Smarter Deliveries Make For A Smarter Contractor
Since construction began, thousands of trucks have visited the Mission Bay site where Truebeck Construction is hard at work on a new campus for Uber Technologies. Trundling through the gates, the trucks drop off their payloads of steel, concrete, tiles, screws and hundreds of other materials, then drive off.
And for the first time, Truebeck knows exactly when and where every truck will arrive.
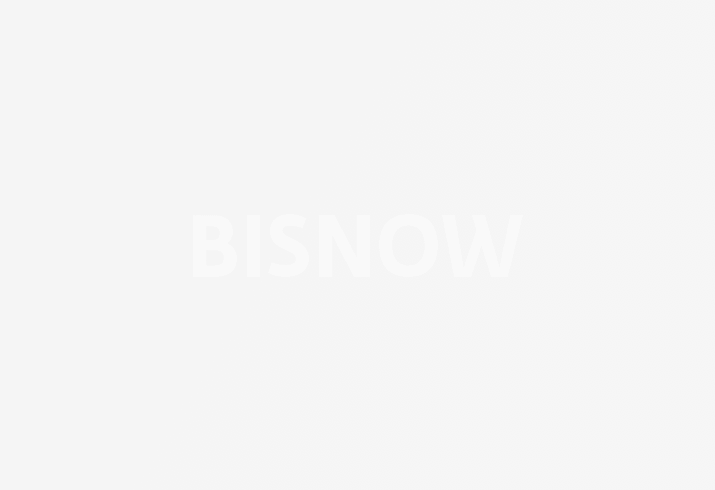
“It used to be that at least 30% of deliveries were unplanned,” said Justin Porter, Truebeck’s director of construction technology and innovation. “Now, that’s dropped to 1%.”
In 2018, Truebeck partnered with a team from LafargeHolcim, one of the world’s largest suppliers of construction materials, to develop a technology that would simplify the chaotic world of construction deliveries. The result was StruxHub, a project management app that lets subcontractors schedule deliveries for exactly when they need materials, keeping trucks flowing around the site and letting construction continue as quickly as possible.
Behind StruxHub are CEO Jeff Chen and Chief Product Officer Chris Schmidt. In 2017, Chen was charged by LafargeHolcim to travel the world’s construction sites and determine how technology could make the biggest difference.
What Chen found was that general contractors’ most valuable employees spent hours every day coordinating deliveries for their subcontractors on whiteboards and scraps of paper, even on projects worth half a billion dollars. Many suppliers were never given a time slot to arrive, so they just showed up whenever they felt like it.
When deliveries repeatedly overlapped, work was disrupted. Chaos and delays ensued.
“You’d see trucks lined up and down the street, blocking traffic, honking at each other to get into the site, and a guy in a red hat — that’s the superintendent — trying to break up a screaming match between two subcontractors,” Chen said.
Chen reached out to Porter in 2017 to discuss Truebeck’s schedule management practices. Keeping trucks moving in and out smoothly was crucial for Truebeck since the contractor works in the famously crowded streets of Silicon Valley and San Francisco. The Uber campus in Mission Bay was vying for space with hundreds of other projects, including the Chase Center, the new home of the Golden State Warriors.
On the very first day the three met, Porter led Chen and Schmidt through Truebeck’s active sites, including the Uber campus and Facebook’s MPK 22 offices in Menlo Park. Chen and Schmidt spent a year in the trailers on Truebeck sites, where they were able to test drive and tinker with each iteration of StruxHub, gathering feedback from field personnel.
This close collaboration helped Chen and Schmidt develop a truly field-centric app that was immediately adopted on several Truebeck sites and shaped StruxHub’s overarching mission to help construction sites work at peak efficiency.
“Looking back, I think one of the keys to our early success was the entrepreneurial culture that runs through Truebeck, from the senior executives down to the foreman,” Schmidt said. “Everyone is so open and driven to improve. They were really the perfect partner for us as an early stage startup.”
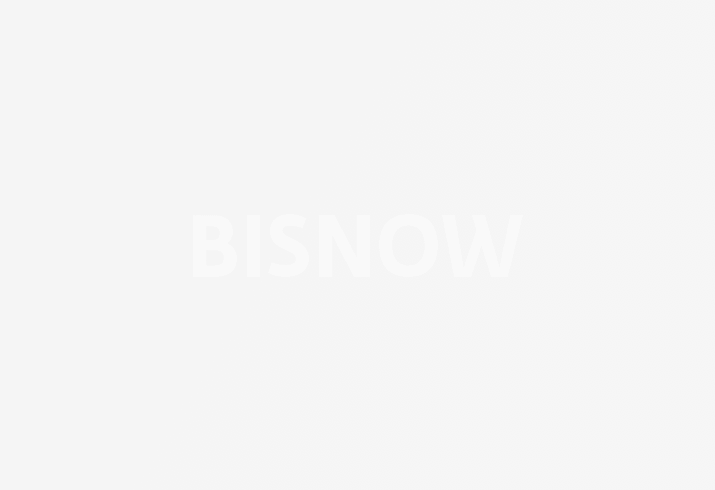
Truebeck was already ahead of the curve when it came to digitizing deliveries, Porter said, but the company’s systems still required project engineers and dockmasters to manually input delivery times. Each subcontractor didn’t always have visibility into what the others were doing, which could lead to conflicts.
“Now subcontractors can see every scheduled delivery and even ones pending approvals,” Porter said. “StruxHub is doing most of the coordination for us now, typically all we have to do is approve the deliveries.”
StruxHub has also allowed Truebeck to get even more granular with its construction sites. At a project in San Carlos, Porter said, Truebeck has split the site into 30 different zones, each of which is managed and scheduled separately. That many zones would be nightmarish to try and manage on a whiteboard, but StruxHub simplifies the complex so that subcontractors can get their material where they need it when they need it.
“The ability of Truebeck to use StruxHub has been monumental in helping us stay on track with our deliveries,” said Nicole Tusa, a project manager at United Mechanical, one of Truebeck's subcontractors. “It’s been great. We’ve been able to schedule everything out through the beginning of the year.”
Implementing the app is one of the latest steps in Truebeck’s plans to become the most tech-enabled contractor in the Bay Area. Porter’s construction technology and innovation team focuses exclusively on ways to gather data and extract insights to help Truebeck plan, budget and build projects in the future.
“We can see the total number of deliveries over the course of a whole project, which often is the limiting factor in construction,” Porter said. “We’re measuring a process that’s normally not tracked at all and finding those hidden pockets of operational efficiency.”
Truebeck has now implemented StruxHub on six of its sites, where the app has so far overseen 4,000 deliveries on 10,000 trucks. Chen and Schmidt are now rolling the app out to the wider community of contractors, but they’ve only recently seen the true mark of their app’s first successful implementation: other contractors getting envious.
“We’re getting calls from other GCs,” Chen said. “They’re saying, ‘Oh yeah, I’ve heard of StruxHub. My subs who work with Truebeck all ask me why I’m not using it yet.’”
This feature was produced in collaboration between Bisnow Branded Content and Truebeck Construction and StruxHub. Bisnow news staff was not involved in the production of this content.