley, GL Seaman & Co DIRTT champion Mary Miano, VCC Construction SVP Derek Alley and AOS Engineering partner Shane Arrant. Shane agrees that teamwork is the best way to keep costs down. When he’s brought in early, he can help get quotes on costs and open the line of communication with vendors, too. It’s also better to know if the owner is looking for upfront costs savings on the building or looking for annual efficiencies.
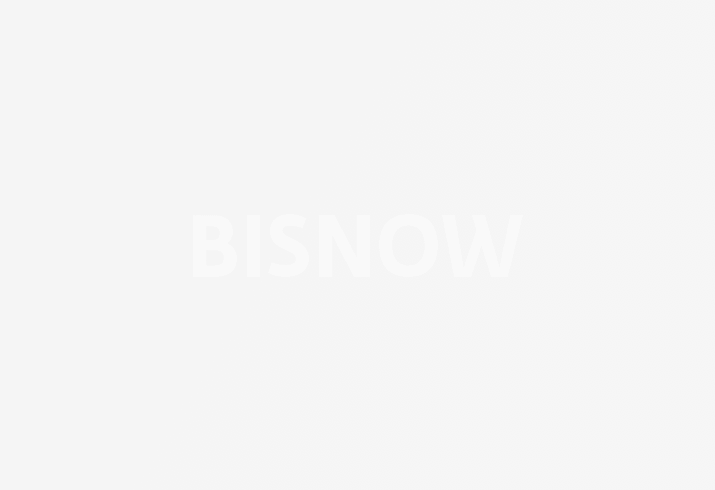
Derek (left, with Slate Harwell’s Gene Blanton) says projects are moving more quickly today with compressed time schedules and a speed to market goal. Especially in Dallas, opening before a competitor benefits lease-up significantly. Because of that, teamwork early on is crucial. Additionally, there’s a variety of challenges from staying on top of new technology and construction materials that can keep costs down to a shortage of skilled laborers. Without pre-planning, you’re courting disaster, he says.
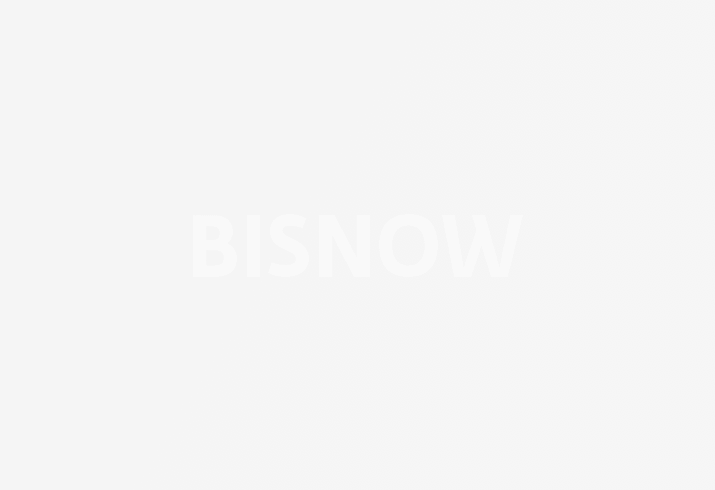
Mary (center, between Curtis Group Architects’ Katie Keyworth and James Spencer) says most large projects use an integrated approach because it’s the best opportunity to engineer value from a scheduling standpoint without compromising design. In some instances with ground-up construction, cost overruns lend to cutting costs on the interior. GLSC uses virtual reality technology to assist with decision-making and see how modular interiors can add value to a project.
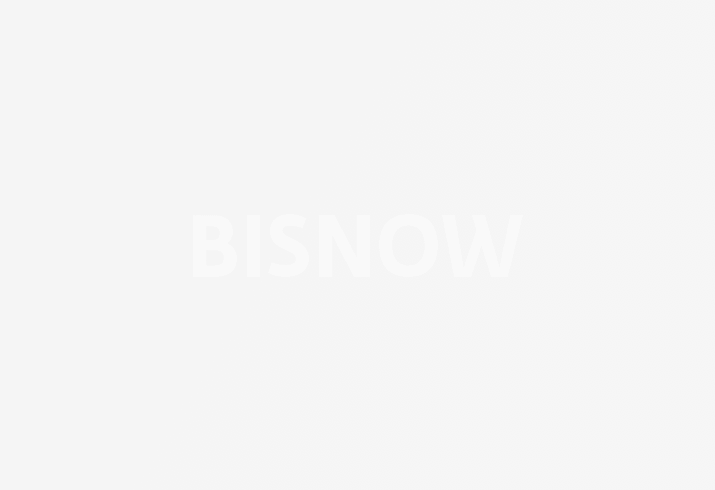
Robbie says the nonprofit strives to educate the public on the use of wood in relation to commercial construction. He said the org’s advice and assistance is free. From a structural standpoint, he says using wood can save anywhere from $10 to $15/SF. He also encourages researching cross laminated timber, which is being used in other countries like Canada to build sounder, taller buildings. There are some 18-story projects that are 100% wood. It allows developers to build taller for less and it will be happening here in the next three to five years, Robbie says.