Baltimore Hopes To Capture More High-Tech Manufacturing To Revive Its Industrial Past
The days of tens of thousands of Baltimore-area residents working at steel mills likely aren't returning, but industrial real estate experts say emerging types of manufacturing can still play a central role in the region's economy.
Advanced manufacturing facilities that require highly trained employees and pay solid wages hold untapped potential to generate jobs in the Baltimore region. But the ambitions to expand the industry and once again make Baltimore synonymous with manufacturing still need to overcome substantial obstacles.
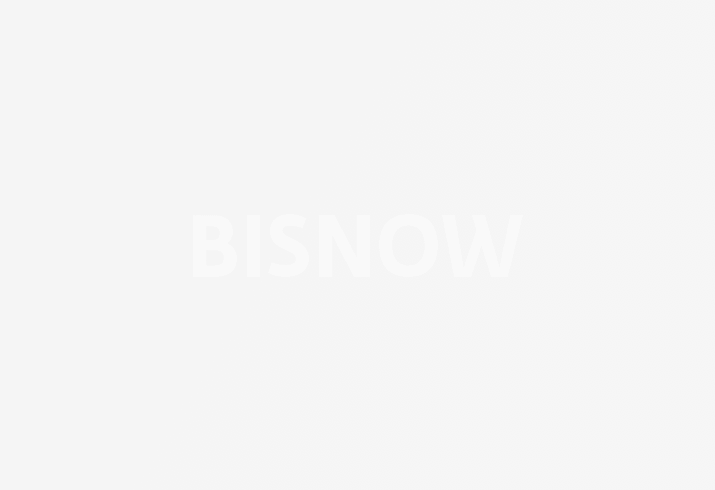
Baltimore has a large inventory of manufacturing space with about 27M SF across the region, according to a first-quarter report from JLL, but it lacks new space available for manufacturers to open operations. The report found that zero manufacturing facilities were under construction or delivered during the quarter in the Baltimore region.
The warehouse and distribution segment of the Baltimore industrial sector, however, had 2.4M SF deliver in the quarter and another 2.8M SF under construction. That segment makes up 85% of the region's overall industrial inventory.
"We are missing an opportunity by not investing in the wealth produced by employers and workers when we don’t allocate space for manufacturing, compared to warehouse or distribution," Regional Manufacturing Institute of Maryland President Mike Galiazzo said.
Manufacturing is experiencing a comeback in many parts of the country. Spurred by an influx of federal funding, along with the growth of the electric vehicle market and other tech sectors, companies are developing major factories across the country to build EVs, batteries, semiconductor chips and other technologies.
Galiazzo said Maryland should lean further into the high-tech manufacturing sector to capture some of this demand.
"We will never be where [manufacturing] was. But it can be where it should be, which is a highly technical, highly skilled workforce that will again adopt and adapt new technologies that allow us to compete globally," Galiazzo said.
"When we lost our manufacturing base, we basically lost avenues of opportunity for people to enjoy middle-class living. With the new technologies that are out there, we can re-establish a global competitiveness that has been missing in America for several decades now."
In pushing for a new future for manufacturing in the Baltimore region, supporters also seek to preserve an essential part of the area's identity and heritage that stretches back to Maryland's colonial era, when industries like shipbuilding and ironmaking in river valleys west of the city emerged.
The true roots of industrialization in the region, according to Henry K. Sharp's book America's First Factory Town: The Industrial Revolution in Maryland's Patapsco River Valley, didn't take hold until the mid-18th century when Maryland farmers shifted their focus to wheat production, which required mills for processing and easy access to Baltimore's port.
However, the real spark for the local industrial revolution came in 1827, when a group of financiers and businessmen chartered the Baltimore and Ohio Railroad. The construction of the B&O Railroad, the nation's first "common carrier" railroad, spurred Baltimore's first wave of industrial manufacturing.
"In Baltimore, numerous industries opened up around the tracks," according to Preservation Maryland. "Construction shops for steam engines, repair sites, iron works, blacksmiths, sawmills — all appeared in railroad towns. With the opening of these businesses came more job opportunities for many Marylanders."
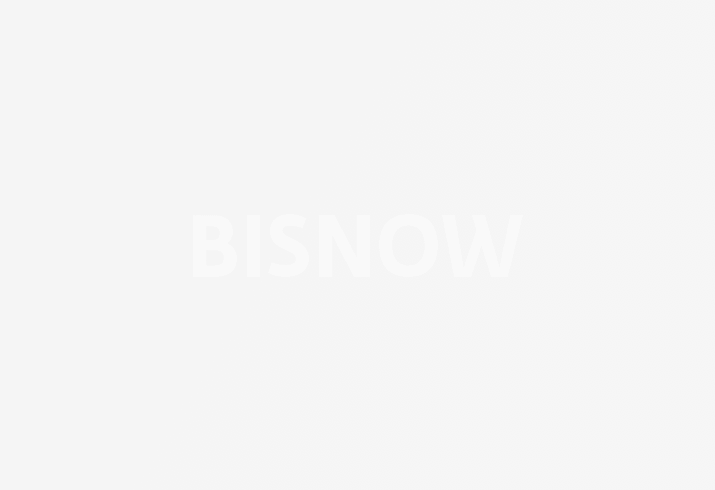
The two world wars brought big steps forward for Baltimore's manufacturing industry in the 1910s and 1940s, as the region developed steel facilities, oil refineries, shipbuilding, aircraft manufacturing and other war-related industries.
In the years following World War II, automobile manufacturing at General Motors' Broening Highway Assembly Plant and steel manufacturing at Bethlehem Steel's Sparrows Point plant cemented the Baltimore area's reputation as an industrial manufacturing hub.
The steel mill at Sparrows Point served as a symbol of the Baltimore area's manufacturing vigor as it grew to the world's largest steelmaking site by the 1960s. But by then, the region's industrial sector already showed cracks in the foundation.
Between 1950 and 1995, the Baltimore region lost more than 100,000 manufacturing jobs, roughly 75% of its industrial employment, according to the State of Urban Manufacturing report released by the Urban Manufacturing Alliance in 2018.
While manufacturing declined in the second half of the 20th century, it hasn't disappeared from Baltimore.
Today, it still ranks among the five most prominent industries in Maryland in terms of gross domestic product, according to 2021 figures from the Bureau of Economic Analysis.
Anne Arundel County, Baltimore County and Baltimore are home to the state’s largest concentration of manufacturers, Galiazzo said. He estimated as much as 45% of the state's manufacturing businesses call the Baltimore metro home.
"You have a wide variety of manufacturing types in the state of Maryland, but also in the Baltimore region in particular," he said. "A lot of people don't realize that manufacturing includes everything from cardboard and paper products to printing products to electronics, metals to fabrication. It's really a variety of products that come out of manufacturing."
Yet if the local manufacturing sector is to ever unlock its full potential, it must overcome numerous obstacles.
The Urban Manufacturing Alliance spelled out those obstacles in its 2018 report, identifying seven issues that are restricting the growth of manufacturing in Baltimore.
According to the report, smaller manufacturers faced the most significant roadblocks to success. Specifically, these firms opined to researchers about their inability to access incentives and early stage growth capital.
Tradepoint Atlantic, the 3,300-acre multimodal transit hub built on the former Bethlehem Steel plant site in Eastern Baltimore County, is one of the sites where backers hope to see advanced manufacturing flourish.
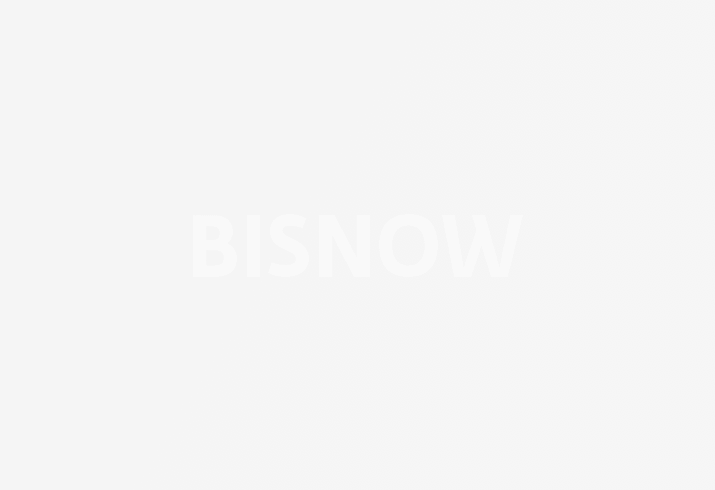
After the last remnants of steel manufacturing at the site ended in 2012, state and local officials envisioned future redevelopment of the site, including a substantial amount of manufacturing.
A task force dubbed the Sparrows Point Partnership released a plan that listed advanced manufacturing as one of the four core sectors it wanted to play a role in revitalizing Sparrows Point.
While the site has developed primarily as a distribution hub, Tradepoint Atlantic Director of Corporate Affairs Kristen King said the property is home to many manufacturing tenants.
Manufacturing tenants include companies like Niagara Bottling, Gotham Greens and Ørsted, a clean energy company that started construction on its advanced foundation component center this spring.
About 13,000 people work at the site daily, King said. While she doesn't expect Tradepoint Atlantic to match the 30,000 people who worked on the site during the steel mill's heyday, she said as many as 25,000 people may work on the site at full build-out.
The site is about 70% built with 13.5M SF of vertical development. How much of that space the developer will dedicate to advanced manufacturing is still to be determined, and the master plan for the site shifts to meet market demand.
“The master plan changes almost daily, and it does because 3,300 acres is a lot of land,” King said.