Tornado Alley Is Growing. Can The Logistics Industry Withstand The Whirlwind?
Industrial developers are going the extra mile to fortify facilities as a confluence of population growth across Middle America and the rise of severe weather events outside of the region known as Tornado Alley puts more warehouses in the path of destruction.
Twenty-seven of North America’s top 100 logistics companies are headquartered in the Midwest, home to several states that fall into Tornado Alley, according to a 2023 report by Transport Topics. But increasingly severe weather ripping through other parts of the country is expanding the definition of which states fall under that umbrella, while population shifts mean more facilities are moving into danger zones.
“Manufacturing, warehouse and logistics folks are going to go where the population goes,” said Kathy Fulton, executive director of the American Logistics Aid Network. “If we are building in places we’ve never built before because people are moving to places they’ve never lived before, then there are hazards that we’re going to have to deal with that we’ve never dealt with before."
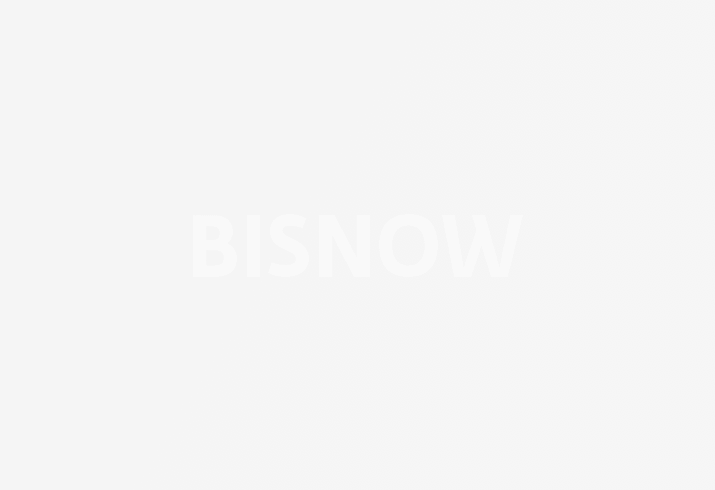
Much of the influx of industrial activity in the region can be linked to pandemic-induced migration patterns, which saw many Americans moving out of large cities and into less populous areas. Industrial demand surged in the Midwest during the health crisis, with a 2021 JLL report projecting the region would need 275M SF of new warehouse space by 2026 to meet demand.
Kansas, for one, landed 21 distribution warehouse or logistics plants in 2022, according to the state’s Department of Commerce, including everything from a $1M investment by Fridgetek to a $326M investment by Heartland Coca-Cola Bottling Co.
“We’re seeing more [severe weather] events, and we’re seeing them in areas we never had warehouses before,” Fulton said. “This propagation of warehouse space over the last decade has put those buildings in areas where tornadoes may have occurred in the past, but they never affected anybody because it was just land.”
At the same time, pro-business policies as well as the availability of land, labor and power in cities like Atlanta, Charlotte, North Carolina, and Nashville, Tennessee, have generated more manufacturing activity in the Southeast, which is home to 28 of the top 100 logistics firms, per Transport Topics.
And while tornado risk has historically been low in the region, a growing body of research suggests that is no longer the case.
States like Arkansas, Louisiana and Mississippi have experienced an increase in tornado touchdowns each year, an April report by Insider found, and researchers warn the storms could become more severe and begin to devastate a greater swath of the U.S.
“There does appear to be a shift [in tornadoes] toward the Southeast,” said Jessica Waters, vice president and manager of climate and structural resilience for commercial property insurer FM Global. “It’s something the science community is keeping an eye on, and it's something that FM Global is certainly keeping an eye on so we can be in a better position to help protect our clients.”
A series of deadly tornadoes swept through southeast Missouri, southern Kentucky, Tennessee and central Alabama in March 2020. The worst of the storms occurred in Middle Tennessee, resulting in widespread damage, hundreds of injuries and more than two dozen deaths, according to the National Weather Service.
More than 400 commercial structures were damaged or destroyed in Nashville, according to CNBC. The impact was especially acute given the exponential population and corporate growth that had occurred there over the preceding decade, driven by companies like Alphabet and Amazon opening up hubs and creating thousands of jobs.
Tornadoes happen with little notice, which makes preparation difficult, said Richard Thompson, international director and leader of supply chain and logistics solutions for JLL. Many companies will shy away from Tornado Alley, he said, but those that choose to go there usually spend extra money on strengthening facilities.
“The holy grail of the supply chain is trying to predict the unpredictable, and tornadoes are the ultimate in natural disasters that are extremely difficult to predict and understand,” he said. “If you can’t stay away, then there are some building designs that are advantageous.”
Choosing the right construction materials is critical to protecting facilities against tornadoes, Waters said. Opting for a concrete roof over metal, or avoiding materials that could become projectiles in severe wind, are some of the things developers in Tornado Alley have to consider.
Those choices, she said, often translate to a heftier bottom line.
“There would be an increase in cost because you are designing the building to be more robust, you’re using heavier construction materials,” she said. “That comes into balancing the business’s tolerance for risk, and is it worth that investment?”
Climate resilience is a top priority for Prologis, the world’s largest industrial landlord, said Carter Andrus, managing director and global head of operations. The company implements disaster response planning and regularly reinvests in its buildings to protect against severe storms, including tornadoes.
“Prologis regularly reevaluates its construction specifications to withstand severe weather events to the best extent possible,” Andrus said in an email. “For example, we have increased the thickness of roofing materials used and added protection around HVAC units to improve resiliency of our portfolio.”
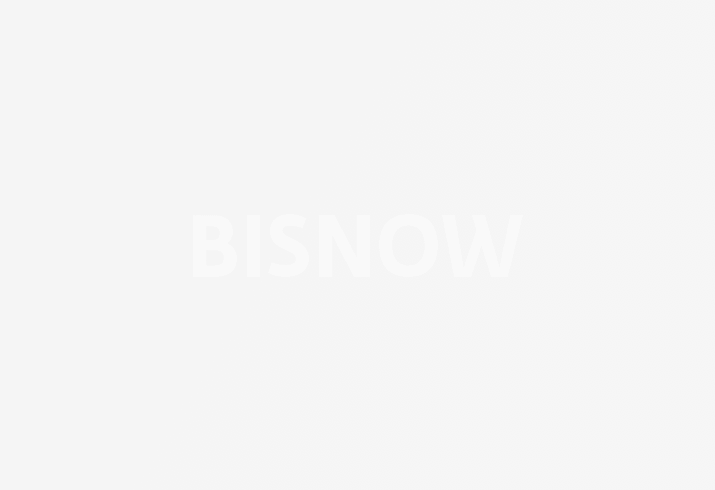
The decimation of transportation infrastructure can cause major supply chain disruptions in the event of a tornado. Last-mile logistics companies like Senpex use technology that aggregates real-time road data from various sources, including Google Maps and OpenStreetMap, to optimize routes so the business can continue to operate.
“This is our core, main problem for logisticians,” Senpex owner and CEO Anar Mammadov said. “The efficiency of the routes and how to make sure drivers are delivering more stuff in a short period of time.”
But most manufacturers and logistics service providers don’t have the resources to make these kinds of structural or technological investments, Fulton said, which is where the public sector and nonprofits like ALAN have to step in.
“So many organizations just don’t have the money or the time or the staff to even build a simple business continuity plan or do a simple risk assessment,” she said. “That’s no shame to those organizations; there has to be a way that we make that easier for them … It’s an industry problem that all of us need to work towards together.”
FM Global invested $300M into the 2022 launch of a program that helps policyholders protect against flood, wind and wildfire exposure, Waters said. The credit has the potential to reduce total losses by $120B, per FM Global’s website.
The Federal Emergency Management Agency also helps communities safeguard against natural hazards through the Building Resilient Infrastructure and Communities program. This year’s program awarded $136M to 325 applicants across 55 states and territories, per FEMA’s website.
These types of partnerships help harden infrastructure and drive business into areas that would otherwise be avoided due to climate risk, Fulton said.
“It’s going to keep our supply chains running after a disaster if we’re not losing power, if we’re not losing water, if we’re not losing whatever resource that building needs,” she said.
The threat of tornadoes is unlikely to drive companies away from certain areas, Thompson said. There’s just too many other benefits that outweigh the risks.
Ultimately, whether or not a company lays down roots in Tornado Alley or any other market prone to natural disasters will come down to their tolerance for risk, Waters said.
“There are things that can be done to mitigate losses, but not all losses are preventable,” she said. “As an organization, the firm needs to look inward and really understand where their vulnerabilities are and where the heartbeat of their company is — that will help inform their decisions on where they’re going to build and where their logistics are located.”