Mass Timber Branches Out Across Texas As Developers Look To Save Time, Fill Buildings
Mass timber has historically been shunned as too expensive and too risky. But commercial projects in Texas are beginning to emerge from the ground as exposure to the product and its benefits reach more developers.
Across the state, there are 84 mass timber projects in design and another 50 that are either under construction or already built, according to industry group Wood Works. The material, once subject to a host of misgivings, is now being applied to a variety of asset types, including office, residential, industrial, higher education and athletic facilities.
“Mass timber has so many benefits that go beyond what we first thought,” said Taylor Coleman, a project architect at Gensler in Dallas who heads the firm’s mass timber efforts. “I don’t think it’s a fad. I honestly think we’re just starting to see its true capabilities and nature.”
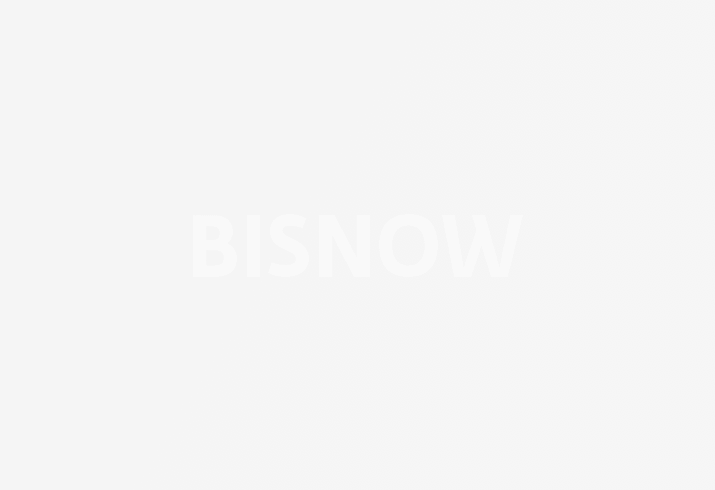
Developers are drawn to mass timber for many reasons. The obvious is its inherent sustainability, which helps investors and other stakeholders meet their environmental, social and governance requirements.
But in an era of high inflation and historically low unemployment, the method’s relatively fast construction timeline and embedded recruitment advantages are perhaps the most appealing. Mass timber buildings tend to attract more tenants as well as more employees, a critical upside given society’s tenuous grip on a full-fledged return to the office.
“The environment in which people work is a criterion that employees are now evaluating as to why they would go to work for Company A over Company B,” said Cody Armbrister, senior managing director of Crow Holdings’ office development group. “There’s an opportunity for us to help companies recruit and retain the best possible workforce.”
Several major Texas developers have thrown their hat in the proverbial tree ring, including Houston-based Hines, which developed a Timber, Transit and Technology — or T3 — prototype that is bringing mass timber offices to cities across the U.S., including a 101K SF building underway in East Austin.
That project came on the heels of The Soto, Texas’ first mass timber office building designed by BOKA Powell in partnership with Hixon Properties and Lake Flato Architects, which debuted in San Antonio in 2020.
“Texas is ahead of some and behind others. You’re seeing some momentum there,” Kathy Berg, a partner at Portland, Oregon-based ZGF Architects, said of the state’s progress with mass timber. “Contractors are getting used to it, but you’re still a little bit more remote from the supply chain than some other states like Idaho or Montana that are a little bit closer to where [mass timber] is being fabricated.”
A thriving timber industry exists in East Texas, but the state hasn't fully put that wood to use. Texas grows upward of 20% more wood than it harvests, which means the market is ripe for the proliferation of commercial mass timber, Texas Forestry Association Executive Director Rob Hughes told Texas A&M Forest Service.
“Cross-laminated timber, made from wood that’s grown here in Texas, is not only a new market, but it’s a big market,” Hughes told Texas A&M. “Texas has eight of the fastest-growing cities in the nation, and with that new growth, new construction, new development — there’s so much potential there.”
The state doesn't yet have a homegrown CLT manufacturer, Hughes said, but that hasn’t stopped the material from rippling through the development community.
After rooting down in Central Texas, the trend finally made its way north.
In September, Crow Holdings broke ground on The Offices at Southstone Yards, a 235K SF project in Frisco that will be the first mass timber building of its kind in the region. The project is being designed by Duda|Paine Architects in partnership with Gensler and is slated for completion by the third quarter of this year.
Strong demand for high-quality office space in North Texas pushes savvy developers to go the extra mile to attract tenants, Armbrister said. Offering a biophilic office environment enveloped in mass timber, something that hasn't yet been done at this scale in this part of the state, was a compelling way to stand out.
“You’re always looking for points of differentiation, to stand apart from what can be a really crowded field,” he said. “You’ve got to do all the other things right, but we are always looking for that competitive advantage.”
The cost implications of using mass timber over traditional steel and cement can be hard to ascertain, Berg said. ZGF has worked on dozens of mass timber buildings, including the practice facility for the San Antonio Spurs. Costs vary widely for each project, she said.
Whether a building is constructed entirely of mass timber or is used as part of a hybrid system can affect cost. General volatility in the construction market can also dictate how timber compares to other materials.
“I could point to a building where we’ve done mass timber and it was cheaper than the alternatives we looked at, and I could point to a building where it was more expensive,” Berg said. “I don’t think you can say unequivocally that it is always more expensive or always less expensive — you have to look at it on a project-by-project basis.”
Even when mass timber carries a bigger price tag, developers tend to recoup those costs via a truncated construction process. It takes less time and fewer workers to construct a mass timber building, Armbrister said, which helps drive down development costs even if the material is sometimes more costly.
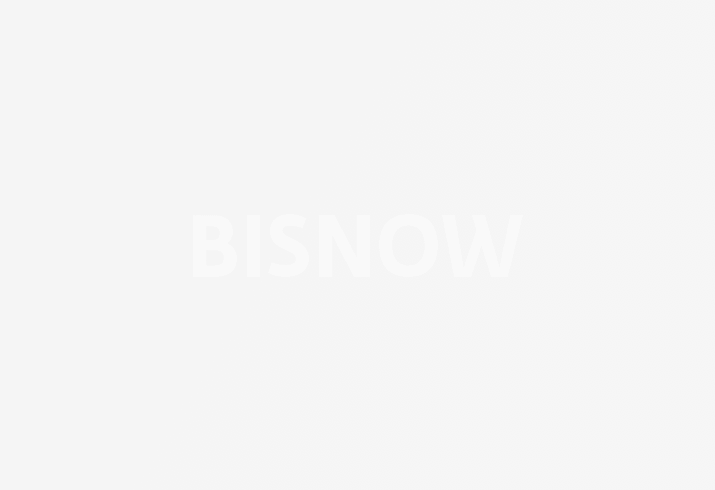
“We can deliver these projects anywhere from 15% to 20% faster than typical concrete construction,” Armbrister said. “That’s faster that we can get to the space to lease it to generate income, and that’s, in theory, less debt service we have to pay while we are under construction.”
The flip side of a compressed timeline is that it allows for a very small margin for error, Armbrister added. Being nimble with the supply chain and knowing how to time the arrival of other items, such as mechanical systems, is essential to sticking the landing on mass timber.
“The good thing is these things are fast to build,” he said. “The bad news is, they’re really fast to build.”
Nearly 1,700 mass timber buildings were in process or already complete in the U.S. as of December, according to Wood Works. But in early 2021, HKS estimated the material represented less than 0.000189% of the nation’s commercial building stock.
That mass timber has yet to penetrate the market in a major way may allow developers to charge a premium on rent simply because the material is still a novelty in most places, Coleman said.
“When you talk about the bottom line, it’s obviously cost, but it’s also the attention and the first-to-market feel developers are obviously chasing,” he said.
Innovations in mass timber are allowing projects to go higher, and the material is hardly relegated to massive offices. The Ascent, a 25-story apartment building that opened in Milwaukee, is the tallest mass timber building in the world.
USAA Real Estate just completed a first-of-its-kind mass timber warehouse in South Dallas, Coleman said, and Gensler is using mass timber to design all of First United Bank’s office buildings, all of which come in around 40K SF.
The business has already completed locations in Sherman and Fredericksburg and will soon debut facilities in Plano and Moore, Oklahoma. Offering a mass timber office environment has been a powerful recruitment tool, but the material also drives important foot traffic to the facilities, said Melissa Perrin, First United Bank executive vice president and chief culture and communications officer.
“The community and our customers love the space,” she said. “The attention and visibility in the market is one of the things we’re seeing.”
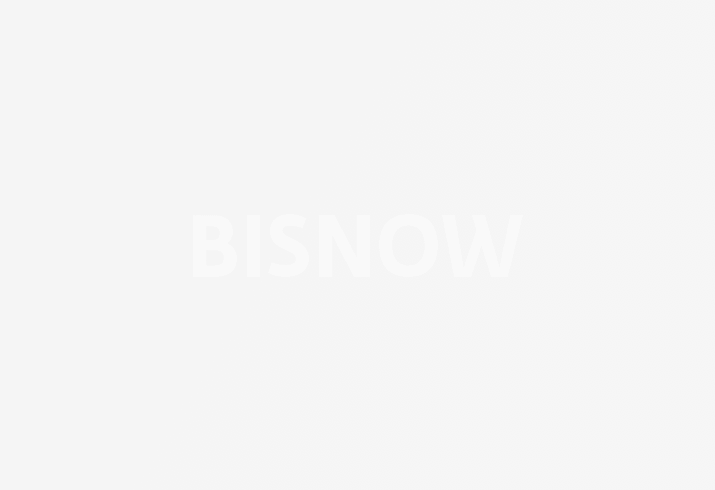
While ESG didn't play into either Crow Holdings’ or First United Bank’s decision to use mass timber, Armbrister said its inherent ESG benefits went a long way in locking in investment during a tumultuous time for office.
“We talked with capital literally all over the world,” he said. “I feel pretty confident in saying, had it not been for the ESG elements of this building, we wouldn't have had those conversations in earnest, especially at the time when we were trying to capitalize a speculative office building. There was a lot of uncertainty, a lot of unknown.”
Texas’ anti-ESG rhetoric could pose a challenge to the prevalence of mass timber in the market. The state's comptroller has called on state pension funds to divest from companies perceived as boycotting the fossil fuel industry, which in theory could limit investments in sustainable buildings.
These obstacles make it all the more crucial for developers to share stories about their experience with mass timber and its ability to produce strong returns, Berg said.
“You don’t even have to talk about sustainability — it’s baked in,” she said. “If we can prove that these buildings have better returns in all markets, then it’s a win-win.”
Despite its many benefits, some investors doubt if mass timber can ever become widespread, especially on a global scale.
Kunal Lunawat, co-founder and CEO of Agya Ventures, said the majority of timber is produced in the U.S., and exporting the material to fast-growing commercial markets in nations like India and China may not always pencil from a cost standpoint.
Height limitations and risks associated with combustibility could also temper mass timber’s growth, Lunawat said. The commercial real estate industry’s focus on sustainability should instead be aimed at simpler solutions, he said, such as offsetting the green premium on efficient heating and cooling systems.
“The most pragmatic, lowest-hanging fruit is heating and cooling,” Lunawat said.
Various methods aside, the built environment generates 40% of global carbon emissions each year, which means commercial real estate has an outsized responsibility to do what it can to decrease impact, Armbrister said. Southstone Yards will be the first in a series of moves by Crow Holdings to make a difference.
“It’s just one building, but everybody’s got to start somewhere,” Armbrister said. “We think it makes a considerable impact on our local environment, and if we can continue to build on this and scale on this, in 10 years if we have a handful of these buildings, we’re doing our part.”
Berg bristled at the suggestion mass timber can’t be delivered at scale. She pointed to the 9-acre mass timber roof that tops Portland’s airport as well as the “hundreds of thousands” of years' worth of wood-based construction as evidence that mass timber is likely here to stay.
“It’s tried, it’s tested, we know it works,” she said. “We’ve got all of history to tell us that there’s no reason why this can’t carry us forward into the future.”