Massachusetts' Once-Abandoned Mills Are Now Living The High Life
Massachusetts’ textile and paper mills were crucial drivers of the Industrial Revolution in the 19th century. More than 150 years later, the state’s $2B cannabis industry is reinvigorating its many long-dormant brick and stone warehouses.
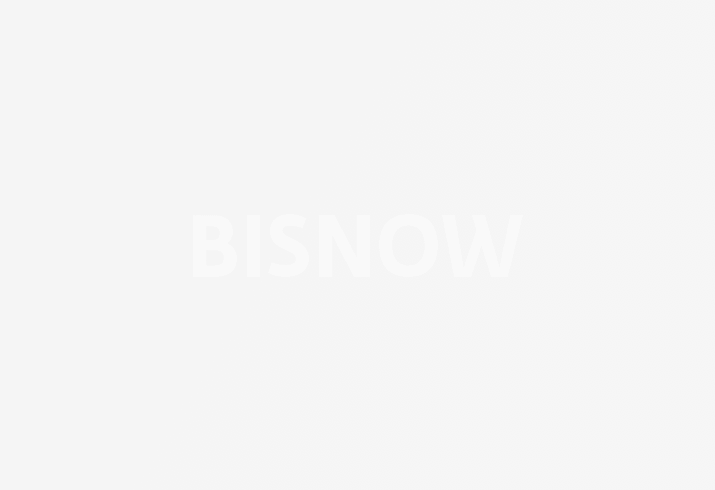
Cannabis growers, retailers and manufacturers are leasing and buying old mills and fixing them up to house their operations. Many of the state's localities are courting marijuana businesses to fill vacant mills to generate both real estate and cannabis sales taxes.
“There are townships around the state that are saying, ‘Hey, we’ve got these buildings, some of the manufacturing presence has died off in the last 50 years, come repurpose these buildings,'” said Chris Zawacki, the CEO of Southbridge-based cannabis business Green Meadows. “We thought it was a great use of the space.”
Green Meadows built its cultivation, retail and manufacturing operations out of a renovated, 35K SF space from a former textile mill that had been turned into the nation's first Ames department store in 1958. Next month, the facility at 64 Mill Road in Southbridge, south of Worcester, will deliver its first cannabis crop after opening in February following 13 months of construction, Zawacki said.
Mills dot the banks of rivers that flow throughout suburban and rural Massachusetts, the remnants of the state’s mid-19th century manufacturing boom. The properties, powered by water and steam, clustered in cities like Lowell north of Boston, where the first major mill complex in the nation was built in 1835, according to the National Parks Service.
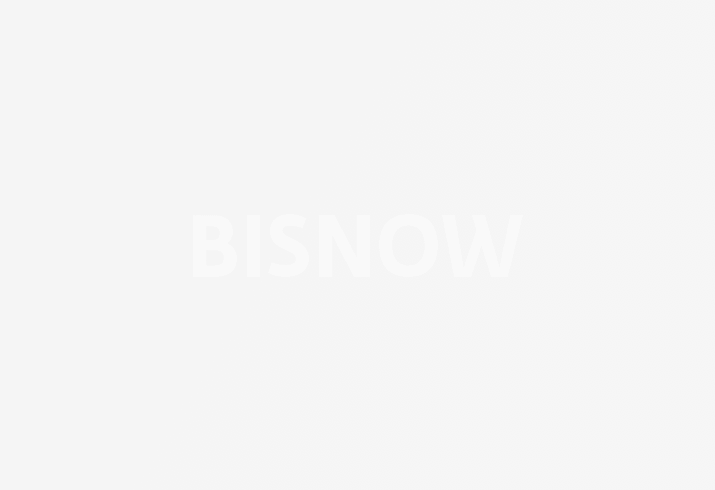
The local economy moved from textile to paper after the Civil War cut off raw cotton supplies from the South, and paper mills thrived in the early 20th century. Holyoke at its peak was home to more than 25 paper mills and was known as “The Paper City.”
The mill ecosystem faded after a last gasp of activity during World War II as manufacturing began to move to the South.
The exodus left dozens, if not hundreds, of obsolete industrial-grade buildings. But following the legalization of recreational-use cannabis in 2017, local politicians quickly recognized that the newly legal industry could awaken the dormant buildings — and generate tax revenue.
Cannabis operators have embraced the invitation and have moved into former mills north of Boston in towns like Fitchburg and Lowell and in Western Massachusetts. Last month, cannabis giant Green Thumb Industries purchased a 326K SF former paper mill in Holyoke for $4.56M.
Then-Holyoke Mayor Alex Morse dubbed his city in 2016 the “Rolling Paper City” in a nod to the new industry following the state’s recreational legalization vote, and he was an early advocate for local cannabis production. In 2017, Holyoke counted more than 1.5M SF of vacant mill space. Today, the town counts nearly 18 mill buildings that have been purchased or have a lease agreement for cannabis operations, a city official told the county’s Daily Hampshire Gazette last month.
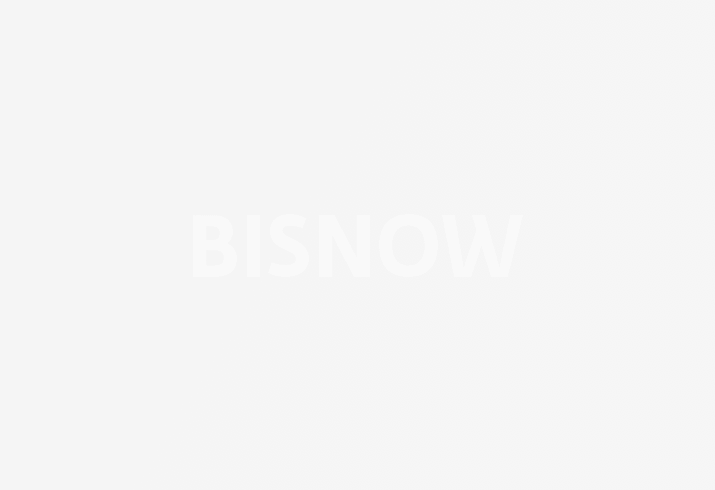
Cannabis businesses moving into mills build a “box within a box,” bringing in either prefabricated cleanrooms or building insulated metal wall panel systems for plants to grow in, McGeorge Architecture principal architect Matthew McGeorge said. The boxes resemble the prefabricated shipping container-like cleanroom boxes in biomanufacturing properties.
McGeorge said he has worked on three Massachusetts cannabis dispensaries, a textile mill conversion in Fall River and is actively working on a mill conversion in Holyoke.
“The challenges to the mill structures are their floor-to-floor heights relative to cultivation programming,” he said. “The energy compliance issues are also a challenge, bringing them up to some reasonable code.”
The cost to build a cultivation facility ranges between $250 to $300 per SF, although it remains dependent on the intensity of a mill retrofit, Zawacki said.
“The cannabis facilities are very utility and engineering intensive,” McGeorge said. “A residential use, on a dollar-per-square-foot basis, is actually more economical [to convert to] than cannabis.”
The mills don’t always offer the speed-to-market cultivators crave because of their unpredictable renovation timelines, experts said. But the buildings are some of the only options for cannabis cultivators and manufacturers to move into — the lack of land and municipal cooperation in Greater Boston’s Interstate 495 ring cost too much to overcome.
Cannabis businesses are vying for their piece of the pie in a market with more than $2B in cumulative sales since 2018 and averaging more than $3M in weekly gross sales, according to the Cannabis Control Commission.
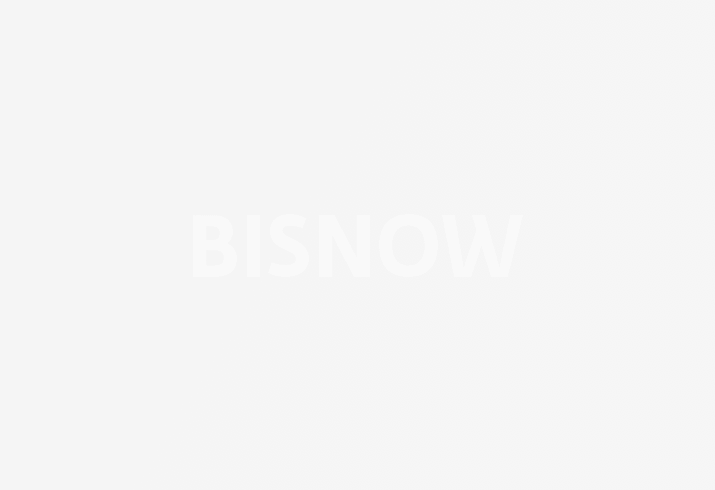
The CCC counts 301 active cannabis facility licenses, with 109 for cultivation and manufacturing operations. Hundreds more hold provisional licenses, and the CCC received more than 22,000 license applications since it was granted governing powers in 2017, it said in its latest annual report last October.
Vantage Builders Director of Cannabis Margaret Cachel said her firm has built 13 cannabis spaces in Massachusetts alone and has constructed marijuana facilities from Florida to New Hampshire.
“Massachusetts is a hot market because some of the western states like California, Oregon and Colorado are saturated already,” she said. “Investors coming from out of state feel very comfortable investing in Massachusetts. It’s well-organized.”
That demand will continue to generate interest in the state's old mills — developers are also looking to reposition warehouses that held operations of the state's furniture-making industry north of Boston, Cachel said.
"We kind of inherited all those mills and they're just standing," Cachel said. "They have a lot of investors who are buying them, we'll convert them."
Industry players projected a slowdown around 2020 after a burst out of the gate two years prior, but the coronavirus pandemic put those concerns at bay, McGeorge said. Facilities continue to be announced and the landscape will be clearer when they begin to deliver by 2023.
“There’s a lot of large operators coming online as the dispensaries get constructed,” McGeorge said. “At some point, they’ll hit a saturation point. We think that’s a couple of years out at this point.”