Boston Has A 'Dire Shortage' Of Biomanufacturing Facilities
The red-hot life sciences market in and around Boston is lacking a critical piece as its growing companies look to expand.
Biomanufacturing facilities are few and far between in the region, and biopharmaceutical companies are scrambling for solutions, experts said. New medicines require fundamentally different manufacturing than the drugs of the past, meaning most of these facilities need to be built new.
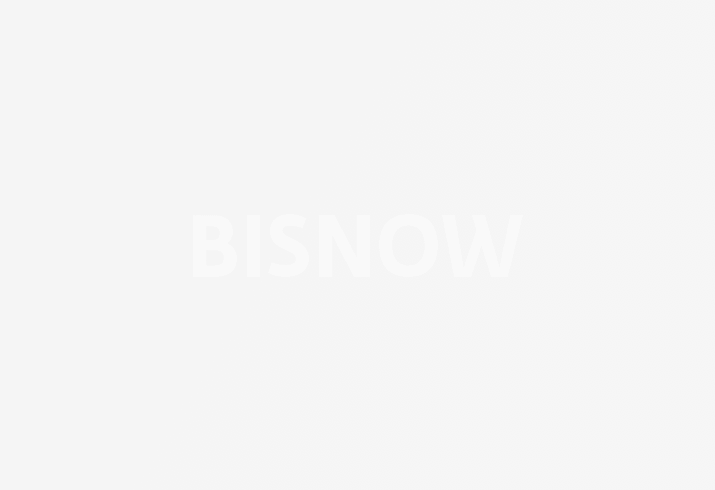
“There’s a dire shortage of this kind of real estate,” King Street Properties principal Stephen Lynch said. “There doesn’t exist, in the U.S., an organized real estate market for this product type. The end users, the companies that need to make these drugs, are scrambling for solutions.”
King Street has formed a biomanufacturing arm called Pathway, and its first development will be a 45-acre campus in Devens. The five-building, 700K SF project this week received approvals from the Devens Permitting Authority to immediately break ground on its first building, a 100K SF speculative facility, Lynch said.
The first major life sciences lease of the year was inked by Oncorus Inc. for a clinical-stage biopharmaceutical manufacturing center 25 miles north of Boston. East Cambridge-based Oncorus, which produces viral immunotherapies, signed a 15-year lease with IQHQ for a new 88K SF clinical manufacturing facility in Andover, it announced Monday.
The facility is expected to begin production in 2023 and gives Oncorus the ability for quality control in its own backyard, an executive said in a statement. The company said it plans to partner with contract manufacturing organizations once operational, in a sign of the demand expected to go well into the future, developers told Bisnow.
“There’s a lot of developers and landlords like us that are thinking and repositioning assets to try to capture that market,” IQHQ Vice President Doug Cuff said.
IQHQ, the life sciences developer that has become a regional competitor, has life sciences developments in West Cambridge and Fenway but had previously only planned to build office, laboratory and research and development space.
“It’s become pretty apparent to us that companies want to be able to control their own supply chain,” Cuff said. “Yes, it may be less expensive to go abroad, but you may want to have your research hub in Cambridge and your manufacturing hub a short drive out of town.”
The Massachusetts Biotechnology Council found a perception in the industry that Massachusetts lacks manufacturing capabilities compared to the Raleigh/Durham Research Triangle area and Pennsylvania, according to a 2020 report.
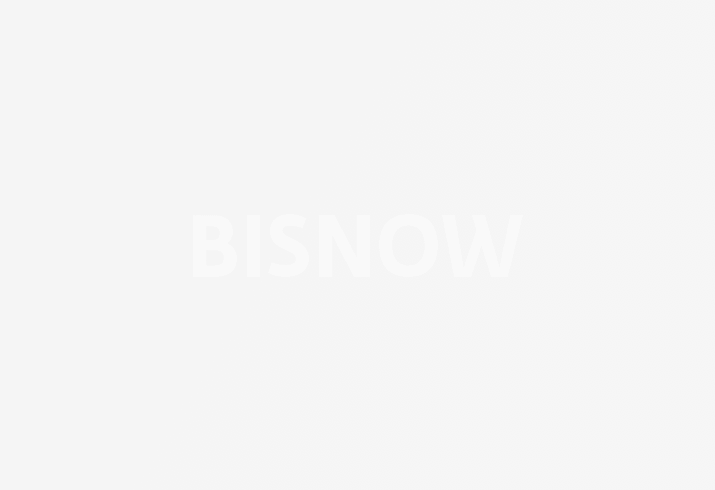
In the past five years, more than $1.9B has been invested in biomanufacturing in Massachusetts, but that has mostly come at the university level, according to MassBio. The demand for new biomanufacturing facilities makes up from 20% to 30% of the current life sciences market demand, brokers said.
The driving factor for modern biomanufacturing facilities is the new class of complicated medicines, Lynch said. For example, an aspirin pill is composed of 21 atoms, while new biologic drugs can be delicate, complex medicines in a liquid form.
Today’s biopharmaceutical production varies greatly from the pill factories of the past, said CBRE Vice Chairman Steve Purpura, who leads the brokerage's life sciences team in Boston.
“Once you get the recipe, you can make it anywhere," he said of past therapies. "This is a little more complicated.”
Purpura cited the complex coronavirus vaccines developed by Moderna, Pfizer and others, which work by using messenger RNA.
“It’s all new technology, so they have to put it near their current research facilities,” Purpura said. “It’s not something they’re comfortable handing off to someone else. That’s the big driver — they're in locations proximate to the research.”
A Pfizer facility in Andover is playing a role in the company's vaccine production, producing the vaccine’s messenger RNA to be shipped to a massive manufacturing plant in Michigan, The Eagle-Tribune reported.
Vibalogics, a virotherapy manufacturing company, signed a long-term lease in November for a 118K SF facility in Boxborough. The life sciences company was selected by Johnson & Johnson as a manufacturing partner for its own COVID-19 vaccine candidate.
“The addition of a late-stage clinical and commercial facility means we can easily tech transfer our customers’ products from our early phase manufacturing facility in Germany to the U.S., resulting in a complete end-to-end service from pre-clinical to commercial supply,” Vibalogics CEO Tom Hochuli said in a statement.
The company plans a $150M investment to upgrade the building for biomanufacturing, according to a statement. Vibalogics didn't respond to requests for comment.
The biomanufacturing demand will require a commitment to development at the state level including incentives to drive new manufacturing ventures, MassBio officials said in its report. The Vibalogics and Oncorus deals are the two most recent biomanufacturing plays in a market that has an “incredible” lack of space in the near term, Purpura said.
“Everything needs to be built,” he said. “The pipeline for the next 18 months is nonexistent.”
The facilities require similar standards as industrial assets, including high ceilings, and adequate loading dock and delivery capabilities, experts said. The typically one-story structures require hospital-grade filtration systems and significant power requirements.
Because of the requirements, rents outweigh the record-highs in Greater Boston’s industrial market, trending more toward standard research and development life sciences deals, JLL Managing Director Don Domoretsky said.
“Along I-495, deals transact in the high $30s to low $40s triple-net,” Domoretsky said. “And along [Route] 128, we’ll say, that same type of deal, probably high $50s to mid-$60s.”
The competition with the industrial market won’t help biomanufacturers in the short term, Lynch said, but won’t slow the demand either.
“We’re at a cold start with biomanufacturing,” he said. “I think the rise of this asset class is going to be something that we see for decades to come.”