Auto Crash Risk Grows, UK Logistics Property Beware
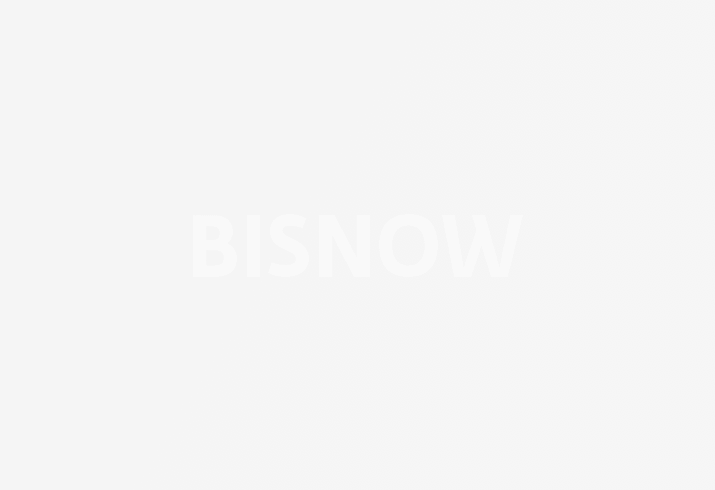
The near collapse of Britishvolt, narrowly averted this week as employees agreed to take a pay cut, has sent an electric shock through the UK auto sector. It could also spark trouble for logistics property.
Britishvolt has been behind the most advanced plans yet for a UK gigafactory. Without gigafactories producing electric vehicle batteries, the UK auto industry’s transformation to a post-fossil fuel future becomes much harder.
Britishvolt was in the process of creating a plant at Blythe, in the north east of England. It would have provided 30 gigawatt-hours of battery capacity, roughly a third of the 98GWh capacity the UK domestic car industry is expected to need by the start of the next decade. Today the UK generates just 2GWh, with a handful of plans for gigafactories. None are far advanced.
The £1.7B Blythe proposal had secured the promise of £100M from the UK government as well as likely private sector backing from abrdn and Tritax. But with the start of production repeatedly pushed back to 2025, and no obvious revenue source, the business began to wobble.
The Britishvolt drama played out as BMW said it was to relocate the production of 40,000 electric Mini cars from Oxford to China, thanks to poor electric vehicle infrastructure in the UK. Honda also abandoned the UK as it contemplated a move to electric vehicles in 2016.
The UK auto industry has been haemorrhaging since the Brexit vote in 2016. Latest data shows that UK car production fell a further 6% in September with 63,125 vehicles built. This produced a rolling annual total of 777,000 vehicles. This contrasts with a rolling total of 1.7M vehicles built in the year to September 2016, and a sharp fall in this total every year since.
The impact for the logistics property sector in the Midlands could be painful. Britishvolt signed with Prologis to occupy a £200M centre of excellence as part of a Midlands 'Battery Corridor' in May 2022.
Plans for a 4.5M SF gigafactory in Coventry were launched in 2021 but have not moved fast.
Constraints on the supply of power in the UK — the result of poor infrastructure, rather than the Russia-Ukraine War — are expected to hinder development. Late last year Savills estimated that gigafactory supply chains could generate 50M SF extra demand for industrial and warehouse space by 2040, requiring up to 2,500 acres of development land with 150MVA power connections.
But the firm warned that without that additional well-powered land, the drive for rapid electric vehicle growth could fall flat.
“So far in 2022, take-up in the West Midlands within the auto sector logistics has been around 5%. The Britishvolt deal at Hams Hall was the largest this year in terms of size at circa 260K SF,” Gerald Eve senior surveyor Skye Andrews told Bisnow.
“The 5% total is a decline from previous years, such as 2017, which witnessed a 39% take-up, driven by Jaguar Land Rover who took a large facility in Solihull Damson Parkway of 988K SF. This is not surprising, as in 2016 the number of annual new cars registered and used vehicles sold was the highest on record. 2019 saw a 21% take-up, which again saw Jaguar Land Rover taking another circa 400K SF and IAC with two separate buildings of 77K SF and 234K SF.”
The UK auto sector will stop producing petrol and diesel engines in 2030.