Yes, They Scan: How A General Contractor Minimizes Disruptions While Keeping Hospital Renovations On Schedule
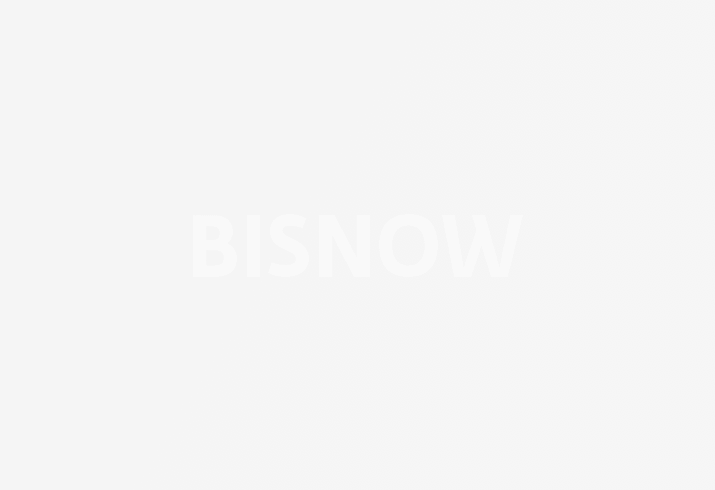
When El Camino Hospital set out to renovate its Imaging Services and Emergency Department in its Mountain View, California, location, it knew it wouldn't be a simple task.
Doing this type of project — which involves renovating two CT scanner rooms, two general radiography rooms, two radiograph/fluoroscopy rooms, two MRI rooms and one PET/CT room — comes with several complications. This type of machinery can't simply be taken away and replaced when it comes time for an upgrade, and hospitals need to be sure the rooms are prepped for the installation and that new equipment can be installed with minimal disruption to the hospital’s day-to-day operations.
While it may seem like a contractor could check a hospital’s as-built drawings to see where old equipment is connected and new equipment needs to go, that isn't always the case — it just isn’t that simple.
“Contractors will often discover that the as-built conditions of a hospital do not match the original plans,” Truebeck Construction Vice President of Operations Pete Caputo said. “A lot of time, people’s as-builts will show ductwork or lighting in a certain spot, and they change it as construction progresses and not update the plans. Or they will move things and not document it.”
Caputo, whose company is working on the project with El Camino, said that when discrepancies like this are found, the new drawings require amendments that need to be approved by the California Department of Health Care Access and Information. This is a very time-consuming process. If contractors begin to take things down only to discover that the hospital conditions vary from what the documents said, it can turn a 90-day renovation into a nine-month ordeal.
Truebeck has a solution to this problem. The company scans all of the existing conditions in the ceiling above and below a room to develop a point cloud that documents ductwork, lighting, HVAC systems or anything else that needs to be taken into consideration. That cloud is then translated into a 3D model that Truebeck uses to coordinate the new utilities for the project.
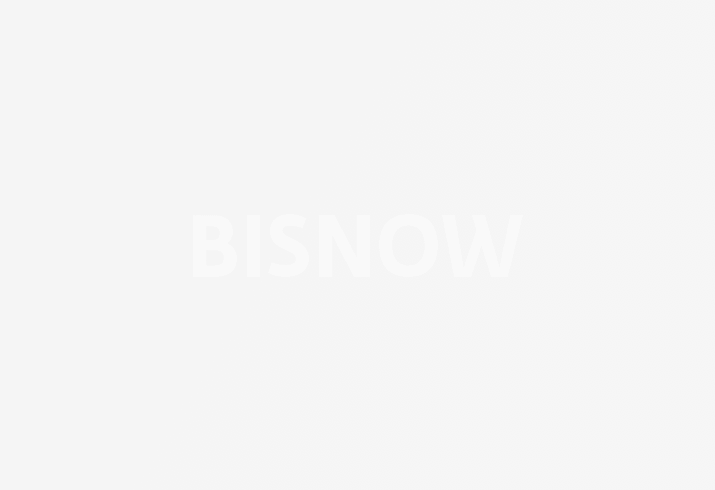
Caputo said the Truebeck team utilized the information from the scan and model to resolve over 80 conflicts that would have otherwise been discovered during construction and submitted an amended construction document to HCAI before beginning the project. When the equipment was taken down, the team discovered the conditions were exactly what was expected based on the model, allowing them to keep the project on schedule without further modification to the approved plans.
For the El Camino project, Truebeck Senior Construction Technology and Innovation Manager Michael Vachon coordinated the scanning in all areas impacted by the renovation over eight nights to limit interruption to the hospital’s operations.
“We're using a laser scanner to capture and document everything above the ceiling and below the floor all at once to 1/8-inch fidelity,” Vachon said. “We’re then utilizing and sharing our findings throughout the entire coordination process, without the need of having repeat visits, where people are going to be possibly disrupting the hospital activities, going into the environment and having to do their normal field measurements.”
Truebeck Senior Project Manager Michael Hazel said another thing that sets Truebeck apart is that the company not only owns this scanning technology but also trains its in-house staff to use it so it doesn't have to rely on third-party vendors for this part of the process.
He said this technology has transformed Truebeck’s process for these types of projects. In the past, the team would have to design a plan and then go into a space, start pulling ceiling tiles and taking pictures of what it found. Team members were also forced to go back and forth between the plan and the existing building design.
Now, they spend a little more time at the front end of the construction schedule doing the building information modeling coordination, but once they have the right information, they can complete the process of tearing down old equipment and getting the room up and running much faster.
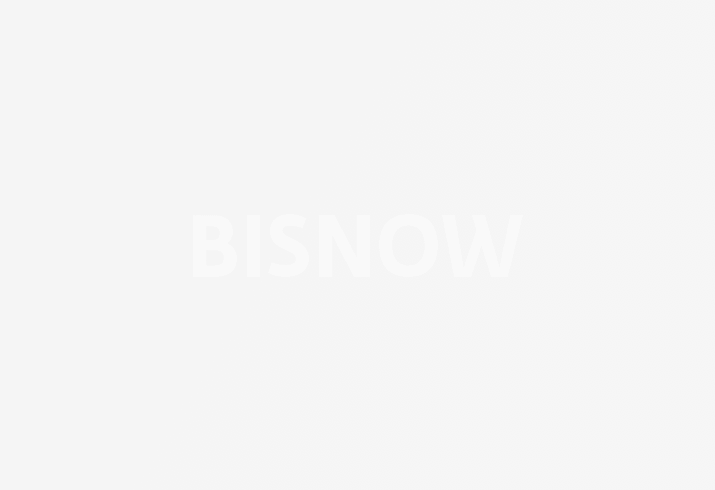
Hazel said that for the El Camino project, his team was able to use scanning technology along with additional augmented reality programs to give the client a real sense of the new design’s space and layout — adding predictability to the end product for hospital staff.
In the end, Hazel said, it is all about giving clients a clear picture while limiting disruptions and inefficiencies and delivering on promises and schedule commitments.
The El Camino project is ongoing, and according to Matt Fardig, who works in facilities development and real estate for El Camino Health, the difference Truebeck’s approach has made is clear.
“We really appreciate Truebeck’s pre-construction efforts: field investigating, 3D scanning and modeling the existing above-ceiling conditions,” he said. “Validating the existing conditions allowed the project team to better coordinate the actual construction activities while minimizing disruptions within the occupied Imaging and Emergency Departments.”
This article was produced in collaboration between Truebeck and Studio B. Bisnow news staff was not involved in the production of this content.
Studio B is Bisnow’s in-house content and design studio. To learn more about how Studio B can help your team, reach out to studio@bisnow.com.