Meeting The Nation’s Demand For Cold Storage And Food Processing Facilities
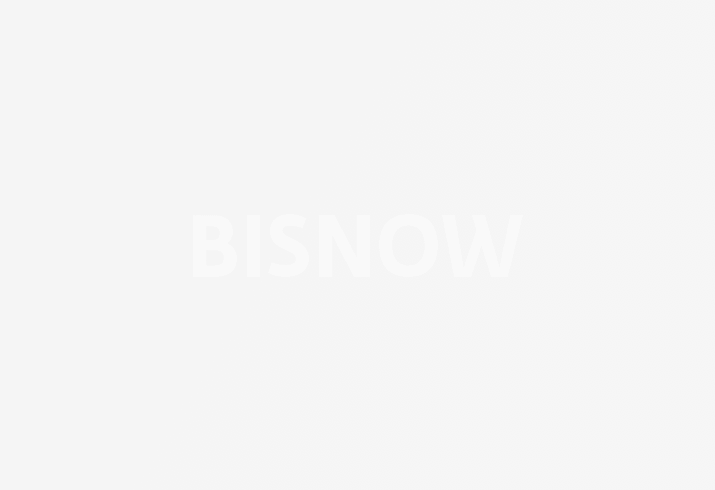
Americans are hungry for fresh food, and their cravings are prompting industrial developers to build more cold storage and food processing facilities.
While the refrigerated storage industry is predicted to grow 3.4% annually between 2014 and 2019, according to JLL, supply has not kept up with demand. JLL expects the number of facilities nationwide to increase 1% annually for the next five years.
The market is demanding new and energy-efficient cold storage space, often combined with a food processing or preparation component. It is a gap in supply that design-build firm FCL Builders has helped fill with its growing portfolio of U.S. Department of Agriculture food production and cold storage buildings.
FCL has offices in Chicago, Dallas-Fort Worth, Atlanta and Baltimore, serving customers in the eastern half of the U.S. and Texas. In addition to being a leader in building e-commerce and warehousing facilities throughout the country, FCL has built a reputation for cold storage design-build expertise. Industrial developers and tenants in these markets have realized the need for new cold storage and food processing facilities, as growing populations put more demand on produce and food distribution.
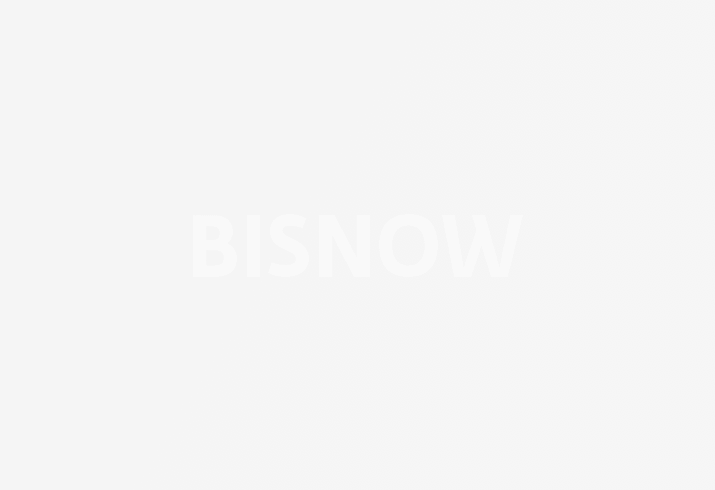
Food wholesalers make up 33% of the demand for refrigerated storage, with retailers cornering 22% of the market. FCL has worked with national retail brands like Trader Joe’s, serving as the design-builder on a 710K SF, three-building food processing and cold storage campus. In Texas, wholesaler Don Hugo Produce hired the company to design and construct a 228K SF produce distribution facility.
The project called for seven coolers ranging in temperature from 34 degrees to 44 degrees, in addition to two zero-degree freezers. The building also called for 10 produce-ripening rooms.
Food manufacturers, who also make up 33% of the market, have enlisted FCL to design and build facilities to keep up with demand. Cloverhill Bakery, a national provider of baked goods, added a 300K SF bakery to its food processing capacity, including six production lines, an ammonia refrigeration system and carbon dioxide freezers.
FCL worked with Mars Inc. in the planning and construction of its 1.4M SF cold storage facility with 336K SF cooled to 42 degrees and 1.1M SF of air-conditioned storage in Joliet, Illinois. The building was designed and constructed to achieve a LEED Gold certification.
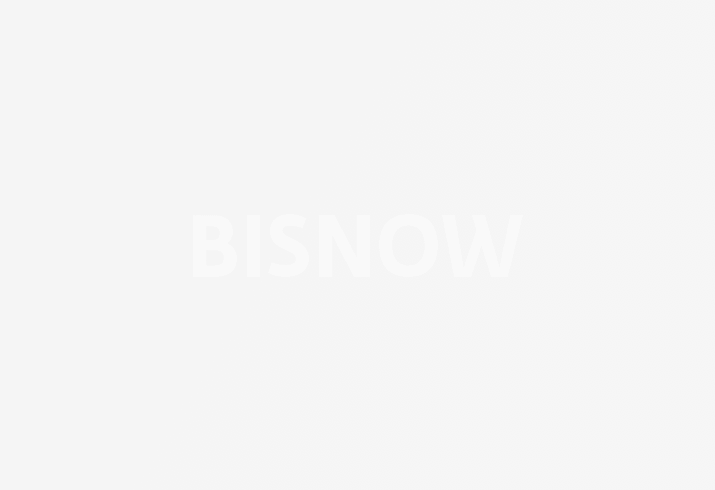
FCL Builders has also worked with major food distributors. Sysco called on the company to design and build a 700K SF cold storage and food distribution facility with an ammonia system. Professional Freezing, a repeat FCL customer, relied on the company’s expertise to build a 522K SF cold storage campus in Bedford Park, Illinois.
Demand for cold storage and food processing has also increased on the East Coast, as ports dredge deeper waters for larger ships and the U.S. supply chains take advantage of vast rail intermodal delivery networks. With the supply chain shifting from west to east, FCL Builder’s East Coast reach and its dedicated USDA food production and cold storage building design-build team are leading the charge in expanding the nation’s food distribution network.
To learn more about this Bisnow content partner, click here.