Mass Timber Has A 'Chicken-And-Egg' Problem As Green Building Grows
With 767 mass timber projects under construction across the U.S., there is more demand than ever for the lumber product that is seen as a more sustainable alternative to traditional building components.
But this surge in demand is running into a supply chain marred by pandemic-era economics and trade policy that makes an already more expensive product even pricier. These challenges are holding up the entire industry just as sustainable builders need it to take off.
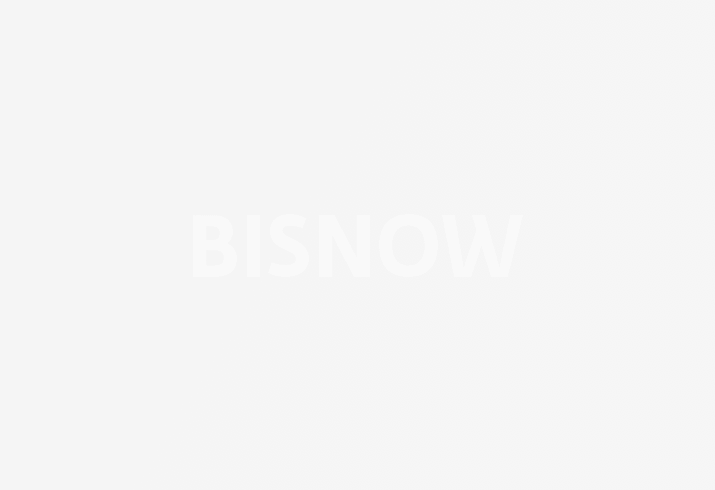
“Mass timber can't move forward unless we can access more material and more manufacturers can come online and domestic supply can increase to drive cost down,” Sam Dicke, business development manager at Timberlab, told Bisnow.
Mass timber has grown more popular as environmental and renewable energy regulations have grown more stringent and the pressure to build green ramps up. Made from multiple panels of wood adhered to one another, it is seen as lower in carbon emissions than steel and concrete and easier on forests than traditional timber. It does, however, have its skeptics.
Whether better for the planet or not, there is no question that mass timber buildings are multiplying and making their way into commercial construction.
One of the best-known mass timber projects in the U.S. is the Ascent, a 25-story, 493K SF mixed-use tower in Milwaukee. Other examples include Intro, a 300-unit apartment complex in Cleveland, and T3 RiNo, a 293K SF office building in Denver.
This year’s 767 projects marks an increase from 600 such projects in 2020, according to the 2023 International Mass Timber Report. Another 910 are in the planning stages, signifying a surge in demand.
The market for the fledgling building material is coping with an uneven lumber supply chain that first inflated as builders ordered as much as they could early in the pandemic, jacking prices sky-high, only to have the brakes slammed when the economy hit the skids in 2022. Dicke said this cycle has happened a few times since the pandemic began, causing prices to fluctuate dramatically and making estimators’ heads spin.
As of Jan. 31, lumber prices stood at about $561 per 1,000 board feet, an increase of 12% over the last six months, even though winter is a traditionally slow time of year for lumber sales, Dicke said. Still, the price of lumber is less than half what it was two years ago when it hovered around $1,500 per 1,000 board feet.
There has been some growth in mass timber production in the U.S., with new sources popping up in Georgia and North Carolina. Mass timber material production in the U.S. increased from 267,900 cubic meters per year in 2019 to more than 348,900 cubic meters in 2022, according to the International Mass Timber report. That figure is projected to increase to more than 800,000 cubic meters per year over the next few years.
But the investment dollars aren’t quite keeping up with demand, American Wood Council CEO Jackson Morrill said.
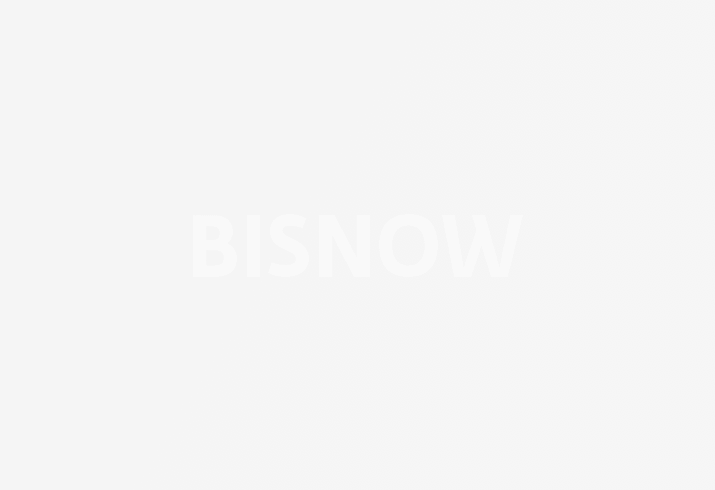
“The manufacturing supply is not feeling the demand is high enough, so we’re not seeing build investments quite yet, and it’s created a sort of chicken-and-egg problem,” Morrill said. “I don’t know when it’s going to go, but I can tell you this: The benefits are too big and too great. It’s just a matter of time when we can find that equilibrium.”
Many manufacturers stateside continue to rely on wood from Germany and Canada, Dicke said.
The U.S. has an 8% import tariff on Canadian lumber, which makes up about 85% of all imported wood materials, according to a 2022 report from the Department of Commerce.
There are also regulatory headaches that mass timber developers are trying to navigate, Morrill said. President Joe Biden has supported growing demand for mass timber development by creating a $32M grant program managed by the Department of Agriculture that aims to expand the use of wood products in construction and strengthen emerging wood markets. Projects that received funding from the grant program include the 88 NoWa Hotel project in Boston and the Star Lofts in Des Moines, Iowa.
On the other hand, the Biden administration’s Environmental Protection Agency is also considering air quality rules that would increase the number of “nonattainment areas” across the U.S. Morrill said the rules, if enacted, could significantly hinder domestic manufacturing of mass timber products.
There are also local challenges. Some building codes still don’t contemplate mass timber production, Morrill said.
Those codes can make it more expensive for developers to get their mass timber projects through the permitting stage, Morrill said. The American Wood Council has been working with enforcement agencies across the country to update codes, but progress has been slow.
The AWC was able to convince the International Code Council, which creates model building codes and safety standards, to include a provision allowing for 100% exposed mass timber ceilings under the ICC’s tall timber regulations. The AWC estimated in its 2022 annual report that the code change could shave $3M in construction costs from the development of a 12-story building.
The code change allowed ZGF Architects to build a 9-acre roof over Portland International Airport’s main terminal with wood that was sourced from a forest within 300 miles of the location.
“These were important additional changes to the code that are attractive to architects and builders, because you want to see the wood and as part of the beauty of building with these products,” Morrill said.