A Biomanufacturing Bottleneck Threatens To Blunt Biotech’s Boom
Biomanufacturing capacity is at a critically low level for startups and early stage life sciences firms, imperiling the success of new companies and their ideas.
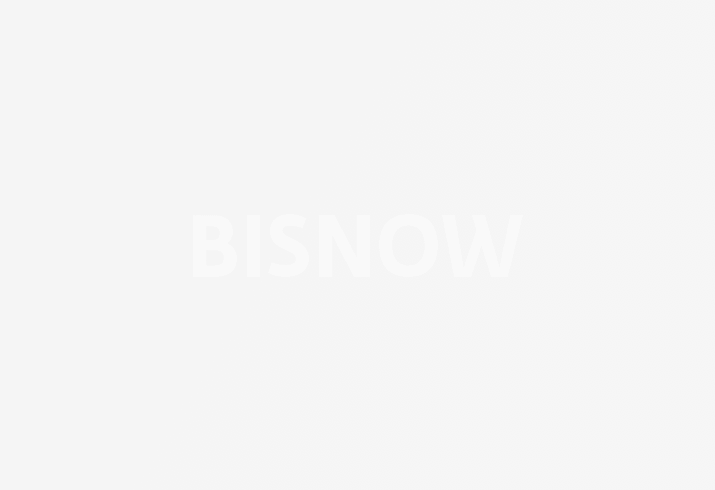
At this moment, a confluence of factors, including the boom in mRNA vaccine technology and new cell and gene therapy firms, has grown beyond the capacity of the nation's contract manufacturing industry, which firms depend on to outsource their therapy production or meet sudden demand. Life sciences startups need these spaces to run clinical trials and work out kinks in their own manufacturing processes before making bigger real estate commitments.
Contract manufacturing organizations are booked solid throughout the rest of the year, said Matt Gardner, a biomanufacturing specialist who was just named head of CBRE’s U.S. Advisory Life Sciences Practice. Finding small-batch production space in the 1,000-liter stainless steel tanks used to create and manufacture drugs or new biologics won’t be possible until 2023.
“There’s nowhere near enough pilot-scale production, which is where companies fail fast and fail forward,” Gardner said. “You want to fail at 500 liters, so you don’t at 50,000 liters. That’s the scale where we see tremendous demand and need much more of.”
Finding concise, accurate data about the industry is challenging due to its sprawling nature, but the available intelligence suggests it is booming. Gardner said he is tracking roughly $6B in biomanufacturing investment in California and North Carolina alone, part of a wave of projects expected to come online as soon as 2024.
Greater Boston, which currently boasts more than 50 firms doing commercial and/or clinical manufacturing and roughly 1M SF of cGMP space — short for Current Good Manufacturing Practice space, which includes biomanufacturing and other drug products — could reach over 8M SF of cGMP space, based on under-construction and announced projects, Cushman & Wakefield East Region Life Sciences Lead Dan Hackett said.
Alexandria Real Estate Equities, the nation’s largest life sciences developer, is working on 1M SF of manufacturing space in San Diego and making similar pushes in other markets, including North Carolina, said Hughes Marino Senior Vice President Shane Poppen, whose advisory firm specializes in life sciences. Alexandria declined to comment.
But much of the product under construction today won't come online for a year or more, and the uncomfortable shortage in biomanufacturing capacity is coming right as two other realities of life sciences development and financing have hit startups.
A shift in the science, especially with the advent of cell and gene therapy, means that “the process is the product,” said Audrey Greenberg, the co-founder and chief business officer at the Center for Breakthrough Medicines, a Philadelphia-area facility that connects small firms focused on cell and gene therapy, a local focus, with manufacturing space.
Game-changing ideas don’t matter unless they can be made at scale, Greenberg said, so firms with their own manufacturing capacity are achieving higher valuations.
At the same time, financing in biotech has crested after a pandemic-era boost and years of record raises and investment, including last year’s $43B haul. Now, the subsequent tightening of the market is making investors look more closely at firms and seek to weed out those with manufacturing issues earlier in the process.
Thomas O’Brien, managing director with The HYM Investment Group, a major Boston-area developer that is pursuing biomanufacturing sites around Boston, said the complexity of the manufacturing process needs to be integrated earlier into the startup cycle, in part because investors are looking at the amount of money being raised and the need for a return.
Some startups that had their own biomanufacturing capacity and suffered setbacks in development, like Boston-based Homology Medicines or Philadelphia’s Tmunity, actually sold back their manufacturing capacity to other firms.
“The manufacturing process takes a long time today,” O’Brien said. “Previously, you’d develop the drug and worry about manufacturing after the fact. Now, it needs to be integrated with the development process and happen in a highly secure place pretty close to where the scientists and executives are.”
Real estate developers attempting to meet this need see exceptional opportunity but also need to contend with the challenging and risky nature of such projects. Biomanufacturing projects often cost roughly $1K a SF and can take up to 36 months to build out when factoring in permitting, local regulations and the numerous validations and sign-offs necessary to certify the facility is approved for medical manufacturing.
Timberline Construction Vice President Devin Gleeson, whose Massachusetts-based firm works on biomanufacturing facilities, said coronavirus-era supply chain issues, the rising cost of key materials like stainless steel and the rush of funding into the sector have driven up costs and created shortages of everything from lab benches to specialized machinery.
“Whenever I look at the growth we’re seeing, you can see truly how multifaceted it is,” North Carolina Biotechnology Center Director of Life Science Economic Development Laura Rowley said.
In her state, she points to developers like Trinity Capital and Crescent Communities and projects like the $1B, 109-acre Spark LS megacampus and INQ 4300, a big-box retail-to-biomanufacturing conversion, that showcase a new generation of campuslike biomanufacturing facilities.
“It’s all about new tech and gene and cell therapy, and we do have that here, but we also have traditional pharma and biomanufacturing, and we’re responding to a pandemic,” Rowley added. “That’s why it feels so big and is so big. It’s all happening at once.”
The present demand is strong enough, and gives developers enough confidence in long-term value, that construction is happening at a brisk pace across the country anyway, including many spec sites.
“Landlords are now willing to give tenants [tenant improvement allowances] for these kinds of facilities where they just wouldn’t in decades past,” Poppen said. “There’s a new confidence level in the longevity of these properties. If something goes wrong with one tenant, there’s more confidence there will still be high demand for the facility.”
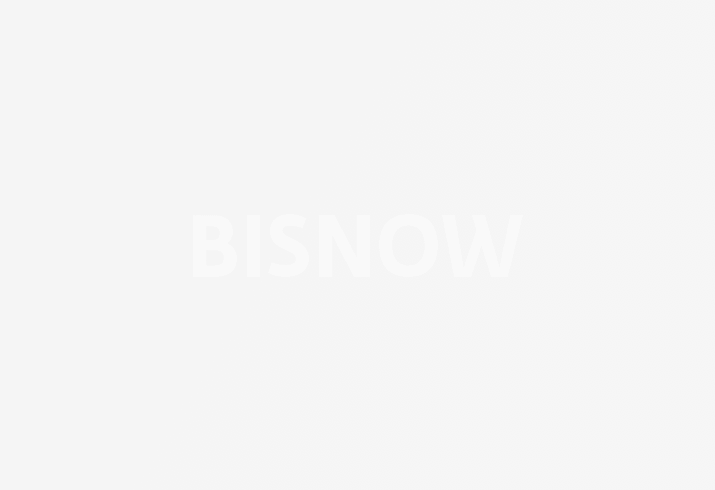
JLL Executive Managing Director Pete Briskman, who leads the firm's life sciences efforts in the Mid-Atlantic, said he believes there is going to be a dispersion of activity outside of the four largest biomanufacturing clusters — Greater Boston, the Bay Area, San Diego and North Carolina’s Research Triangle — into Maryland, as well as up-and-coming markets including Indianapolis, Atlanta, Colorado and Texas.
States can also help tip the scales in their favor with well-tuned incentive packages and tax breaks that favor the industry; the capital expenditures of biomanufacturing make these policies especially alluring to developers.
Maryland is seeing significant speculative biomanufacturing activity, with 600K SF of such space under construction, Briskman said, including projects from the Matan Cos. at 700 North Frederick and Riverside Research Park that are geared toward companies transitioning into preclinical pilot plant and large-scale manufacturing.
To remedy the exceptional shortage of small-molecule domestic manufacturing, many developers are working on a new generation of facilities that combine biomanufacturing and research and development space for startups, like the Center for Breakthrough Medicines, which features extensive shared equipment and manufacturing capacity alongside R&D suites.
BioPlan Associates, an industry analyst, predicted in its 2021 annual report that a number of new trends, including more modular construction and smaller and more flexible facilities, will favor the needs and budgets of startups. This suggests the current absence of available space for these companies' biomanufacturing needs could be alleviated in the coming years.
HYM is hoping to be a part of the solution in Revere, Massachusetts, a 10-minute light rail ride from downtown Boston, where it is working on a massive multi-use project at the historic Suffolk Downs racetrack site. The project includes 100/150 Salt St., a $280M, five-story biomanufacturing facility that combines high-end lab space and multiple floors of biomanufacturing with custom freight elevators for every tenant. Built on spec and set to open in 2024, it is meant to take advantage of the local workforce and closeness to research in Boston and Cambridge.
“In order to be a player, you need to be a spec builder,” O’Brien said. “You need to be in the ground, ahead of the game and moving.”