Modular, Long Seen As Cheap Option, Getting More Expensive
Modular construction, though touted as a way to bring down costs and save time, has always been complicated by expensive startup costs and other logistical challenges, but in the wake of another interest rate hike and persistent supply chain problems, the method faces yet another set of challenges.
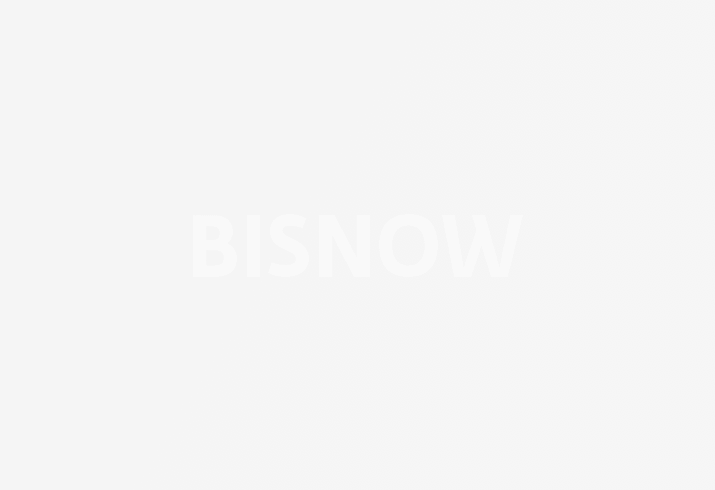
Avana Capital co-founder Sanat Patel, whose company specializes in construction bridge financing, said that the two things keeping him up at night about the current construction environment, especially for building modular, are continued supply chain kinks and rising interest rates, respectively.
Patel said that without the certainty of having materials when needed or locking in pricing, some projects are failing to pencil out, so some projects are still on hold until issues are resolved. Interest rates have also led to similar situations.
“Sometimes, no amount of value engineering [the speakers] can do can offset that,” Patel told the audience at the Bisnow Southern California Prefab and Modular Construction Summit, held Wednesday at the DoubleTree by Hilton Hotel DTLA. “So you have to really make a decision. Do I shelve this?”
Last week brought the third interest rate increase since March in an effort by the Federal Reserve to tame tenacious inflation, but raising the cost of borrowing in the process. Additional hikes are expected by the end of the year.
Patel says the best way to get a project across the finish line now is, unfortunately, an expensive one.
“If you're going to proceed, be ready to open up your pocketbook because it's going to require you to come up with some serious equity into the project,” he said. “None of you like to hear that, I know, but I'm just being very upfront about what can work in financing.”
Assemblage Works CEO Michael Mathews said that between supply chain complications and the continuation of a years-long labor shortage, he doesn’t see the traditional cycles playing out anymore.
“We're never going to have a scene where [subcontractors] are hungry, because we just don't have enough subs,” Mathews said. “And we're not going to get our prices down, because the supply chain — as much as it's simmering down — is still being stressed. So we're at a place now where we need to think about how we unpack that.”
Modular construction is more common but still represents only a fraction of total construction projects. In 2020, modular projects represented 4.39% of all construction projects, according to data from the Modular Building Institute. A big jump from about 2% in 2015, but not a huge piece of the pie. In Los Angeles, off-site construction methods have been used to build student housing, affordable housing and even a hotel.
Speakers at the event also discussed the importance of coordinating with all involved parties, from general contractors to architects, during the earliest stages of the process and underscored that off-site construction isn’t something that a project can pivot to midway if it has been designed otherwise.
“We get a lot of calls from people who want to leverage our system, but it's after the design of the project is complete and it’s to solve a problem — whether it's a scheduling problem, a manpower problem, or a cost problem in most cases,” Clark Pacific President Geene Alhady said. “It's very hard for us to do that.”