For Biomanufacturing, Changing Science Creating Conditions For Building Boom
The maturation of new life sciences technology will lead to a new generation of cures hitting the market in coming years, which means the business of building and operating a new generation of biomanufacturing plants offers a significant real estate opportunity.
“Every few decades, there are dramatic shifts to the industry,” said Matt Gardner, leader of CBRE's advisory life sciences practice. “The last one was when the whole industry shifted towards monoclonal antibodies, these complex folded proteins. We’ve entered the cell-gene therapy era.”
While deal volume has cooled during the recent period of market and financial uncertainty, demand is only forecast to grow as a wave of life sciences developments mature. Cell and gene therapy, which results in more personalized medicine and smaller-scale manufacturing runs, may have nearly a dozen FDA approvals this year.
That means new facilities will be needed as more products come online. The potential for smaller-scale facilities opens up new opportunities to develop and build on smaller, more urban lots. These kinds of developments have already taken shape in markets such as Boston, Philadelphia, Maryland, the Bay Area and in North Carolina.
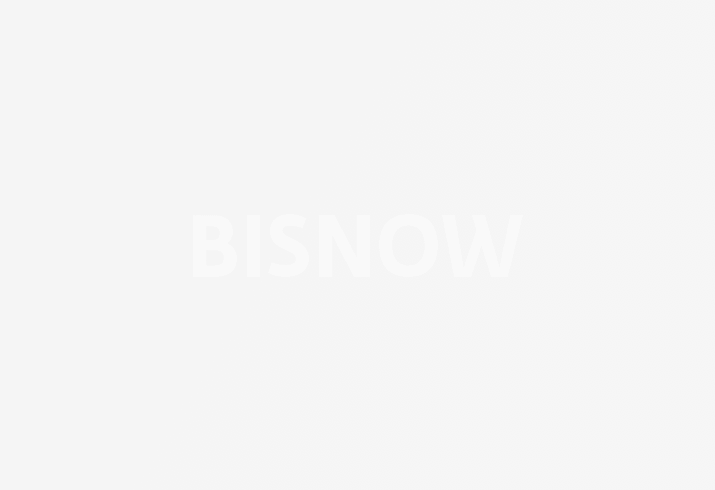
CRB, a firm that analyzes the life sciences and pharma industry, predicts 6% to 10% growth in manufacturing in each of the next three years, and almost all of the 500 companies it surveys annually have plans to expand, with a significant portion making capital investment in manufacturing set to pay dividends in the next few years.
The firm’s 2022 Horizons report also forecast significant growth in manufacturing capacity for RNA-based therapies, and predicted cell and gene therapy manufacturing will skyrocket due to “chronic” shortages. The gene therapy submarket, which raised $10.6B in 2022 — a 14% year-over-year jump — has strong recent clinical trial success, suggesting a pipeline of therapies will make their way to market.
“This has finally been recognized as a specialty asset class,” Gardner said. “The investment has come in to support that, and if you ask any of the players involved, they expect a dramatic increase in demand for biomanufacturing capacity over the next decade.”
You can see the rapid pace of biomanufacturing’s growth in two cities, located on opposite sides of the country. In Holly Springs, North Carolina, a small town south of Research Triangle Park, what was once fields and farmland has become more than 4M SF of biomanufacturing facilities.
In Vacaville, California, new facilities focused on emergent cell and gene therapy have taken shape down the street from where Genentech started manufacturing advanced biologics years ago.
These shifts speak to how the industry — supercharged during Covid and poised to reap benefits from a Biden Administration Covid-era reshoring push and a new generation of cures — is poised to grow. Capacity is short, and whether firms build their own plants, lease a new generation of smaller facilities or pay a contract manufacturer to produce their therapy, it all adds up to demand for new biomanufacturing capacity.
Investors have poured significant money into buying up these properties. Oxford Properties has made a series of investments in the biomanufacturing space, including a $125M purchase of a Boston site in February, and owns roughly 2.4M SF of space over a dozen sites. The multinational’s website says “growing our life sciences business represents one of our highest conviction investment strategies and top priorities, and GMP (good manufacturing process, a type of biomanufacturing space) real estate is a natural and promising extension of that work.” And National Resilience, a firm focused on a variety of biomanufacturing processes, won a $410M loan from the federal government to build a domestic biomanufacturing site.
A center of the industry, Raleigh-Durham, North Carolina, which has seen significant investment and biomanufacturing growth; roughly $6.1B was invested in life sciences facilities in the region in 2021 and 2022 alone.
Eric Forshee, a JLL executive vice president leading the life sciences practice group for the Raleigh-Durham market, said growth in the market is expected to expand in coming years, with roughly 1M SF of biomanufacturing space in the pipeline expected to be finished in the next year. A number of new projects, such as CaMP Helix, The Spark and The Yield, are massive multiuse projects that incorporate manufacturing with commercial, retail and even hotel space, amenitizing campuses that used to simply resemble industrial parks.
“Researchers who are developing pharmaceuticals and biologics don't necessarily have the expertise to scale up and bring things to manufacturing scale,” North Carolina Biotechnology Center Director of Life Sciences Economic Development Katie Stember said. “And so if you can co-locate that talent and expertise, you can learn more before you need to manufacture.”
Other growing markets include Colorado, which has seen a wave of new investment in life sciences properties, and the Greater Houston area. A recent announcement of a new biomanufacturing facility being co-developed in the Woodlands by Howard Hughes corporation joins Alanza and KDI Biopharma, adding manufacturing capacity to a growing life sciences market.
“Regardless of what's happening in the market, right now, the need for this capacity, even for the existing medications that we're trying to make right now, is there,” said Stember.