Chip Shortage Driving Explosive Growth In Demand For Industrial Space
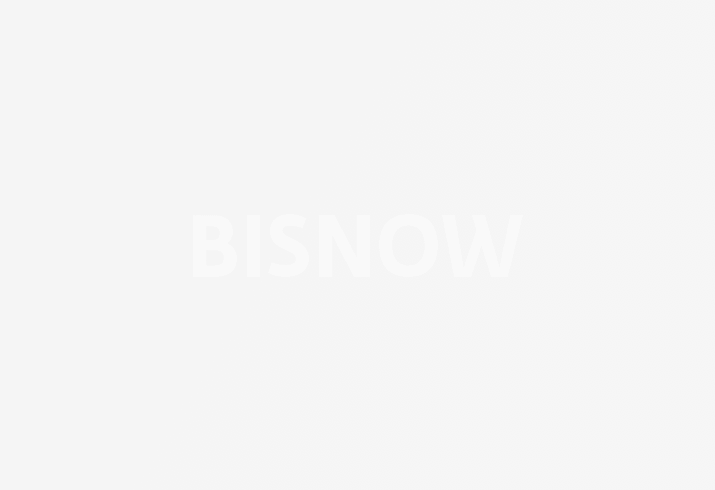
The global pressure on semiconductor manufacturing is turning the industry into a gem for industrial real estate.
Chip manufacturers are betting big on U.S. industrial plants. The semiconductor industry as a whole spent nearly $150B in capital expenditures last year, and it is likely to spend more than $150B for the first time in 2022, according to a fall report from the Semiconductor Industry Association.
That's a big leap in CapEx: Prior to 2021, the industry had never spent more than $115M in a year.
The increase in manufacturing space also means an increase in demand for other kinds of logistics space as suppliers follow manufacturers, John Morris, an executive managing director with CBRE, told Commercial Property Executive.
"Manufacturing investments like these do indeed create a cascading impact on local economies and on the logistics real estate markets in the area," Morris said.
Semiconductor inventory has fallen precipitously for the industry just as demand ramps up. Across all buyers, median demand for chips increased by as much as 17% between 2019 and 2021, according to a report released by the Department of Commerce last month.
The demand comes from a variety of sectors beyond just cellphone manufacturers: automakers make up 42% of buyers and healthcare and medical users make up 18%.
Meanwhile, chip suppliers report their median inventory of in-demand products has dropped from 40 days to less than five days between 2019 and 2021.
"There is a significant, persistent mismatch in supply and demand for chips, and respondents did not see the problem going away in the next six months," Commerce Department officials wrote in the report.
Lack of capacity in the U.S. was identified by chip buyers in the Commerce Department report as the No. 1 cause of the bottleneck in chip supply — leading many firms to ramp up their domestic production.
Major manufacturers like Intel are pouring big money into U.S. industrial spaces. The Santa Clara-based tech giant announced in January it planned to spend at least $20B across two new semiconductor plants near Columbus, Ohio. Intel said the campus in Licking County could eventually hold eight factories through a roughly $100B investment.
Other states are seeing the manufacturing money roll in as well. Outside Austin, Texas, Samsung is investing $17B to build a 6M SF manufacturing campus. Micron Technology Inc. is reportedly considering two counties outside the Central Texas city for a $40B chip plant.
The knock-on increase in demand for manufacturing space is already unfolding in Arizona, where Taiwan Semiconductor Manufacturing Co. is building a $12B, 3.8M SF chip campus. Kevin Helland, a senior vice president at Avison Young who works in the industrial space, told CPE that additional Taiwanese suppliers are also planning to open in the area because of the TSMC plant.
"We have experienced a significant increase in interest in our land listings in Pinal County as a result of the TSMC plant," Helland said.