From Cubicles To Cancer Treatment: Converting Office Spaces Into In-Demand Healthcare Facilities
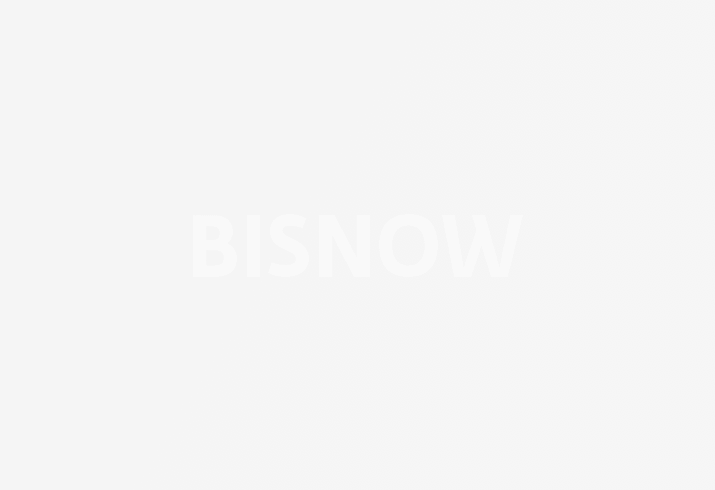
As offices across the country continue to experience high vacancy rates, owners and developers see an opportunity to solve another challenge: the demand for more healthcare facilities in the U.S.
Hospitals are struggling to find space to care for the influx of patients they have experienced since the pandemic began, with hospital bed occupancy nationwide above 70% every week since at least October 2022. To help solve this problem, developers have been transforming office space into healthcare facilities. But what makes an office building a good candidate for this type of conversion?
“It’s all about ease of access,” said Mary Kate Knightly, senior project manager at Chicago-based Leopardo Construction. “The location needs ample parking and to be positioned near both residential and commercial areas and the amenities they offer.”
Leopardo Vice President of Healthcare David Rutledge said when developers are looking to build a new healthcare facility from the ground up, they often find that ideal sites like Knightly described are few and far between. Converting existing office buildings into healthcare facilities, however, provides a prime location, accelerated timeline and cost-effective strategy.
Of course, these conversion projects don’t come without significant challenges. When transforming an office into a healthcare facility, the building will likely need new utility services, mechanical, electrical and plumbing infrastructure, and vertical transportation modifications, at a minimum. How quickly and easily these changes can be made depends on the existing structure of the building.
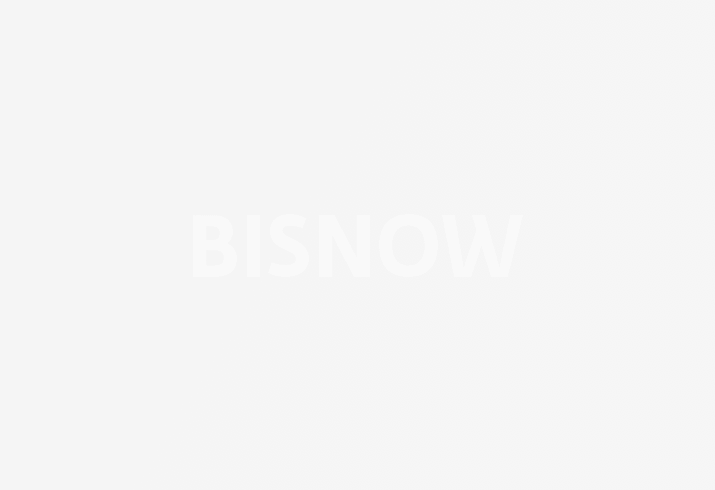
“An office conversion we previously completed had a core structure consisting of hollow core concrete planks, requiring very specific areas where we could and couldn’t penetrate,” Rutledge said. “This posed a challenge for all the plumbing that goes along with healthcare facilities. Utilizing existing precast shop drawings and CAD-based layout tools, we were able to spot the plumbing cores with little floor plan disruption. The core structure is the one thing you can’t change in an adaptive reuse project, so you need to find solutions and work around it.”
One thing driving the electrical and design needs of a healthcare facility is the diagnostic and treatment equipment, which requires a great deal of space and electricity to operate.
Rutledge specifically mentioned linac vaults, linear particle accelerators that are used to provide radiation treatments for patients with cancer. The Leopardo team installed a linac vault, along with performing several other diagnostic imaging build-outs, in the Rush Cancer Center at Lisle in Lisle, Illinois, a 55K SF renovation that transformed an office building into a modern cancer facility.
Knightly said a critical aspect of the Rush Lisle project was the post-demolition laser scan the team performed to validate the architect’s planned layout and confirm where all MEP systems, stairways and other core features were located. She explained that often, these scans reveal things that lead to changes in the floor plate design, which was true for this particular project, as its built conditions differed from the original design drawings.
“We were able to coordinate the design to the layout we saw in the scan,” she said. “We coordinated around existing fire protection systems and quickly and easily determined where systems needed to be replaced and which could be reused.”
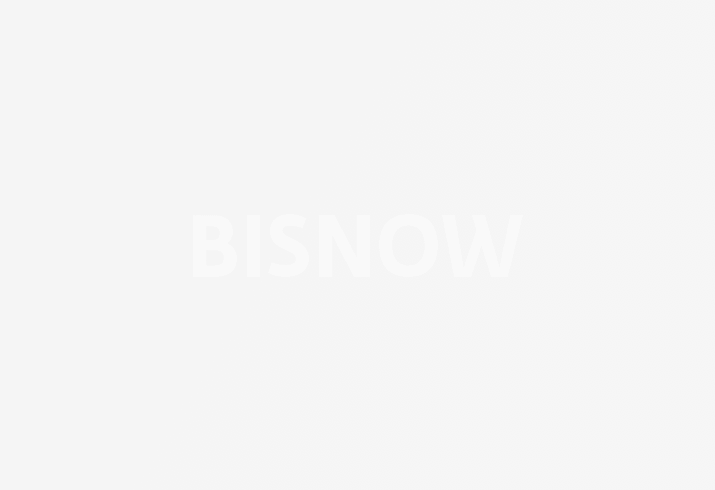
Rutledge said that since offices typically have smaller floor decks than healthcare facilities, it is especially important to perform this type of scan to document the existing structure and map out a plan to install new equipment, since healthcare facilities consist of more complicated systems and denser floor plans to function.
The Leopardo team is also integrating a new exterior system into the Rush Lisle space, including installing new metal panels, staining granite from an existing pink color to a more Rush-style gray, and putting in a new curtain wall system.
“The plan early on was to reuse as much of the existing building as possible,” Rutledge said. “So the question becomes: How do you make the exterior skin look like an inviting space for patient care, matching a brand, while reusing as much of the existing as possible? We have managed to reuse quite a bit, which is better for the environment from a sustainability standpoint and the project overall.”
Knightly said for typical ground-up projects, there is more time to wait for materials with long lead times to come in due to the many different construction phases. But that isn't the case with retrofit projects like Rush Lisle.
Leopardo utilized its own procurement team to purchase the rooftop units and the electrical gear needed right away, giving them plenty of time to arrive within the project schedule. This kept things moving, avoiding costly delays.
The result has been that Rush is able to more quickly bring its world-class healthcare facility to a suburban area that needs it, she said.
“When city health systems are able to migrate to the suburbs, it makes a significant positive impact on the community,” Knightly said. “We’re proud to make healthcare more accessible.”
This article was produced in collaboration between Studio B and Leopardo. Bisnow news staff was not involved in the production of this content.
Studio B is Bisnow’s in-house content and design studio. To learn more about how Studio B can help your team, reach out to studio@bisnow.com.