Just What The Doctors Ordered: JE Dunn Overcomes Construction Obstacles To Help Emory Scientists Solve Medical Challenges
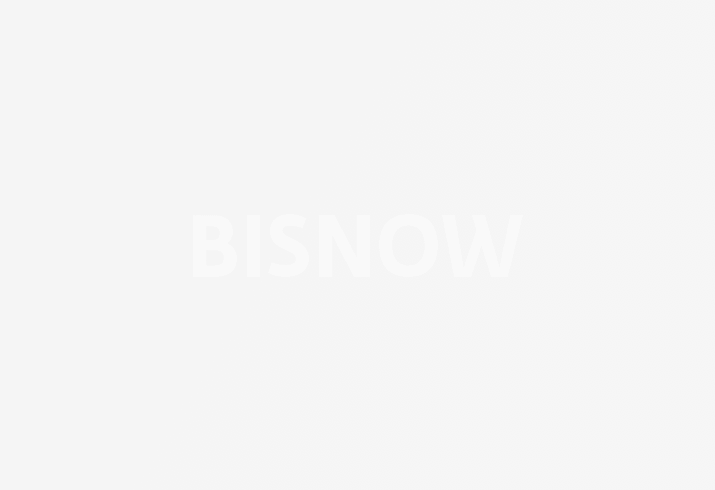
Emory University calls the newest building on its Atlanta campus a “trailblazing space” where 1,200 biomedical researchers will collaborate to find solutions to “the biggest human health problems of our time.”
The design of the 350K SF, eight-story Health Sciences Research Building II is meant to encourage creativity and collaboration among the scientists who will conduct research in disciplines like oncology, cardiology and pediatrics, according to the university.
The building’s ribbon-cutting in March will be the culmination of four years of hard work for JE Dunn Construction. In 2019, the company was tasked with solving a daunting problem: finding the most efficient construction solutions to bring the highly complex building to life on its tight footprint in a busy area.
“Most of the lab buildings I’ve built over the years have been square boxes,” JE Dunn General Superintendent Ken Cornell said. “But there is nothing typical about HSRB II.”
The biggest construction project in the history of Emory, HSRB II includes a cyclotron, magnetic resonance imaging and PET/CT imaging equipment. In addition, it houses wet and dry labs, faculty offices, formal and informal collaboration spaces, and support and conference spaces.
A soaring, skylit atrium and interactive video monitors throughout the building will help encourage idea exchanges in the new home for Emory’s Woodruff Health Sciences Center and the School of Medicine.
All of this is squeezed onto a 4-acre site that JE Dunn Project Director Christopher Rampton described as a “postage stamp on the university campus.” Its close neighbors include other university buildings, a children’s hospital, a high school and a railroad line, all of which remained active during construction.
In addition to the typical traffic on a construction site — which, in the case of HSRB II, involved deliveries of more than 6.7 million pounds of reinforcing steel, 1.1 million tons of Portuguese marble and 31,300 cubic yards of concrete — JE Dunn coordinated more than 40 blasts to prepare the rocky site for construction, with some of the explosions occurring only feet from neighboring buildings.
All of that called for frequent communication between the team led by JE Dunn and HSRB II’s neighbors.
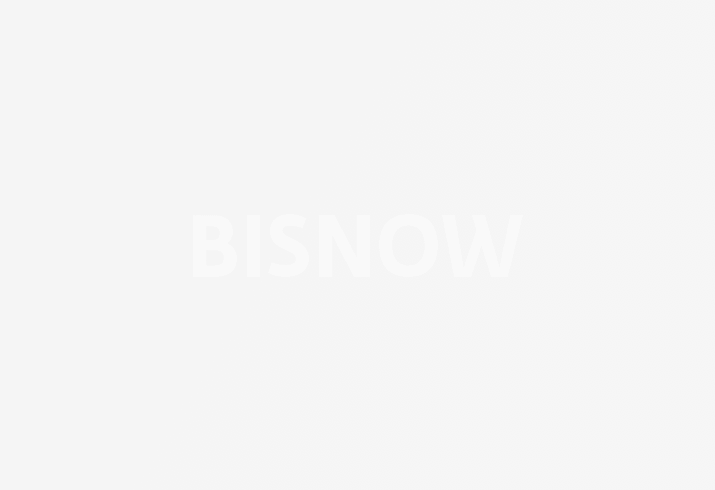
“There was a lot of coordination with not just Emory but the surrounding entities like the children's hospital right across the street,” Cornell said. “On the afternoons that we blasted, we had to shut down Haygood Drive. At the hospital, the surgeons basically put their scalpels down at 4:15, then we’d do our blast at 4:30. Once we gave them the all-clear, they went back to work.”
Along with diligently keeping its neighbors in the loop, Rampton said JE Dunn employed other tools that allowed the team to complete the biggest project ever for its Atlanta office. These included its use of proprietary estimating software, the team’s expertise in building information modeling, known as BIM, and the company’s application of lean construction principles.
Senior Project Manager Frederick Tull said JE Dunn worked closely with architect HOK and studied the building’s older neighbor, HSRB I, to advise Emory on how to budget for this new project.
In addition, JE Dunn’s Lens estimating software allowed it to continuously estimate and collaborate throughout the pre-construction phase, bringing the client real-time cost knowledge for fast decision-making, Tull said.
“As we went through the design process, Lens allowed us to communicate better about the details of the budget estimate and even see a 3D model,” Tull said. “This was a complex project to get your arms around because it was so unique, and being able to collaborate better on the details of our estimate in real time was definitely beneficial to our success.”
Rampton said JE Dunn’s BIM mastery also was critical to the project, allowing the team to schedule work and manage the installation of materials that ranged from sensitive equipment and the infrastructure needed to support it to terrazzo tile floors and a multistory hanging stairway for the lobby.
“The project would never have succeeded without the BIM coordination process,” he said. “I've never seen anything like the complexity of this job, and it took every minute of everyone's time to get to a point where we could install what was drawn with minimal conflicts.”
JE Dunn’s use of the 5S principles of lean construction was an additional key to the project's success, Cornell said. The techniques allowed the team to keep the work site organized, simplify work processes and avoid wasted efforts or materials.
“We’ve used lean techniques on past projects, but on HSRB II, we spearheaded the use of 5S, which stands for ‘sort, straighten, shine, standardize and sustain,’” he said. “Overall, it allowed us to perform the work more efficiently, effectively and safely.”
For the JE Dunn team, HSRB II was an opportunity to demonstrate and hone its skills for similarly complex future projects. Constructing a building that will make a difference in people’s lives for years to come also left the team members with a sense of satisfaction.
For Cornell, the work was particularly meaningful because he himself benefited from cancer research conducted at Emory when he participated in a clinical trial for a new treatment.
“I've done healthcare and lab construction work for years, and it never really hit me like it did here, that this really does help people,” Cornell said. “Hopefully, the research performed here by Emory will help other people like it did me.”
This article was produced in collaboration between JE Dunn and Studio B. Bisnow news staff was not involved in the production of this content.
Studio B is Bisnow’s in-house content and design studio. To learn more about how Studio B can help your team, reach out to studio@bisnow.com.