Modular Construction Seizing Moment In Hospitality
Board-by-board, nail-by-nail, stick-built construction has dominated how hotels have been built in the United States for more than 100 years, but that could become a thing of the past.
As the hotel industry enters the second decade of the 21st century, pre-fabricated or modular construction is picking up steam.
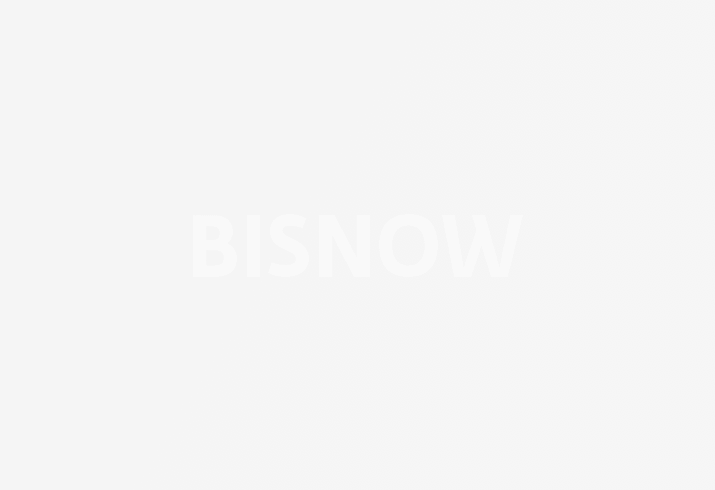
“There’s a movement not just in the hotel industry but across other disciplines that we’re starting to see a trend … you can build your projects faster, produce higher-quality rooms and lower cost in a factory-style development,” Marriott International Chief Development Officer Eric Jacobs told Bisnow at the Americas Lodging Investment Summit at the JW Marriott in downtown Los Angeles this week.
Like all of the other major asset classes, hotel construction is facing a severe skilled labor shortage, higher material costs and other limited resources. Some hotel ground-up developments are taking twice as long to open.
Modular construction is seen as the great equalizer that could increase the volume of units while driving down project costs.
“The time it takes to build a [stick-built construction] three- or four-story wood frame mid-rise hotel used to be about 12 months. Now, we’re at 20 months,” Jacobs said. “Our owners and investors are asking how we can get back to 12 months. One of the ideas is modular construction.”
“It is definitely the future,” R.D. Olson Construction President Bill Wilhelm said of modular construction. “Everyone is trying to get their arms around it. It is a trend that whether it’s tomorrow or the next couple of years, it is out there.”
But is the industry ready for modular construction?
“The biggest obstacle is a lack of understanding and a lack of a willingness to learn about modular construction from the traditional AECO [architect, engineering, construction and owner-operated] community overall,” Modular Building Institute Executive Director Tom Hardiman wrote in an email to Bisnow.
The Modular Building Institute is a nonprofit that serves the commercial modular construction industry.
“Status quo is tough to change and especially challenging in an industry not known for embracing changes,” Hardiman wrote.
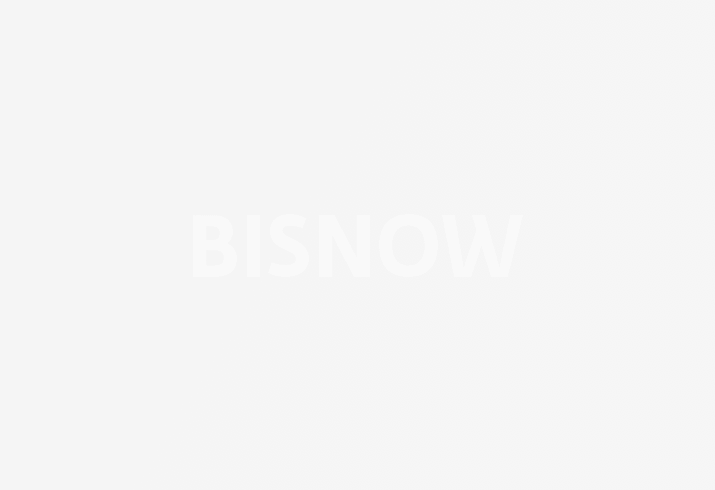
Modular Momentum
With modular or pre-fabricated construction, the building products — from bathroom pods with fixtures to fully furnished rooms — are usually done off-site, in a controlled factory setting, and then shipped to a project site. At the site, the completed rooms are then stacked before adding finishing touches.
Z Modular Director of Business Development Chris Waters said factory workers are doing the same job as on-site construction workers. The modular process is much more efficient, quicker and with better quality control mechanisms than traditional stick-built construction, Waters said.
“We’re building in a production-line atmosphere in some cases under a 200K SF facility in a climate-controlled condition,” Waters said. “We have a viable work pool that is happy to be there because of the climate-controlled conditions — they are not on a job site getting rained on or muddied and the reality is they are doing the same job.
“It’s not right for every situation but it is a viable alternative, especially for hospitality. It is an ideal product profile,” Waters said, adding that modules have a size limitation.
Z Modular is currently building a student housing project near Texas State University in San Marcos, Texas, slated to be completed next year. The firm also has seven projects in the pipeline, including hotels.
But modular construction faces challenges for hotel adoption.
CM&D - Construction, Management & Development Chief Operating Officer Demos Pragastis, who spoke on a panel at the ALIS conference, said he is still skeptical of the product.
Design might be an issue, he said. And having to educate the local government building authorities and jurisdictions might take too long. Lenders and bankers need to be educated about this product, too.
There are a lot of upfront costs and individual unit sizes are limited.
With few modular manufacturing companies, shipping the finished product is also seen as an issue, along with cost. There are only about 200 or so modular manufacturing companies in the U.S., according to the Modular Building Institute.
“The biggest challenge we all have is finding a way to understand it better where we can benefit and capitalize on our cost savings that we all believe will come with it in time,” said Olson, the president of R.D. Olson. “To this date, I haven’t seen any cost savings.”
Jacobs, the Marriott executive, said the cost of a modular hotel is the same as one being built as a traditional stick-built construction. Where a developer saves money is time.
The quicker a modular hotel opens, the sooner it can generate income, he said.
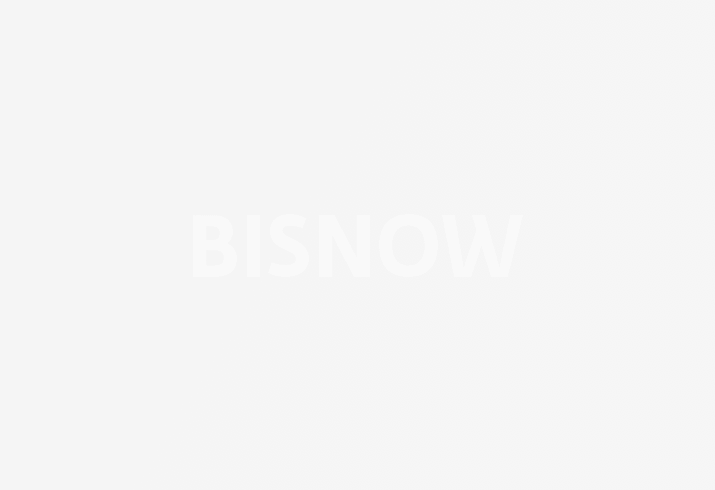
Hotel Brands, Developers Embracing Modular
The Modular Building Institute's Hardiman said driving the growth of this industry is a perfect storm of factors.
The U.S. is facing a skilled labor shortage, high housing costs, a high demand for all types of construction projects and a massive need for affordable housing nationally, he said.
Four years ago, modular construction represented just over 2% of all new construction starts in North America, according to the Modular Building Institute.
In 2017, that figure had grown to 3.27%, driving over $7B in construction activity, Hardiman said.
Hardiman expects that number to be higher in 2018 and beyond.
"We have two choices for the future of our construction industry and I don’t think this is [in any way] an exaggeration: We can embrace modular and off-site construction processes and become more efficient overall, or we can watch as developers continue to import modules and our construction industry from overseas providers who have embraced and adopted modular," Hardiman wrote.
Marriott is on the forefront of the modular hotel construction momentum but other big hotel brands are following suit.
Hilton is opening its first modular hotel in San Francisco in 2019. Hyatt is reportedly going to have a modular hotel in Winston-Salem, North Carolina.
North Carolina-based Concord Hospitality Group touted the efficiency of its 156-key modular AC Hotel by Marriott built in Louisville, Kentucky, in 2017.
“It opened three months ahead of schedule,” Concord Hospitality Senior Vice President of Business Development Grant Sabroff said during a panel at ALIS.
Marriott International Senior Director Global Design Jennifer Abuzeid said the modularly constructed Courtyard by Marriott Los Angeles LAX/Hawthorne in Hawthorne has become a flagship property for the company.
The $86M modular hotel, which opened last year, is dual-branded and has more than 350 rooms — the largest modular hotel built to date, she said.
Customers don't know the difference, she said.
In total, Marriott International currently has 28 total projects that have been either hotels or modular bath pods.
Modular hotel construction is the wave of the future, experts said.
"It’s a tool in a tool belt," Z Modular's Waters said. "It’s not for everybody. I think you're going to see some growth. It’s coming. But it’s not fully here yet."
"We're still at the very early stages of modular," Abuzeid said. "We have a long way to go. I think we're going to get there. ... We want the hospitality industry to push for this."