New Research Facility Aims To Spur Innovations In Construction
The construction industry faces a multitude of challenges, from the rising cost of materials to the labor shortage to the impact buildings have on the environment and the need to make buildings resilient to natural disasters.
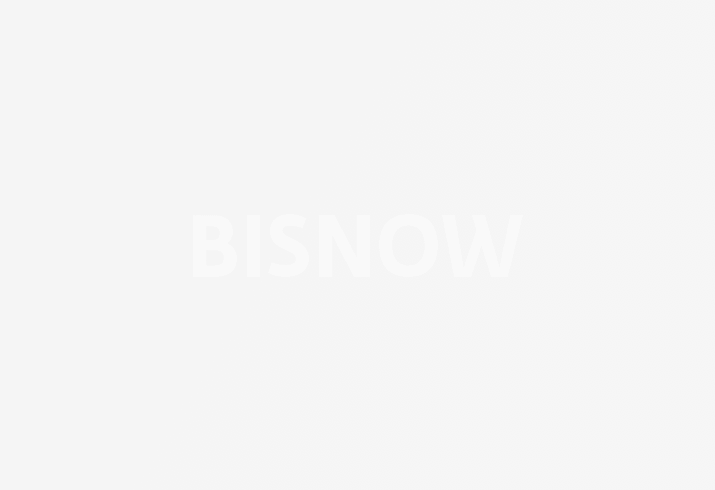
A new lab facility Hitt Contracting opened this month in Falls Church, Virginia, aims to help find solutions to these problems by developing and testing new construction materials and technologies.
The 8,600 SF facility, branded as Co|Lab, opened June 14 at 2757 Hartland Road in Falls Church. Hitt Contracting Vice President of Sustainability and Innovation Katie Rothenberg said the facility aims to help the construction industry catch up to other sectors in innovation.
"The construction industry as a whole invests less than 1% of revenues on research and development," Rothenberg said. "Other industries invest many times that, so there's no wonder we have room for improvement."
Rothenberg said Hitt has previously conducted internal research and development, but it saw the Co|Lab facility as a way to bring in new partners and collaborate in solving the industry's problems.
"This was an opportunity to make a more outward-facing commitment given the challenges the industry faces whether it's changing technology, workforce development issues, changing project economics or resiliency," Rothenberg said. "There's a lot of opportunity for us to come together and find ways to move the market forward."
The facility launched with six seed projects, and Hitt plans to bring in new projects over time. One of the seed projects, from a company called BioMason, is testing a method for growing bricks using microorganisms, a more environmentally friendly way than the carbon-intensive process of firing the material.
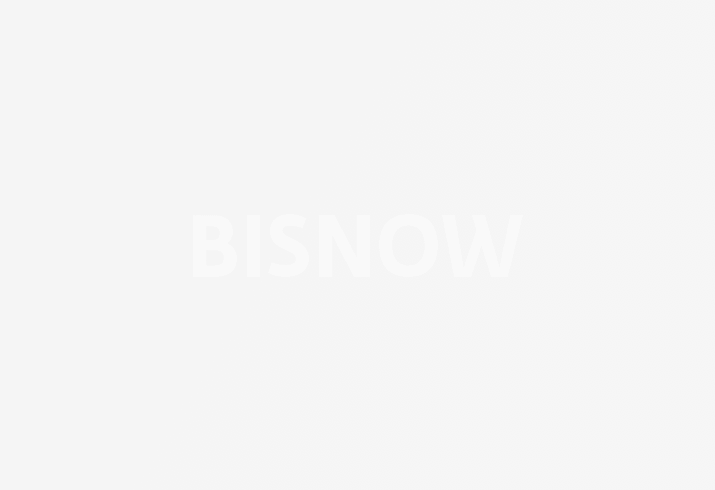
Hitt is also demonstrating an environmentally friendly building method with the Co|Lab facility itself. The building, designed by William McDonough + Partners, features a rooftop solar array, and it was the first structure in Virginia to be built using cross-laminated timber, the team said.
The use of cross-laminated timber, a subset of the mass timber product type, involves prefabricating wood panels off-site that fit the exact dimensions of a project. The method requires fewer people to put together on-site than a typical building material. Rothenberg said developers are becoming more interested in using this material because it can reduce labor costs and is good for the environment.
"Part of what makes mass timber as a structural product so interesting is it is effectively a prefab product," she said. "The reason prefab and modular construction is interesting is it's a way to build more efficiently, which we're all going to need to do if we have fewer people to do the work."
To prepare for the effects of natural disasters and climate change, D.C. and other cities have been introducing policies to push building owners to make their properties more resilient. Rothenberg said the Co|Lab facility aims to help discover new construction materials and methods to help buildings achieve that goal.
"Designers and operators have to start looking at resiliency whether we want to our not, because many municipalities are making us," Rothenberg said. "It’s not going anywhere ... We're looking at different products and methodologies to inform how our clients might better think about resiliency during design and construction."