Coronavirus Could Hit Construction Supply Chains Next
A clear picture of the global economic impact of the deadly coronavirus has begun to emerge, and U.S. real estate companies are monitoring how the crisis could play out on construction sites and in development pipelines.
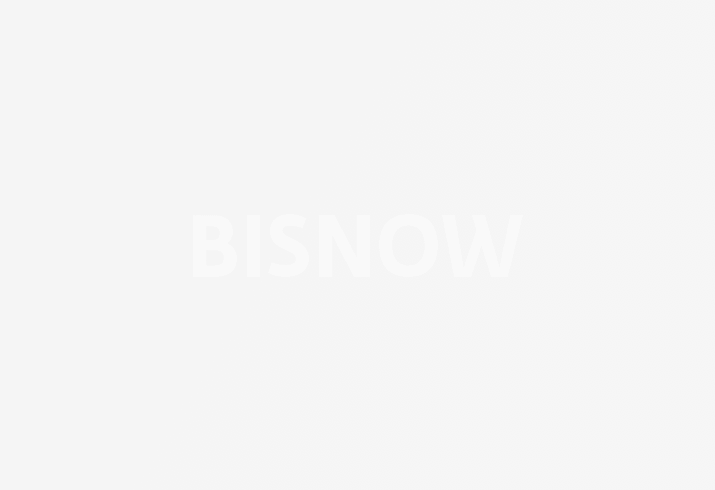
Coronavirus caused more than 2,000 deaths and infected more than 75,000 people as of Thursday, and while most of those are still concentrated in China, where the pathogen originated, its global reach is coming into clearer focus. Coronavirus has impacted the bottom lines of some of the world’s biggest companies.
Apple said Monday its latest smartphones would be delayed as a result of the virus, affecting its first-quarter sales. A drop in demand for international travel due to flight cancellations will cost airlines some $29B this year, the International Air Transport Association announced Thursday. Disney has warned of a hit to its park profits in China — they closed to prevent further spread — while Facebook is enduring a backlog in fulfilling orders for its Oculus Quest virtual reality headset. U.S. retailers are feeling the pinch, though Chinese factories have slowly begun reopening.
While most U.S. real estate impact has been contained to businesses with direct ties to China, material supply chains that begin in China on which construction sites and developments rely could start to be affected by disruptions as the crisis stretches on.
“For the first time this week I heard from two general contractors that they had materials caught up in ports because of the coronavirus — we’re starting to see some of that,” Hoffman & Associates Executive Vice President Maria Thompson said at a Bisnow event in Washington, D.C., this week.
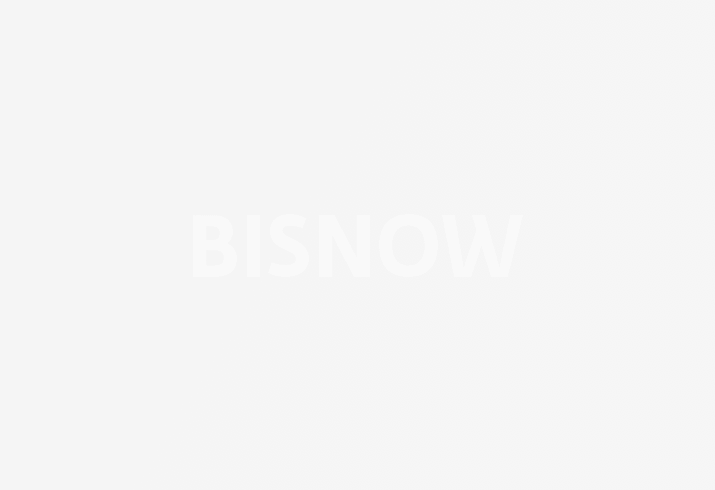
Hoffman and Madison Marquette are co-developers of the massive mixed-used development The Wharf on the city's Southwest waterfront.
“[It’s] something we hadn’t necessarily thought through," Thompson said. "We were thinking more about the labor impacts associated with it and not necessarily getting materials here to the States. So I think that’s a real thing to consider over the next couple of months.”
Representatives for Hoffman & Associates and one of the Wharf's Phase 2 general contractors, Balfour Beatty, didn't respond to requests for additional comments.
Thompson isn’t the only one worrying about what the future could hold. Though some commercial real estate sources said they aren’t feeling any impact just yet, others said they are already operating with the worst-case scenario in mind.
“It takes three-plus weeks on a good day to get anything from China to the U.S., through customs, etc.,” said FullStack Modular founder Roger Krulak, whose firm makes modular buildings at a factory in the Brooklyn Navy Yard and has four projects underway in New York City right now.
While the company's modular factory is local, it sources materials from China. He said construction in the U.S. has a heavy reliance on material that emanate from that country, and specifically pointed to plumbing fixtures, electrical fixtures, concrete boards and flooring tiles.
So far, FullStack's imports have not been affected, Krulak said, but he is expecting that could happen soon. And he is predicting the ripple effects to be felt industry-wide.
"Even a slight curtail in a booming construction market is just going to cause supply constraints,” he said. “From a financing perspective, it's incredibly concerning … [It could mean] construction delays, delays in finishing buildings, delays in certificates of occupancy, increased construction costs.”
The company is looking at sourcing materials earlier than it normally would and possibly looking to rely more heavily on suppliers in Malaysia, Turkey and Thailand.
Lenders have their eye on the problem, too. Avana Capital co-founder Sanat Patel, whose firm has provided construction financing for Marriott International's AC Hotel in Manhattan, as well as projects in California and Georgia, said he is monitoring the situation.
“We do anticipate it coming down the line. Our concern is really delivery times,” he told Bisnow. “If projects are already in production, there is nothing you can do. But if I were starting a project today … as a lender, I would advise them to get ahead on the lead time because of this.”
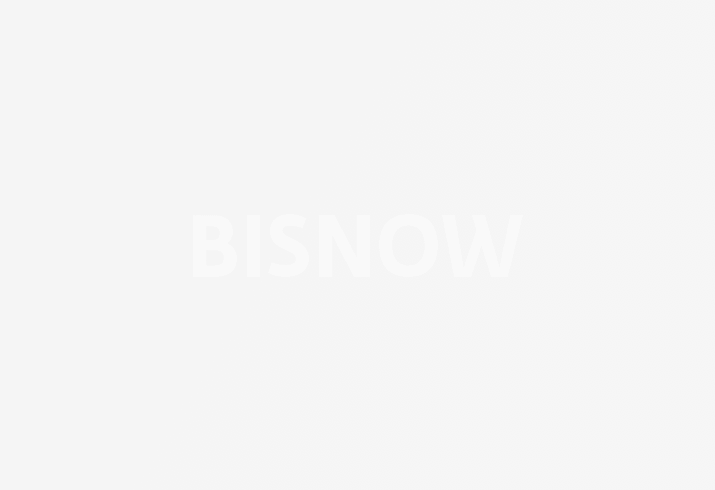
In China, it is hard to move goods by truck because of the government's strict quarantine measures, and there are reports of products arriving at ports with no one there to load them, said Omar Nashashibi, a partner at The Franklin Partnership. His D.C.-based firm does lobbying and government consulting, as well as helps companies and organizations navigate global supply chains.
"You get a lot of steel bars and rods and those items that go into construction that actually come from China,” Nashashibi said. “We are expecting significant delays and disruptions throughout all industries and sectors.”
Complete Manufacturing & Distribution founder Paul Stepanek, who advises companies on getting supplies in Asia and works with hundreds of factories in China, said different areas in China seem to have different rules with the pathogen, which originated in Wuhan, the capital of the Hubei province.
In one region, he said, factory owners were threatened with fines if there was a case of the virus detected at their business. Others are providing free train tickets and chartered planes for people to come back to their homes to work.
“It’s very patchy, but I would say the silver lining, if you will, is that things are moving. Customs is open, trucks can make pickups and deliveries,” Stepanek said. “What we had forecasted to ship in February, there is no way we are going to be able to hit that volume. The factories simply were not open."
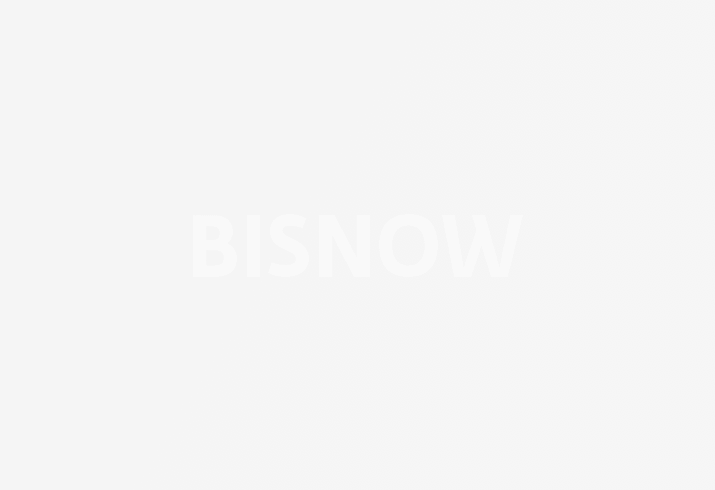
The fallout of coronavirus has come as tensions between China and the United States continue, despite the U.S. and China reaching a Phase 1 agreement in January to de-escalate their ongoing trade war. President Donald Trump had announced increased tariffs back in August on the $300B worth of Chinese goods that hadn't already been affected.
Joy Construction principal Eli Weiss, whose firm is working on a 200K SF mixed-used development in the Bronx, said coronavirus would have been a major problem for construction eight years ago, but not so much in 2020.
"One, because of pricing, and then second, because of tariffs," he said. "We have really shifted away from buying in China for a long time, and I don’t think that’s unique to us."
Joy Construction is sourcing more materials from Canada and other Asian markets, like Vietnam, Weiss said.
“I think it's a good place for some … We’ve had success with China in the past importing materials and we’ve had times at the end of the process, we’ve thought to ourselves, ‘Was the squeeze worth the juice? Did we really save money?’” he said, noting tariffs were a bigger concern for him than coronavirus.
"Just a year ago, we went through a real reverberation in the market with tariffs,” he said. “This is like the third iteration of having to readjust everybody's approach to dealing with China."
Jon Banister contributed to this report from Washington.